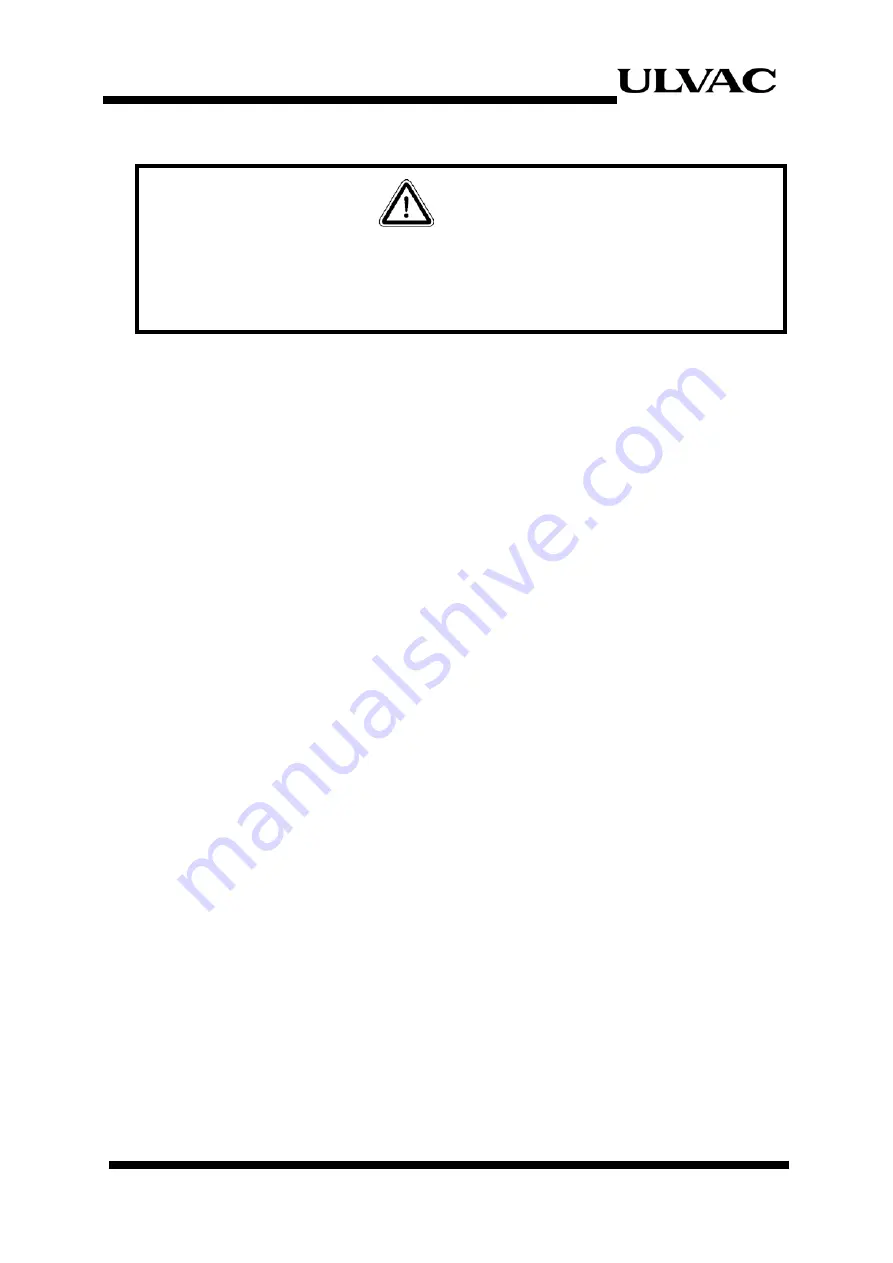
30
ULVAC CRYOGENICS INCORPORATED
9.3 Disconnecting Manual Dispense Flexible Hoses
Disconnect flexible hoses in the opposite way of connecting. Push down the outer
ring of the MP-300K side joint and pull out the flexible hose to disconnect.
CAUTION
When disconnecting flexible hoses, make sure that they return to room temperature.
Note that disconnecting hoses right after dispensing liquid nitrogen may result in
damaging the O-ring inside the coupler joint.