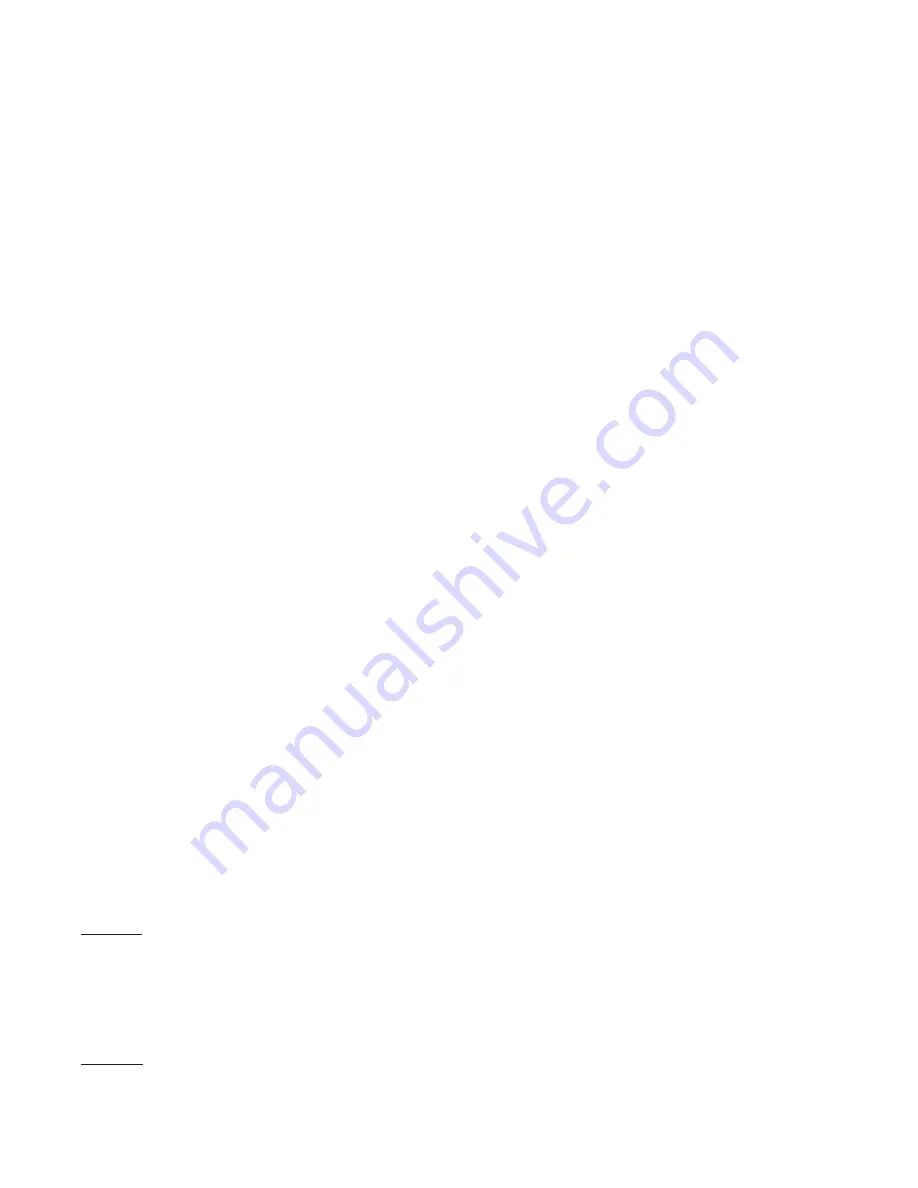
8
pumping corrosive vapors or where excessive operating temperatures are encountered. Boosters with mechanical seals on the rotors
can generally run the full 1500 hours before an oil change is required.
Proper oil drain schedules require oil be changed before the contaminant load becomes so great that the lubricating function of the
oil is impaired or heavy disposition of suspended contaminants occurs. To check the condition of the oil, drain a sampling into a clean
container and check for the presence of water or solids. Slight discoloration of the oil should not necessitate an oil change.
NOTE: When changing oil be sure to reseal the drain and fill plugs. This is especially important on 92/93 series which have no
mechanical seals on the rotors. Air leaks past these plugs can cause rapid loss of oil from end covers resulting in booster failure.
NOTE: Oil levels should be checked every 24 hours of operation.
