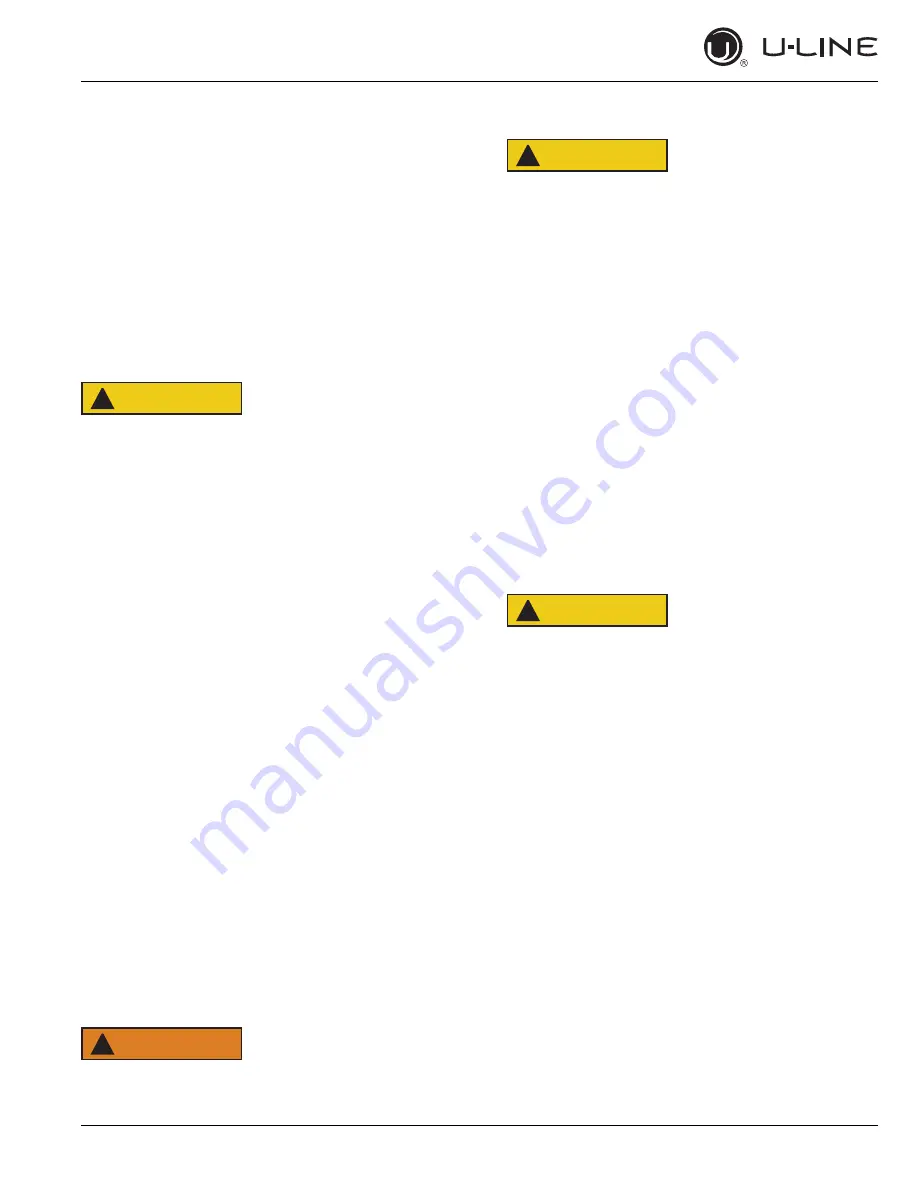
USER GUIDE
Water Hookup 1
u-line.com
SAFETY •
INSTALLATION & INTEGRATION
• OPERATING INSTRUCTIONS • MAINTENANCE • SERVICE
Water Hookup
PREPARE PLUMBING
The water valve uses a standard 1/4" (6.35 mm)
compression fitting. U-Line recommends using accessory
water hook up kit – part # WATERHOOKUP. The kit
includes a 10' (3 m) braided flexible water supply line and
a brass hose fitting. When using a 1/4" (6.35 mm) O.D.
soft copper supply line use the brass nut and sleeve
included with the unit.
CAUTION
!
Plumbing installation must observe all state and
local codes. All water and drain connections
MUST BE made by a licensed/qualified plumbing
contractor. Failure to follow recommendations
and instructions may result in damage and/or
harm.
Water Supply Connection
When connecting the water supply, please note the
following:
• Before installing the unit and connecting to the cold
water supply, review the local plumbing codes.
• The water pressure should be between 20 and 120 psi
(138 and 827 kPa).
• The water line MUST have a shut-off valve in the
supply line.
• The water line should be looped into 2 coils. This will
allow the unit to be removed for cleaning and servicing.
Make certain that the tubing is not pinched or damaged
during installation.
WARNING
!
Connect to potable water supply only.
CAUTION
!
Do not use any plastic water supply line. The line
is under pressure at all times. Plastic may crack
or rupture with age and cause damage to your
home.
Do not use tape or joint compound when
attaching a braided flexible water supply line
that includes a rubber gasket. The gasket
provides an adequate seal – other materials
could cause blockage of the valve.
Failure to follow recommendations and
instructions may result in damage and/or harm,
flooding or void the product warranty.
Use new hose set. Do not reuse old hose set.
CAUTION
!
Turn off water supply and disconnect electrical
supply to unit prior to installation.
Use caution when handling back panel. The
edges could be sharp.
1. Turn off water supply and disconnect electrical supply
to product prior to attempting installation.
2. Remove the grille (plinth strip/base fascia) and access
panel (if equipped) along with back panel.