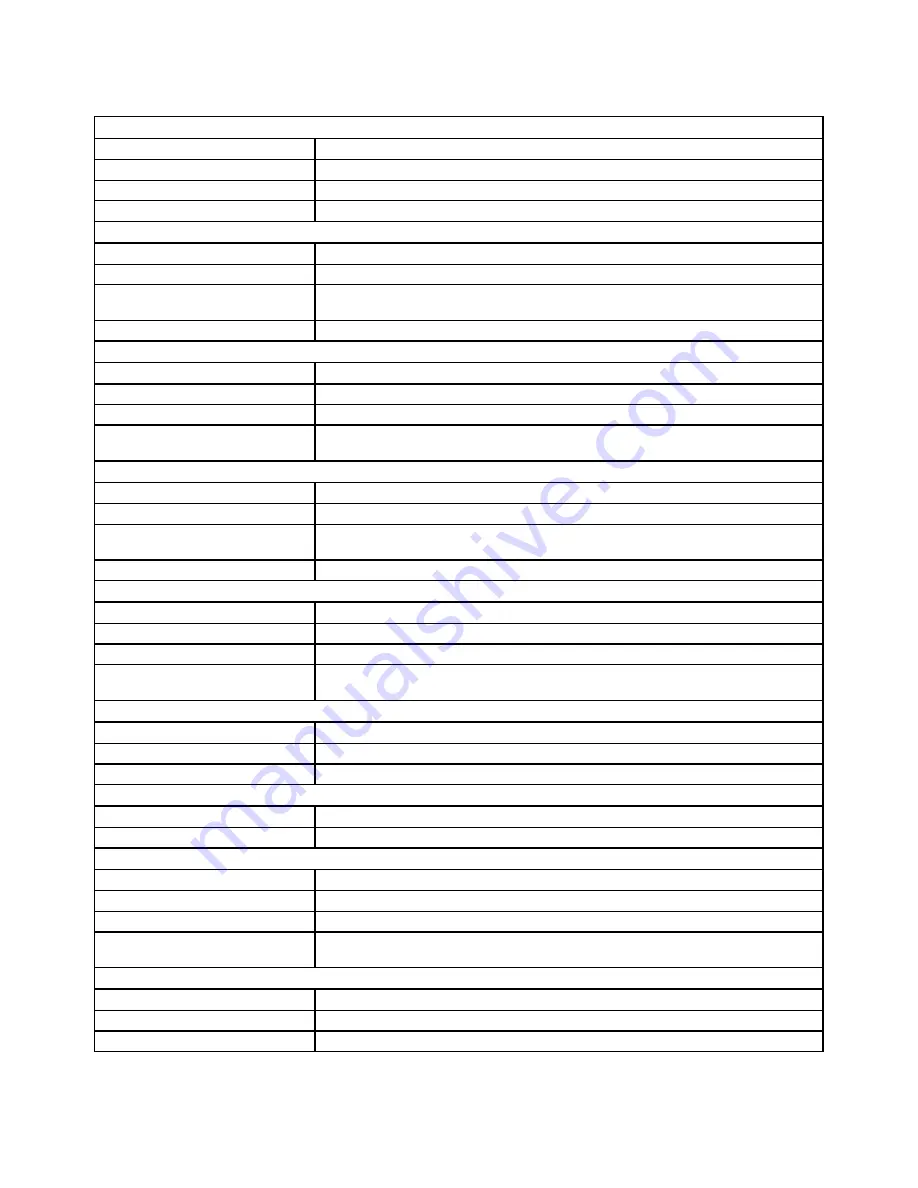
21
20
1: No arc
Possible Reason
Suggested Remedy
Incomplete welding circuit
Check earth lead is connected. Check all cable connections.
Wrong mode selected
Check the MMA selector switch is selected
No power supply
Check that the machine is switched on and has a power supply
2: Porosity − small cavities or holes resulting from gas pockets in weld metal.
Possible Reason
Suggested Remedy
Arc length too long
Check that pure Argon is being used
Work piece dirty, contaminated or
moisture
Remove moisture and materials like paint, grease, oil, and dirt, including mill scale from
base metal
Damp electrodes
Use only dry electrodes
3: Excessive Spatter
Possible Reason
Suggested Remedy
Amperage too high
Decrease the amperage or choose a larger electrode
Arc length too long
Shorten the arc length
Tungsten melting into the weld pool
Check that correct type of tungsten is being used. Too much current for the tungsten
size so reduce the amps or change to a larger tungsten
3: Weld sits on top, lack of fusion
Possible Reason
Suggested Remedy
Insuf cient heat input
Increase the amperage or choose a larger electrode
Work piece dirty, contaminated or
moisture
Remove moisture and materials like paint, grease, oil, and dirt, including mill scale from
base metal
Poor welding technique
Use the correct welding technique or seek assistance for the correct technique
4: Lack of penetration
Possible Reason
Suggested Remedy
Insuf cient heat input
Increase the amperage or choose a larger electrode
Poor welding technique
Use the correct welding technique or seek assistance for the correct technique
Poor joint preparation
Check the joint design and t up, make sure the material is not too thick. Seek assist-
ance for the correct joint design and t up
5: Excessive penetration - burn through
Possible Reason
Suggested Remedy
Excessive heat input
Reduce the amperage or use a smaller electrode
Incorrect travel speed
Try increasing the weld trav
e
l speed
6: Uneven weld appearance
Possible Reason
Suggested Remedy
Unsteady hand, wavering hand
Use two hands where possible to steady up, practise your technique
7: Distortion − movement of base metal during welding
Possible Reason
Suggested Remedy
Excessive heat input
Reduce the amperage or use a smaller electrode
Poor welding technique
Use the correct welding technique or seek assistance for the correct technique
Poor joint preparation and or joint
design
Check the joint design and t up, make sure the material is not too thick. Seek assist-
ance for the correct joint design and t up
7: Electrode welds with different or unusual arc characteristic
Possible Reason
Suggested Remedy
Incorrect polarity
Change the polarity, check the electrode manufacturer for correct polarity
The following chart addresses some of the common problems of MMA welding. In all cases of equipment malfunction,
the manufacturer’s recommendations should be strictly adhered to and followed.
MMA (Stick) WELDING TROUBLE SHOOTING
21
20