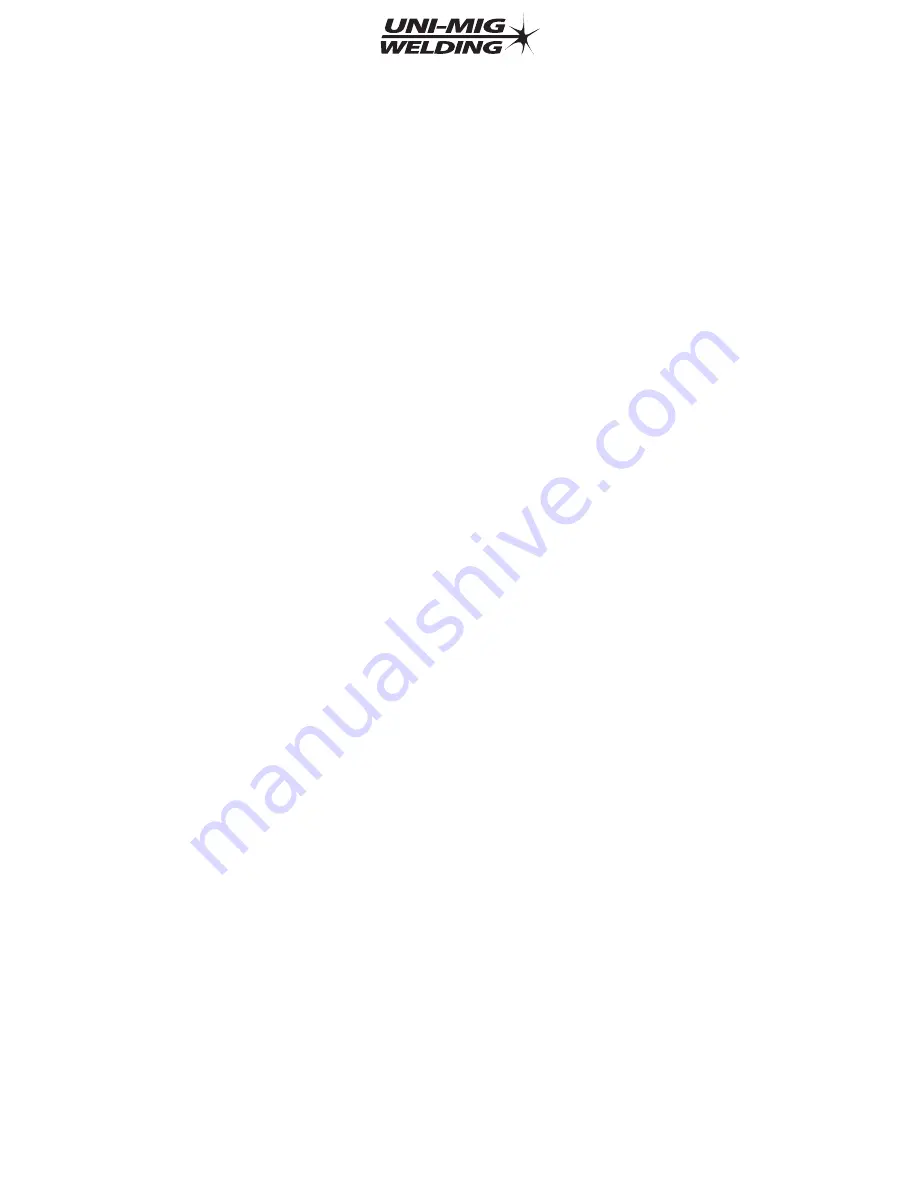
4. Pass the wire through the guide, over the drive roller and into the
torch liner.
· Push about 10-15 cm into the torch liner.
5. Lower the arm and replace the tensioning knob.
· Tighten the tensioning knob sufficiently to hold firmly, but do not fully tighten.
NOTE: Correct tension will allow the wire to feed into the torch liner smoothly,
but will allow the drive roller to slip in the event of a blockage.
6. Close the side panel of the welder.
7. Pull off the torch shroud with a twisting movement, then unscrew the contact tip.
8. Connect the welder to the power supply and switch ON.
9. Set the ‘WIRE FEED’ rotary control on the front panel to position 7 or 8 and squeeze
the trigger on the torch body.
· The wire will feed through the MIG Torch until it appears at the torch tip.
· Ensuring the hose is free from kinks during this process will assist the wire in its
passage through the hose liner.
10. Release the trigger and switch off the welder and disconnect the machine from the
mains supply.
11. Refit the appropriate size contact tip (0.8 mm is supplied fitted) to suit your wire.
then replace the shroud.
12. Trim the welding wire so that it protrudes no more than 5 mm -10mm from the end
of the gas nozzle.
MIG WELDING PRINCIPLES
MIG (Metal Inert Gas) welding allows you to weld together two similar metals.
A consumable wire electrode is continuously fed through the welding torch that is fitted
with a concentric gas nozzle. The wire is connected to a voltage supply which creates
an electric arc between the electrode (the wire) and the workpiece. The arc is used to
create the required heat to turn the metal into a molten state. The wire is used as both
the electrode and as a filler.
The argon mix / CO2 inert gas is used to prevent oxidation and to shield the arc and the
weld from atmospheric contamination. The choice of gas is dependent upon the
material being welded,
When using the welder in a gasless configuration the shielding gas is created
from the flux within the welding wire. When using the welder outside, you may need to
erect a wind break to make sure the shielding gas is not blown away, thereby leaving a
poor quality weld.
UNI-PLAS
UNI-PLAS