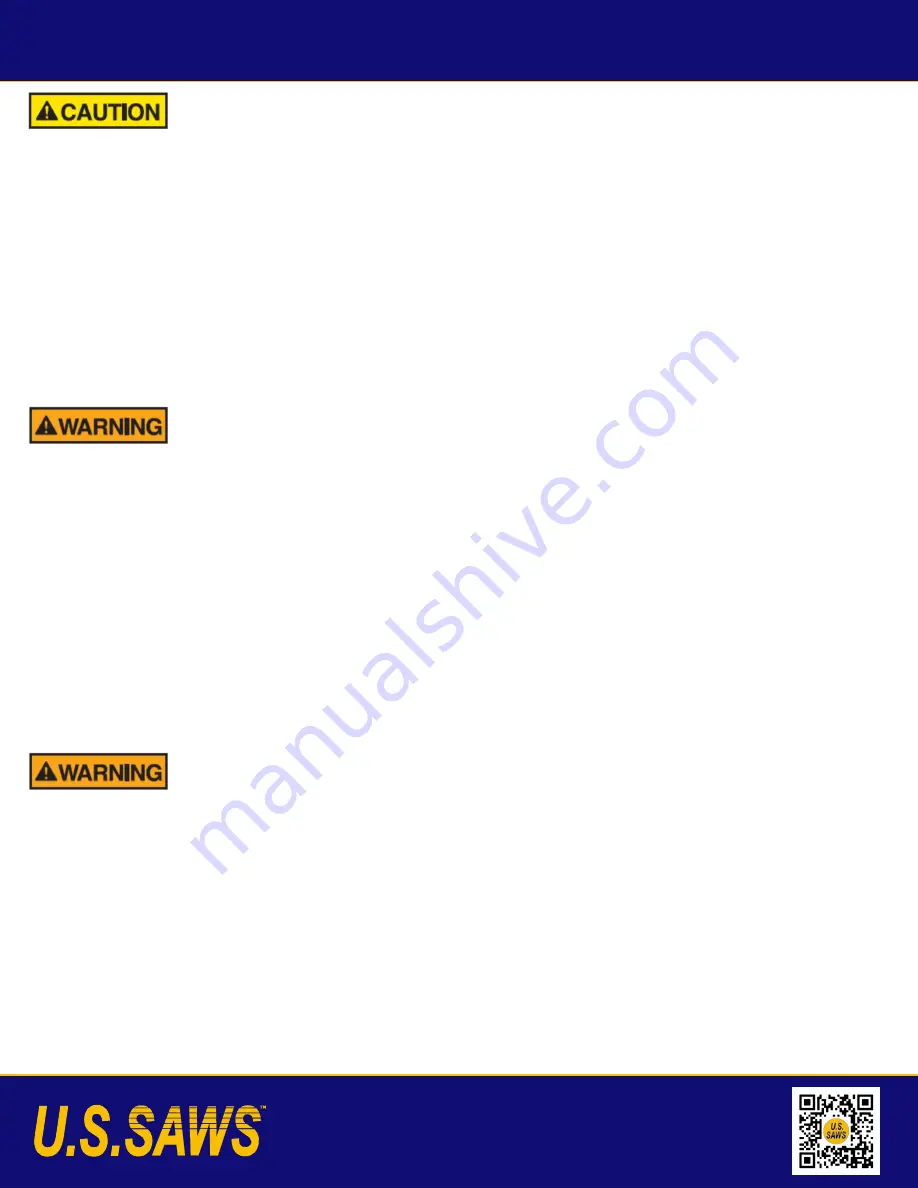
OPERATION
6.1.3
Place one wrench on the drive flange to hold the blade shaft in
place. Place the other wrench on the blade nut and turn counter-clockwise to
loosen the nut.
6.1.4
Unscrew the blade nut. Slide the outer flange, spacers and blade off
the shaft.
6.1.5
Replace blade, spacers, and outer flange. Outer flange pin must line
up with all spacers and drive flange to fit through properly.
WARNING:
Be sure that the flanges, and blade are clean and undamaged
before mounting. Do not use damaged parts. The CC-100 maximum blade
operating speed is 7500 rpm as labeled on the blade guard. The CC-100 shaft
diameter is 1 inch. Therefore, only use dry cut diamond blades rated for higher
than 7500 rpm maximum safe speed and designed for 1-inch diameter shafts.
Using a non dry cut diamond blade or a blade rated below 7500 rpm could
result in severe blade failure, personal injury or death. See Figure 28 and Fig-
ure 29. Never cut material for which the blade was not designed. Check blade
manufacturer’s guidelines on material to be cut. Never operate a blade in the
wrong rotation direction. Verify blade direction when changing blades.
