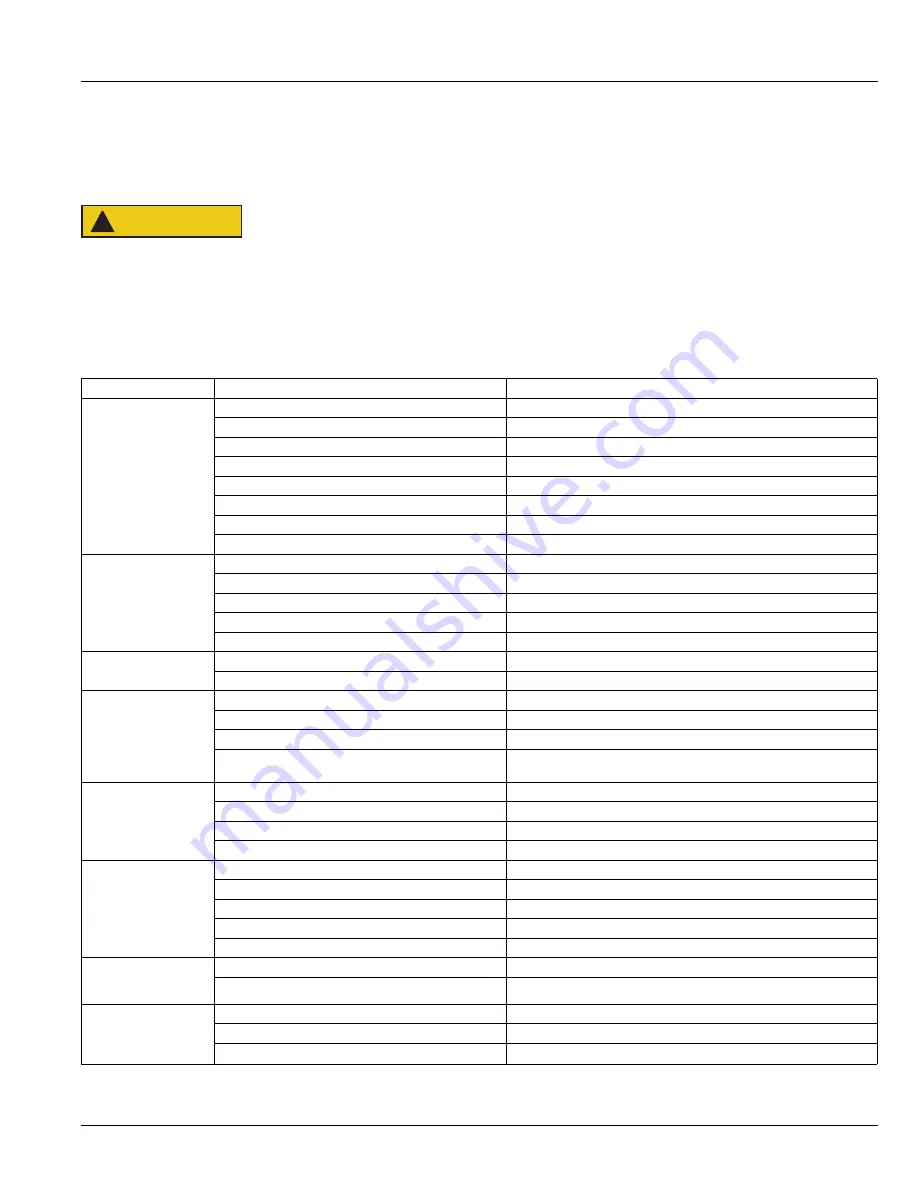
USER GUIDE
Troubleshooting - Extended
SPECIFIC ERRORS & ISSUES
CAUTION
!
Never attempt to repair or perform maintenance
on the unit until the main electrical power has
been disconnected from the unit.
TROUBLESHOOTING GUIDE
Concern
Potential Causes
Suggested Remedy
Will not eject ice
(water frozen).
Control setting too cold.
Adjust control warmer (counterclockwise).
Control inoperable (1-2 contacts open)
Replace control.
Bin switch inoperable.
Replace bin switch.
Limit switch defective (open).
Replace limit switch.
Ice maker assembly motor stalled.
Replace motor.
Broken wire in ice maker circuit.
Repair or replace wiring.
Water soaked cabinet insulation.
Replace foamed cabinet assembly.
Dirty condenser.
Clean condenser.
Will not fill with
water.
Water supply valve closed.
Open water supply valve.
Water switch inoperable (open).
Replace water switch.
Solenoid valve inoperable.
Replace solenoid valve.
Fill tube outlet frozen.
Defrost fill tube.
Broken wire in water fill circuit.
Repair or replace wiring.
Will not stop making
ice.
Bin switch inoperable (closed).
Replace bin switch.
Bin arm binding.
Lubricate bin arm pivot points or loosen bin arm lever screw.
Water will not stop
filling.
Water switch inoperable (closed).
Replace water switch.
Solenoid valve inoperable.
Replace solenoid valve.
Stalled ice maker motor.
Replace motor.
Temperature control inoperable. Ice maker is in
continuous harvest cycle (contacts 1-2 closed).
Replace temperature control.
Ejector blades will not
stop turning.
Control inoperable (1-2 contacts will not open).
Replace control.
Hold switch inoperable.
Replace hold switch.
Broken wiring.
Repair or replace wiring.
Short in mold heater.
Replace heater.
Low ice production.
Control set too cold.
Adjust control warmer (counterclockwise).
Fan motor stalled.
Replace fan motor.
Ice cubes too large.
Lower water fill adjustment.
Dirty condenser.
Clean condenser.
Bypass valve stuck open (Frost Free units only).
Replace bypass valve (Frost Free units only).
Not freezing
(compressor and fan
motors operating).
Little or no frost pattern on evaporator.
Check for sealed system leak or restriction.
Bypass valve stuck open (Frost Free units only).
Replace bypass valve (Frost Free units only).
Not freezing
(compressor not
operating - fans
operating).
Relay inoperable.
Replace relay.
Overload inoperable (open).
Replace overload.
Compressor inoperable.
Replace compressor.
Troubleshooting - Extended 1
37