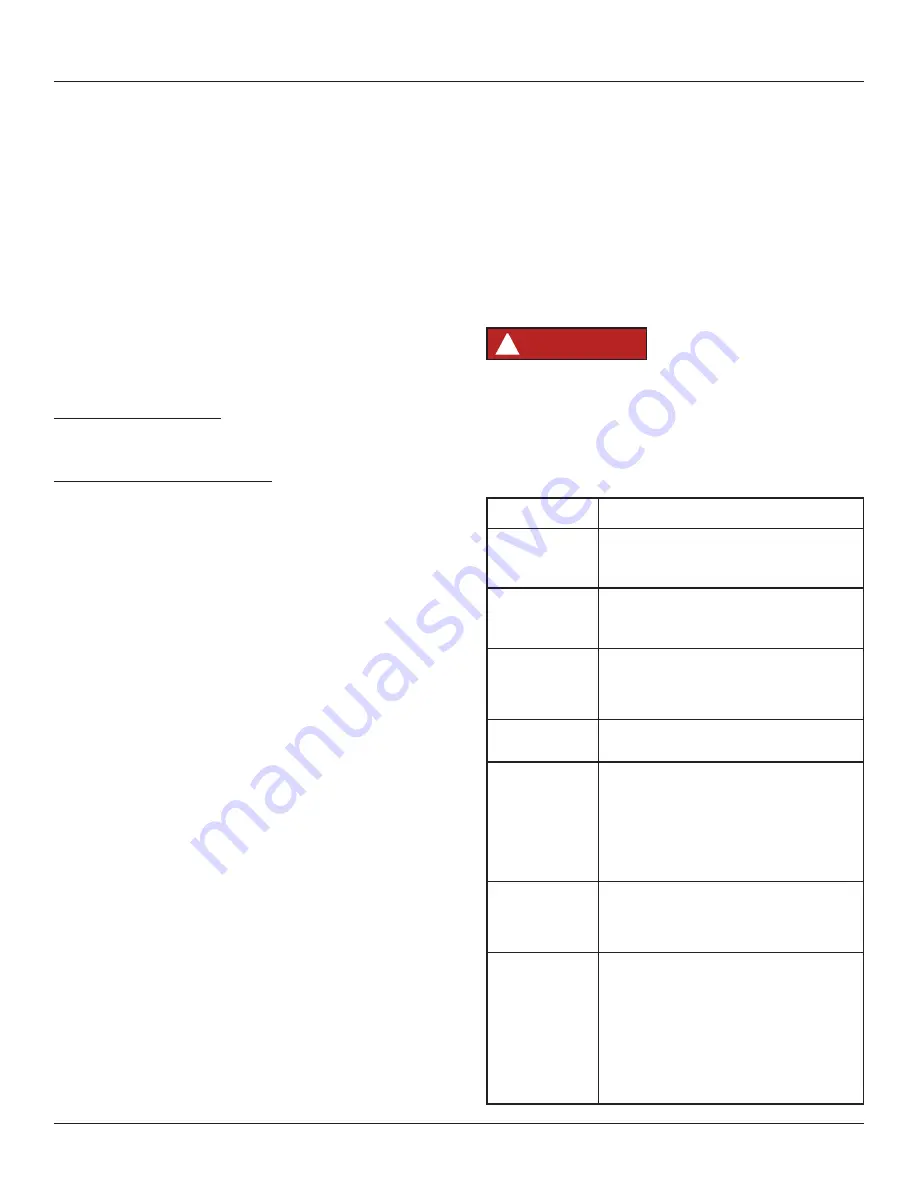
USER GUIDE
Troubleshooting
If you think your U-Line product is malfunctioning, read
the CONTROL OPERATION section to clearly understand
the function of the control.
If the problem persists, read the NORMAL OPERATING
SOUNDS and TROUBLESHOOTING GUIDE sections below
to help you quickly identify common problems and
possible causes and remedies. Most often, this will resolve
the problem without the need to call for service.
If your product needs service, please go to
www.u-line.com/servicers/ and navigate to the
Find a
Servicer
page to locate a U-Line Authorized servicer. Please
make sure to register it at
www.U-Line.com/u-lineregistration. If you have any
issues following this process you can contact the U-Line
Corporation by phone at +1.414.354.0300;
please make
sure
you have your product Model
and
Serial Numbers
handy; They can can be found on the Serial number plate
located within the interior of your product, most often
placed on the ceiling.
All models incorporate rigid foam insulated cabinets to
provide high thermal efficiency and maximum sound
reduction for its internal working components. Despite this
technology, your model may make sounds that are
unfamiliar.
Normal operating sounds may be more noticeable because
of the unit’s environment. Hard surfaces such as cabinets,
wood, vinyl or tiled floors and paneled walls have a
tendency to reflect normal appliance operating noises.
Listed below are common refrigeration components with a
brief description of the normal operating sounds they
make. NOTE: Your product may not contain all the
components listed.
• Compressor: The compressor makes a hum or pulsing
sound that may be heard when it operates.
BEFORE CALLING FOR SERVICE
TROUBLESHOOTING GUIDE
ELECTROCUTION HAZARD. Never attempt to
repair or perform maintenance on the unit
before disconnecting the main electrical power.
Troubleshooting - What to check when problems occur:
NORMAL OPERATING SOUNDS
Troubleshooting
•
Evaporator: Refrigerant flowing through an evaporator
may sound like boiling liquid.
• Condenser Fan: Air moving through a condenser may
be heard.
• Running Water: As your unit continues to produce
ice you will hear water flowing into the collection
chambers and running through the evaporator.
DANGER
!
Problem
Possible Cause and Remedy
Unit Does Not
Operate.
No electrical supply. Plug unit in or
check
circuit breaker.
Light Remains
on When Door
is Closed
Turn off light switch if equipped.
Check reed switch.
Unit Develops
Condensation
on External
Surfaces.
The unit may be exposed to excessive
humidity.
Moisture will dissipate as humidity
levels decrease.
Poor Ice
Quality.
Ice maker system may be dirty. Clean
the ice maker.
No Ice
Production.
Ensure water is being supplied to the
unit.
Verify the bin arm on the ice making
device is not locked in the up position.
If it is, gently push the bin arm down.
See
Ice Maker Production
in the ICE
section of this manual.
Not Enough
Ice.
Ensure the condenser coil is clean and
free of any dirt or lint build-up.
Check ICE section of this manual for
more information.
Water in Ice
Bin.
Ensure unit is not located in excessive
ambient temperatures or in direct
sunlight.
Ensure the door is closing and sealing
properly.
Ensure nothing is blocking the front
grille, found at the bottom of the unit.
Ensure the condenser coil is clean and
free of any dirt or lint build-up.
24