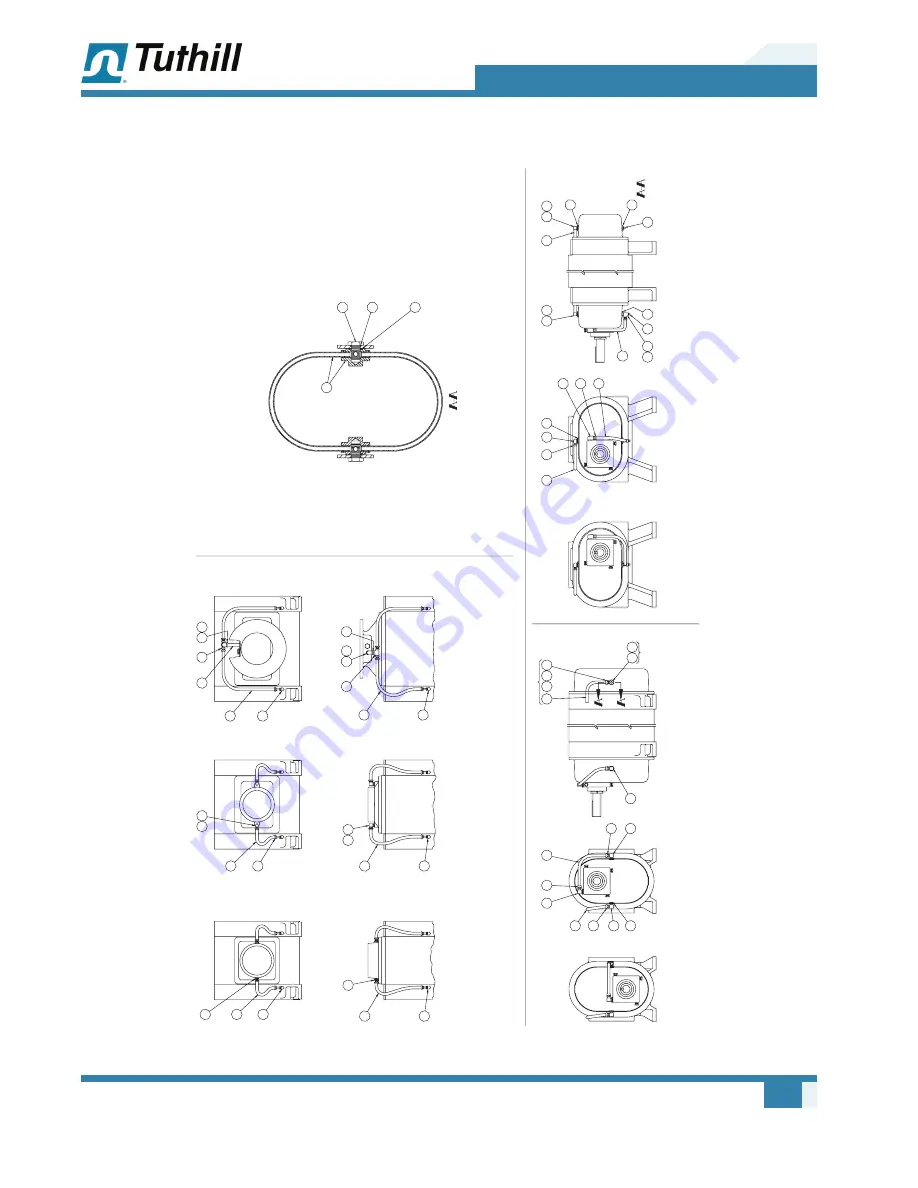
71
Assembly Drawings
Manual 2006 Rev B p/n 2006
Model 5500 – Double Envelope (Cooling Coil Option) – Side and End Views
VENTING DE
TA
IL
HORIZONT
AL
FLOW
BOTT
OM DRIVE
TO
P
DRIVE
VERTICAL
FLOW
HORIZONT
AL
FLOW
NPT
5507
NPT
5507
NPT
551
1
FLANGED
5507, 551
1, 5514, & 5518
NPT
551
1
FLANGED
5507, 551
1, 5514, & 5518
VERTICAL
FLOW
RIGHT DRIV
EL
EFT DRIVE
COOLING COIL
DET
AIL
SCALE: 1/2
VENT
TO
INLET PORT
RIGHT SIDE &
TO
P
INLET SHOWN
(SEE F
ACT
OR
Y
FOR FLOW DIRECTION
)
180
166
180
181
166
273
152
274
181
166
180
120
163
120
159
163
159
120
180
163
159
120
163
159
180
163
159
259
258
132
149
163
159
132
259
149
258
181
274
273
152
166
180
166
272
271
274
166
180
180
166
181
94
95
97
96
97
97
98
THIS SIDE
97
97
FARSIDE
97
SEC
97
SEE SEC
97
98
97
Summary of Contents for M-D Pneumatics PD Plus
Page 6: ...iv Table of Contents Manual 2006 Rev B p n 2006 ...
Page 61: ...55 Assembly Drawings Manual 2006 Rev B p n 2006 Model 3200 Standard Seals Side and End Views ...
Page 64: ...58 Assembly Drawings Manual 2006 Rev B p n 2006 Model 4000 Lip Labyrinth Side and End Views ...
Page 78: ...72 Assembly Drawings Manual 2006 Rev B p n 2006 ...