SPARE PARTS
Refer to the parts list and exploded view for your particular model. Repair kits are available for all models. These kits contain all of
the seals, bearings, O-rings, locks and special retaining screws necessary for an overhaul. Always have the complete booster model
number and serial number when ordering.
In developing a stock of spare parts, consider the following:
•
The degree of importance in maintaining the booster in a “ready” condition
•
The time lag in parts procurement
•
Cost
•
Shelf life (seals and O-rings)
Contact Tuthill Vacuum & Blower Systems Service Department for any assistance in selecting spare parts.
Telephone: (417) 865-8715
Toll Free (48 contiguous states): (800) 825-6937
Facsimile: (417) 865-2950
REPAIR SERVICE
With proper care, Tuthill Vacuum & Blower Systems Mechanical Vacuum Boosters will give years of reliable service. The parts are
machined to very close tolerances and require special tools by mechanics who are skilled at this work. Should major repairs become
necessary, it is strongly recommended that the booster be returned to the factory for repair or to one of the authorized service facilities
that specialize in vacuum booster repair. Contact the factory for the location nearest you. Units which are still under warranty must
be returned to the factory, freight prepaid, for service.
DISASSEMBLY — KMBD-200, 400
NOTE: Items shown in brackets [ ] are referenced to item numbers shown on page 22.
1. Disconnect cooling water lines [274 & 181]. Do not disturb cover bushings [120] or it will be necessary to retest cooling coils for
leakage as described in the assembly procedure. Covers should be retested if water is detected in drain oil. (90/91 series only).
2. Drain oil from both ends of booster and remove inlet and outlet port fittings [38 or 48].
3. Remove spanner lock nut [83], dust washer [82], screws [93], and seal adapter housing [91]. Tap out seal [76] and discard
O-rings [92 & 140]. Remove spacers [77 & 74], adjusting shim [118] and discard O-ring [75].
4. Remove cap screws [26A & 26B] and both end covers [6 & 7]. Two jack screw holes are provided on each cover.
5. Remove lockwire [49], socket head screws [66], and drive shaft [45]. Using puller, remove bearing [50].
6. Remove flat head Allen screws [29] from end of each rotor shaft. Remove washers [25], spacers [57], and oil slinger [21]. NOTE:
The flat head screws have nylok in their threads and may be difficult to remove. Strike the head a couple of blows with a flat face
hammer for easy removal.
7. Mark housing, end plates, rotors, and gears before proceeding with disassembly. There are two methods which can be used to
disassemble the rest of the unit. Method “A” requires an arbor press and method “B” requires the use of bar or yoke pullers. See
puller drawing (T29603) on page 29.
8. Method A:
a. Place two support blocks, 5-1/2 to 6 inches (14 to 15.5 cm) high (hard wood or steel), on the bed of an arbor press. Set
the unit, with the gears pointing down, on the two blocks making sure the blocks support the rotor housing only. Press both
rotors out of free end bearings simultaneously.
b. Lift the housing off the rotors and remove the non-drive end plate [4] by tapping the end plate from the inside of the
housing. Place the rotor housing back over the rotors.
c. Set the unit on the support blocks with the gears pointing upward. Do not extend blocks into the rotor bores. The rotors
may now be pressed from the gear end plate. Do not damage rotors.
Method B:
a. Align timing marks on gears (Figure 6A). Rotate drive gear clockwise approximately three teeth and mark a matching
reference line on each gear as shown in Figure 6B. This gear position is necessary so rotors will clear and not jam. Do not
allow the gears to move from the matched reference line while pulling. Use a light rocking motion to insure that the lobes have
Summary of Contents for KINNEY KMBD Series
Page 21: ...21 ASSEMBLY PRINTS FOR KMBD 200 AND 400 CUTAWAY VIEW ...
Page 22: ...22 ASSEMBLY PRINTS FOR KMBD 200 AND 400 SIDE AND END VIEWS ...
Page 23: ...23 ASSEMBLY PRINTS FOR KMBD 540 AND KMBD 570 CUTAWAY VIEW ...
Page 24: ...24 ASSEMBLY PRINTS FOR KMBD 540 AND KMBD 570 SIDE AND END VIEWS ...
Page 25: ...25 ASSEMBLY PRINTS FOR KMBD 850 1600 2000 AND 2700 CUTAWAY VIEW ...
Page 26: ...26 ASSEMBLY PRINTS FOR KMBD 850 1600 2000 AND 2700 SIDE AND END VIEWS ...