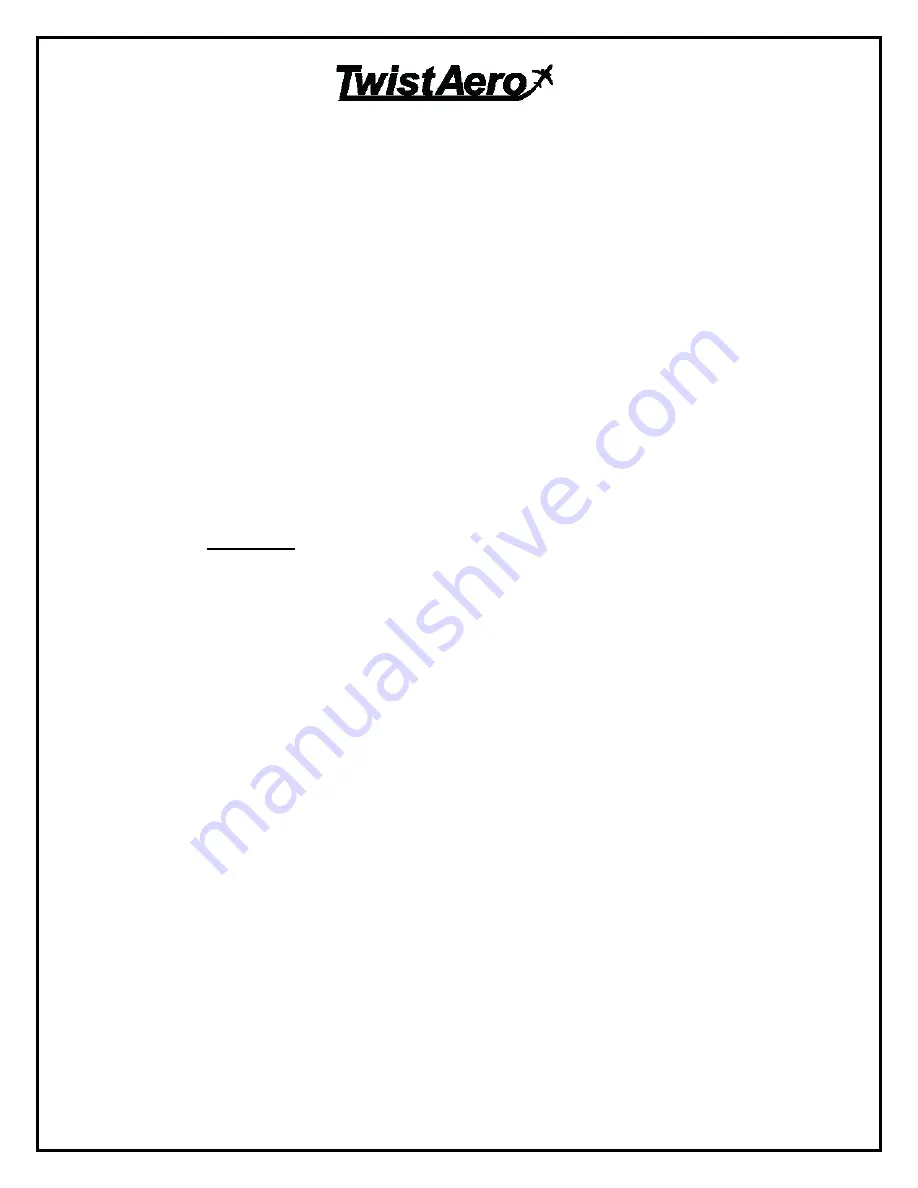
MODEL PCA090480WH
CHAPTER 2
SERVICE
Section 3: Refrigeration Basics and Service
2-3
March 2013
Page 44
Proprietary/Confidential
© 2013 Twist, Inc.
Leaks can occur not only from joints or fittings, but also from line
breakage due to vibration, gasket failure, or other operating
malfunctions.
The common means of pressure testing a system for leaks include the
following:
(1)
If the system is not already charged with refrigerant, it is more
economical and just as effective to slightly charge with refrigerant
and then use an inert gas such as dry nitrogen or dry carbon
dioxide to build up pressure in the system to approximately 175
psig for testing purposes.
WARNING: NEVER USE OXYGEN FOR PRESSURIZING A
SYSTEM; AN EXPLOSION MAY OCCUR IF OIL IS
PRESENT IN THE SYSTEM. ALWAYS USE A GAUGE
EQUIPPED PRESSURE REGULATOR ON THE HIGH
PRESSURE BACK-UP GAS, AND NEVER
INTERCONNECT THE REFRIGERANT CYLINDER AND
THE INERT GAS CYLINDER THROUGH A GAUGE
MANIFOLD. NITROGEN AND CARBON DIOXIDE
CYLINDER PRESSURES CAN RUPTURE A
REFRIGERANT CYLINDER.
The electronic leak detector is the most sensitive type available
and can detect small leaks of a fraction of an ounce per year,
often missed when using other testing methods. Because of their
extreme sensitivity, only use electronic detectors in a clean
atmosphere not contaminated by refrigerant vapor, smoke, vapor
from carbon tetrachloride, or other solvents, which may give a
false reaction.
(2)
Yet another method is by means of soap bubbles. Swab a
suspected leak with liquid soap or detergent, and bubbles will
appear if a leak exists. Despite its simplicity, the soap bubble
method can be extremely helpful in pinpointing a leak that is
difficult to locate.
Property of American Airlines