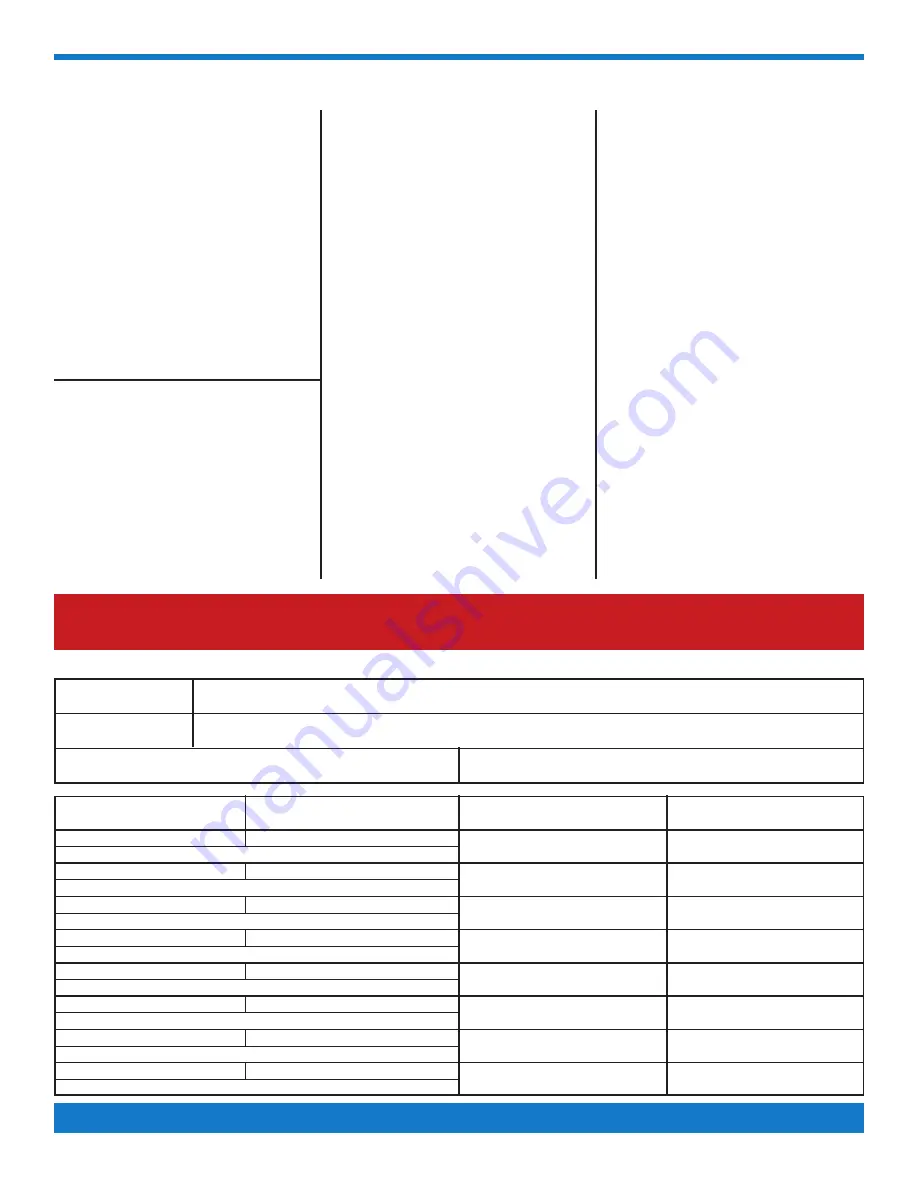
3
General -
1. Check for wear and deterioration.
Before each use, carefully inspect your harness for
signs of wear, deterioration, or evidence of impact
loading. Visually inspect for loose threads, pulled
rivets, burns, cuts, distortions, abrasions, or any other
evidence of chemical or physical deterioration that
may have weakened the material or assembly.
2. Inspect hardware for malfunctions and cracks.
Check all snap hooks, buckles and D-Rings.
3. Remove from service and replace all worn
or damaged equipment.
If any part does not pass inspection, immediately
remove the harness from service and destroy.
Specific -
1. Stitching and webbing.
Check stitching for broken, burned, cut or pulled
stitches. Broken strands appear as tufts on the surface.
To inspect, hold the webbing with your hands six to
eight inches apart. Bend the webbing in an inverted
U to cause surface tension, exposing problem areas.
Inspect all web areas. Damage from cuts, abrasion,
corrosives, heat or chemicals should be apparent.
2. Buckle and belt ends.
Inspect the ends of all straps. They are subject to
wear as a result of repeated opening and closing.
Enlargement or distortion of holes may indicate
excessive wear or possible damage through impact
loading. Harnesses with unusually enlarged or
distorted holes should fail inspection.
3. D-Rings.
All D-Rings should be checked for distortion. D-ring
attachment points should be checked for unusual
wear or damaged Fibers. Badly pitted D-rings indicate
chemical corrosion, and the equipment should
fail inspection.
4. Stitching or rivets at hardware attachment points.
For stitched attachment points, check that stitching
is not broken, burned, cut or pulled. Check all riveted
attachment points for tightness. Badly pitted rivets
indicate chemical corrosion, and the equipment
should fail inspection.
5. Tongue buckles.
All tongue buckles should be checked for distortion,
sharp edges and cracks. The tongue should move
freely and overlap the frame. Rollers should not be
distorted and should roll freely.
6. Friction slide adjusters.
Friction slide adjusters should be checked for sharp
edges, distortion. Make sure that the outer bars and
center bars are straight. Also check corners and
attachment points for wear and cracks.
7. Easy-connect buckle.
Easy-connect buckle (square rings) should be checked
for distortion, sharp edges and cracks. For stitched
attachment points, check that stitching is not broken,
burned, cut or pulled.
8. Friction style buckle.
Friction style buckles should be checked for sharp
edges, cracks and distortion. Make sure outer bars
and center bar are straight. Also check corners
and attachment points for wear.
9. Leather.
Leather should be soft and supple. Visually check
leather for cracks tears, burns, brittleness or other
signs of damage age or abuse. While the leather
components of the system are not load bearing,
damage to the leather is a sign that the entire harness
MAY NOT be in acceptable condition. Re-inspect
entire system. Leather should both look and feel good.
1O. Destroy or replace worn or damaged Harnesses.
If evidence of excessive wear, deterioration or
mechanical malefaction is observed; the harness
should be destroyed. Never work with worn or
damaged equipment. Using damaged or worn
equipment can cause serious injury or death.
11. The inspector is the most important part
of any inspection procedure.
Check all equipment thoroughly and follow all safety
procedures and guidelines. Don't take any shortcuts.
Harness System Inspection Procedures
Serial Number:
Model Number:
Date Purchased:
Inspection Date
Inspection Items Noted
Corrective Action
Maintenance Performed
Date of First Use:
INSPECTION AND MAINTENANCE LOG
IMPORTANT NOTE:
OSHA specifies that all employers covered by the Occupational Safety and Health Act are responsible for inspection and
maintenance of all tools and equipment used by employees, whether owned by the employees or by the company. All Ultra-Safe equipment
should be inspected before each use, and immediately removed from service if equipment does not pass inspection.
Approved By:
Approved By:
Approved By:
Approved By:
Approved By:
Approved By:
Approved By:
Approved By: