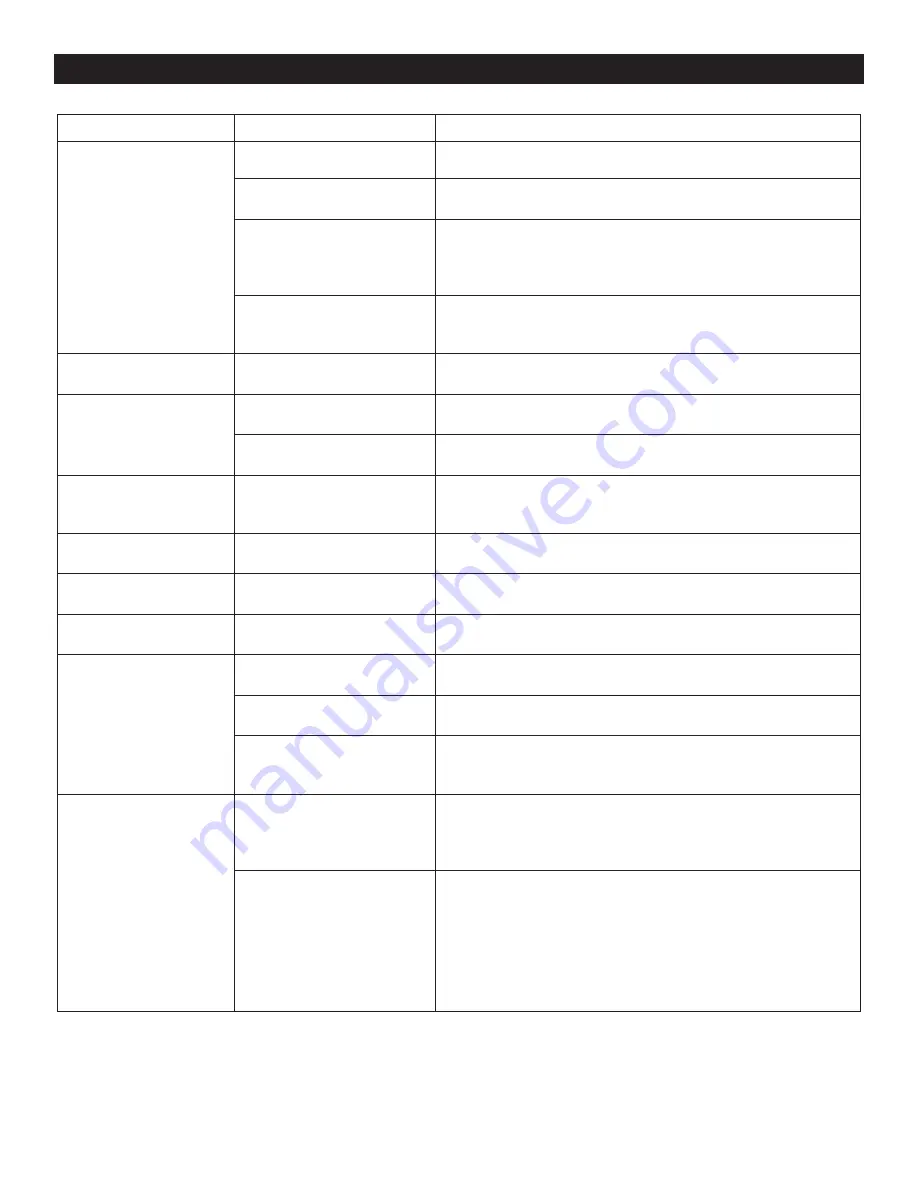
PAGE 6 OF 18
0518 IH-6323
ISSUE
POSSIBLE CAUSE
RESOLUTION
General print quality
issues - the printed
image does not look
right.
The printhead is dirty.
Clean the printhead. See Cleaning the Printer.
You may be using the
wrong power supply.
Verify you are using the power supply that came with this
printer.
The printhead has worn out.
Replace the printhead. The printhead is a consumable item
and will wear over time due to friction between the media
and printhead. Using unapproved media may shorten
printhead life or damage your printhead.
The platen (drive) roller
may need cleaning or
replacement.
Clean or replace the platen (drive) roller.
No print on the label.
Media has been loaded
incorrectly.
The media printable surface must face up towards the
printhead. Follow the instructions for Loading Media Roll.
Loss of printing
registration on labels.
Excessive vertical drift in
top-of-form registration.
The platen (drive) roller is
dirty.
Clean the printhead and platen roller. See Cleaning the
Printer.
The media is loaded
incorrectly.
Load media correctly. See Loading Media Roll.
Printing too light or too
dark over the entire
label.
The media or ribbon is not
designed for high-speed
operation.
Replace supplies with those recommended for high-speed
operation.
Smudge marks on
labels.
Improper label format.
Check your label format and correct it as necessary.
Mis-registration/skips
labels.
Improper label format.
Check your label format and correct it as necessary.
Vertical drift in top-of-
form position.
The platen (drive) roller is
dirty.
Clean the printhead and platen roller. See Cleaning the
Printer.
Vertical image or label
drift
The platen (drive) roller is
dirty.
Clean the printhead and platen roller. See Cleaning the
Printer.
The media is loaded
incorrectly.
Ensure that the media is loaded correctly. See Loading
Media Roll and Printing a Test Label.
Incompatible media.
You must use media that meets the printer specifications.
Ensure that the inter-label gaps or notches are 3 to 4 mm
and consistently placed.
The barcode printed on
a label does not scan.
There is not enough
blank space around the
barcode.
Leave at least 1/8 in. of blank space around the barcode
(referred to as the quiet zone) and other printed areas on
the label and between the barcode and the edge of the
label. This requirement varies by barcode type.
There is a void or missing
print in a barcode, text or
graphic in a printed form.
Voids can look like a white
bar area in a barcode.
Perform Cleaning the Printer to remove contaminants on the
printheads. Reprint and test the barcode.
Use the Printer and Network Configuration Reports from
Cleaning the Printer to see if the printhead has damaged
printhead elements. Verify that the large black bar on the
bottom of the printed test label does not have any streaks
or voids after thoroughly cleaning the printhead.
TROUBLESHOOTING
π
CHICAGO • ATLANTA • DALLAS • LOS ANGELES • MINNEAPOLIS • NYC/PHILA • SEATTLE • MEXICO • CANADA
1-800-295-5510
uline.com