6.1.6
Screw on and tighten the blade nut with wrenches making sure the
face is flat against the outer flange. The blade shaft should be flush or slightly
stick out beyond the blade nut to ensure all the blade nut threads are en-
gaged. The outer flange pin should not touch the CC-100 chassis and 1/2” hex
bolts when rotating. Rotate blade by hand to verify proper clearance and that
the blade runs true (without wobbling). See Figure 30 and Figure 31. Never
use a blade with interference or that does not run true.
6.1.7
Always run a CC-100 with the blade guard in the down position.
WARNING:
Breathable silica may be generated by use of this product; Silica
can cause severe and permanent lung damage, cancer, and other serious dis-
eases. Do not breath the dust. Do not rely on your sight or smell to determine
if the dust is in the air. Silica may be in the air without a visible dust cloud. If
air monitoring equipment for silica is not provided by your employer at your
worksite, you MUST wear appropriate respiratory protection when using or ser-
vicing the machine. Consult your employer and OSHA regarding the appropriate
respiratory protection.
6.2
Adjusting dust brush height and 2 inch blade guard caster wheel
6.2.1
The dust brush should firmly touch the ground to prevent excessive
dust from escaping into the surrounding work area.
8
6.2.2
With engine in the OFF position, loosen the 3/8-inch hex nut by turn-
ing it clockwise. Then turn the caster adjustment nut counterclockwise to lower
the dust brush or clockwise to raise the dust brush.
6.2.3
With the dust brush in the desired position, tighten the 3/8-inch hex
nut by turning it counterclockwise.
6.3
Checking and adjusting belt tension
6.3.1
The belt tension should be checked after the first hour of operation
on a new CC-100 or new belt. On a used CC-100, the belt tension should be
checked once a day. With engine in the OFF position, remove the four 5/16”
hex bolts that attach the belt guard to the chassis.
6.3.2
Remove the belt guard. The belt should deflect no more than 1/16”
under moderate finger pressure equidistant between the sheaves.
6.3.3
To tighten the belt, loosen the four 5/16” hex nuts that hold the
Honda engine to the chassis. Then, turn the 3/8” hex head bolt clockwise on
the front of the CC-100.
6.3.4
After reaching the desired belt tension, verify that the belt sheaves
are properly aligned and the belt is straight. Retighten the four 5/16” hex nuts
that hold the engine against the chassis.
6.3.5
Replace the belt guard with the four 5/16” hex bolts that were
removed in step 6.3.1. Never run a CC-100 without the belt guard in place.
6.4
Bearing lubrication
6.4.1
With engine in the OFF position, slowly tilt the CC-100 back until the
handle rests on the ground.
6.4.2
These bearings are exposed to excessive dust and require the
same brand of high quality grease as supplied by the factory. Apply ALVANIA®
Grease 3 with a hand grease gun to both flanged bearings on the blade shaft
after every 100 hours of use.
6.4.3
The performance of the bearing is greatly influenced by the quantity
of grease. For optimum performance, insert grease until a little bleeds out
from between the outer ring raceway and the perimeter of the slinger. Wipe off
excess grease.
6.4.4
Slowly tilt the CC-100 forward until all wheels are back on the work
surface.
6.5
Honda engine maintenance
6.5.1
See the section titled “Servicing your Honda engine” in the Honda
Engines Owner’s Manual. This section includes
detailed information on:
6.5.1.1
The importance of maintenance
6.5.1.2
Maintenance safety and precautions
6.5.1.3
Maintenance schedule
6.5.1.4
Refueling
6.5.1.5
Engine oil level check, oil change, and recommendations
6.5.1.6
Air filter inspection
6.5.1.7
Air cleaner service
6.5.1.8
Sediment cup cleaning
6.5.1.9
Spark plug service
6.5.1.10
Idle speed adjustment
6.6 Transportation
6.6.1
Allow the CC-100 blade guard, blade, engine, and engine muffler to
cool.
6.6.2
See the section titled “Helpful tips and suggestions - Transporting”
in the Honda Engines Owner’s Manual.
6.6.3
With engine in the OFF position, securely strap down CC-100 to ship-
ping pallet, trailer bed, etc. in normal upright position.
6.7 Troubleshooting
6.7.1
See the three sections titled “Helpful tips and suggestions, Taking
care of unexpected problems, and Technical and consumer information” in the
Honda Engines Owner’s Manual.
6.7.2
See Rx for Diamond Blade Safety by the Masonry and Concrete Saw
Manufacturers Institute for diamond blade
troubleshooting.
Surface Prep
Division
P: 877-817- 6687 F: 813-621-7125
Visit us at www.ussaws.com
CAUTION:
Running the CC-100 generates heat in the engine, engine muffler,
blade and blade guard. Do not touch these components without proper heat
protecting work gloves.
6.1
Removing and installing the blade
6.1.1
With engine in the OFF position, loosen the clamping knob and
remove both 1-1/2” blade change wrenches from the CC-100 handle.
6.1.2
Remove bolt in the blade guard holding bracket. Hold the blade
guard firmly and raise guard up into the holding bracket. Reinsert bolt in the
blade guard holding bracket and tighten nut.