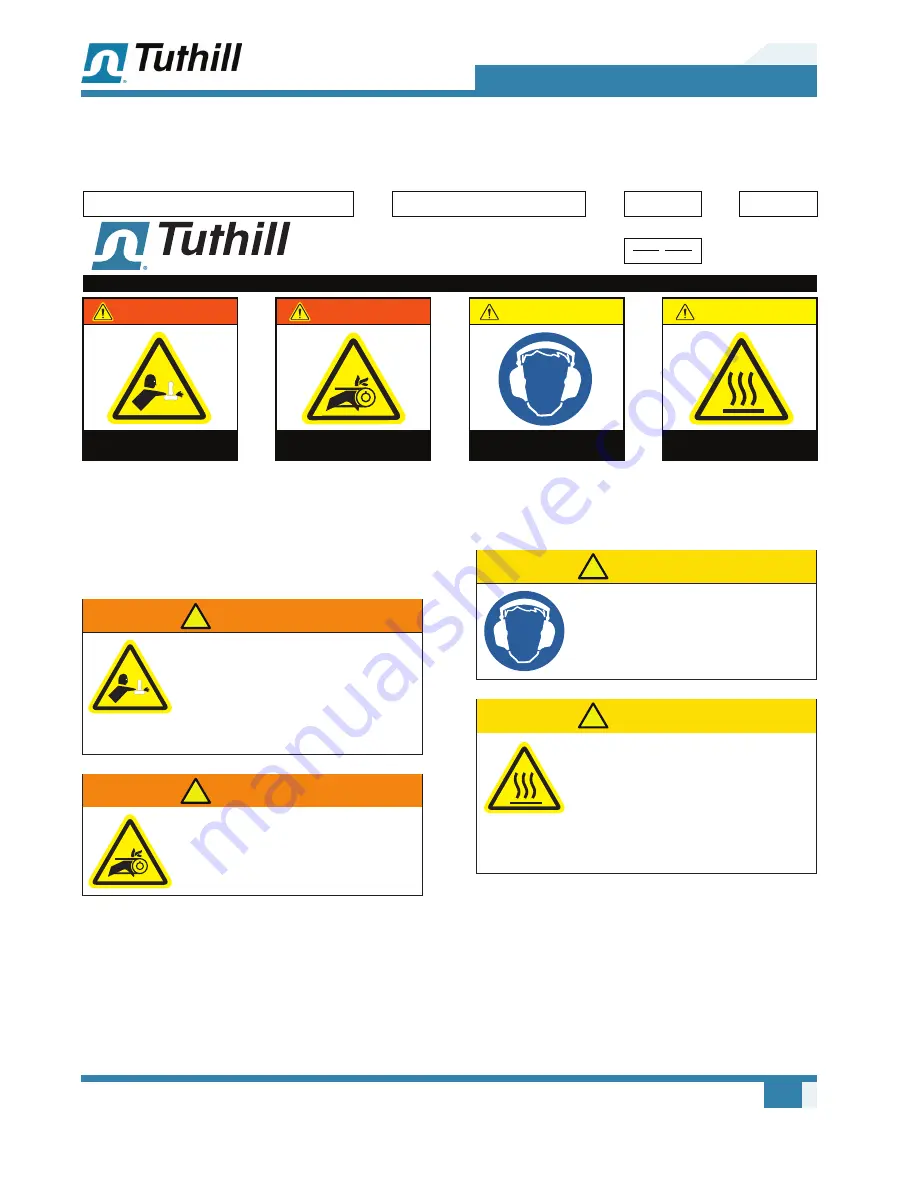
3
02
Conventions and Data Plate
Operator’s Manual 2009 Rev B p/n 2009
DATA PLATE
WARNING
WARNING
CAUTION
CAUTION
http://www.tuthill.com
Hearing protection
required.
Do not touch hot
surfaces.
A
S
U
e
h
t
n
i
e
d
a
M
7
3
9
6
-
5
2
8
)
0
0
8
(
READ INSTRUCTION MANUAL BEFORE OPERATION OR BODILY HARM MAY RESULT
Keep body & clothing away
from machine openings.
Do not operate without
guards in place.
R
E
B
M
U
N
L
A
I
R
E
S
R
E
B
M
U
N
L
E
D
O
M
Tuthill Vacuum & Blower Systems
4840 West Kearney Street
Springfield, Missouri USA 65803
YEAR
MAWP
MAX RPM
Figure 2-1 – General Operation and Symbols on Data Plate
The following information is contained on the data
plate:
WARNING
!
Keep body and clothing away
from machine.
During operation, keep body
and clothing away from inlet
and outlet of the blower.
WARNING
!
Do not operate without guards
in place.
CAUTION
!
Hearing protection is required
while the blower is in operation.
Noise levels may reach as high
as 81 dBA.
CAUTION
!
Do not touch hot surfaces.
Ohe upper limit of the blower
operation is 400°F (205°C). Do
not touch the blower while it is
in operation and assure blower
is cool when not in operation.