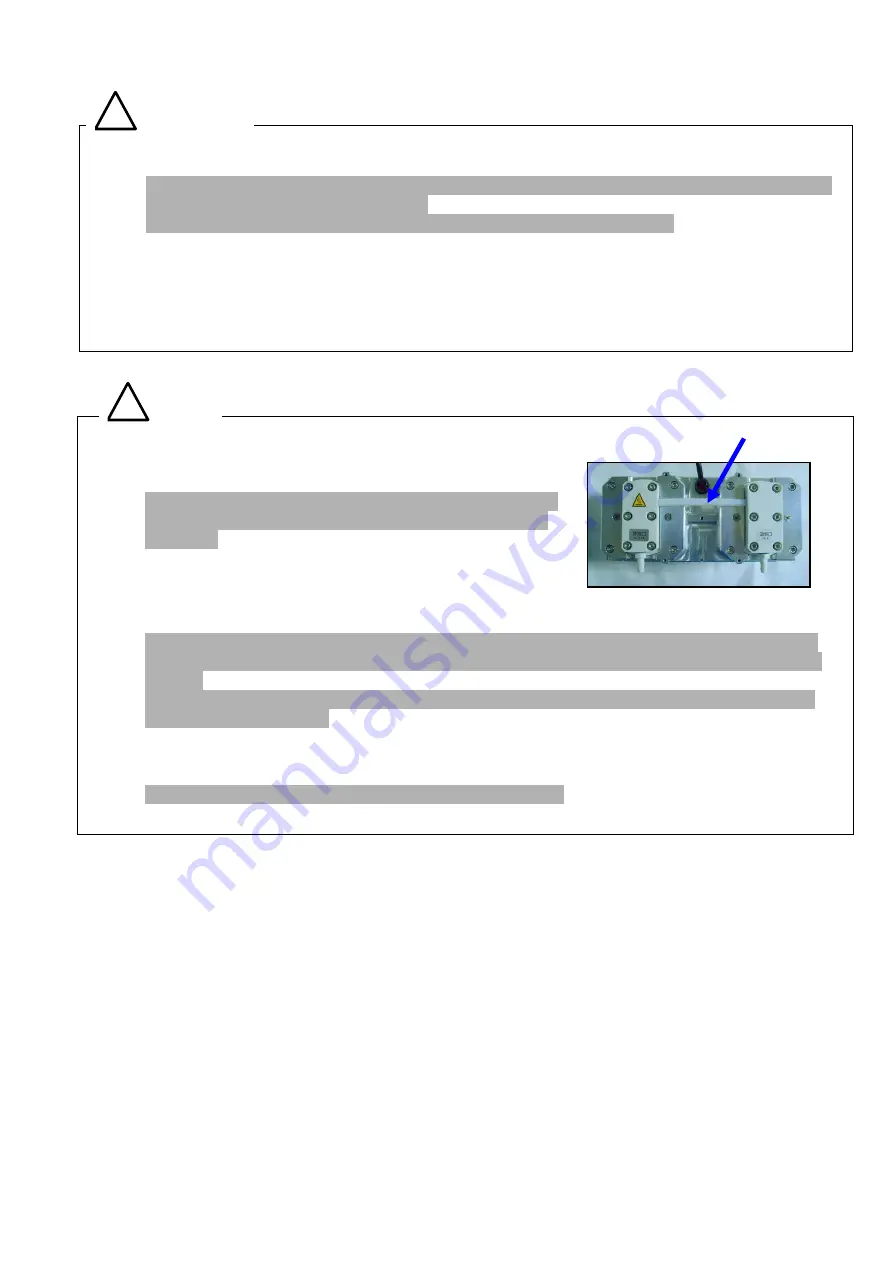
06
Maintenance and Repair
(9) Dispose in accordance with legislation for disposal and cleaning of waste products, handle as
industrial waste, and do not incinerate.
Toxic fluorine gas is generated by incineration of fluorine-based plastics.
(10)
If the pump ceases operation, turn power OFF (set switch to O) immediately to prevent
accidents, remove the power cord from the wall outlet, and contact your dealer or the
manufacturer for inspection and repair.
(11) Leave the pump for at least 30 minutes until it has cooled, and begin operation again. Touching
the pump immediately after it has stopped may result in burns.
Installation
(1) The pump may malfunction if it is subjected to shocks or
tipped over on its side.
(2) Do not hold or push the tube at the top of the pump (see
below). Damage to the tube may affect performance of
the pump.
Applications
(3) This pump is not designed to be corrosion-proof. Use it only with clean air at normal
temperature, or with gases of equivalent characteristics.
(4) This pump is designed for general corrosion resistance, however it is not resistant to molten
alkali metals such as molten sodium, to fluorine at high temperatures, and to some oxides of
fluorine.
(5) Corrosion-resistant plastic is used in the external covering of the DTC-41K however it is not
resistant to all chemicals.
Ensure that the following chemicals do not come in contact with the pump. Any chemical,
including the following, which comes into contact with the pump should be wiped off
immediately.
• Acetone • Ethyl ether • Ethyl acetate • Animal fats
!
Caution
!
Note