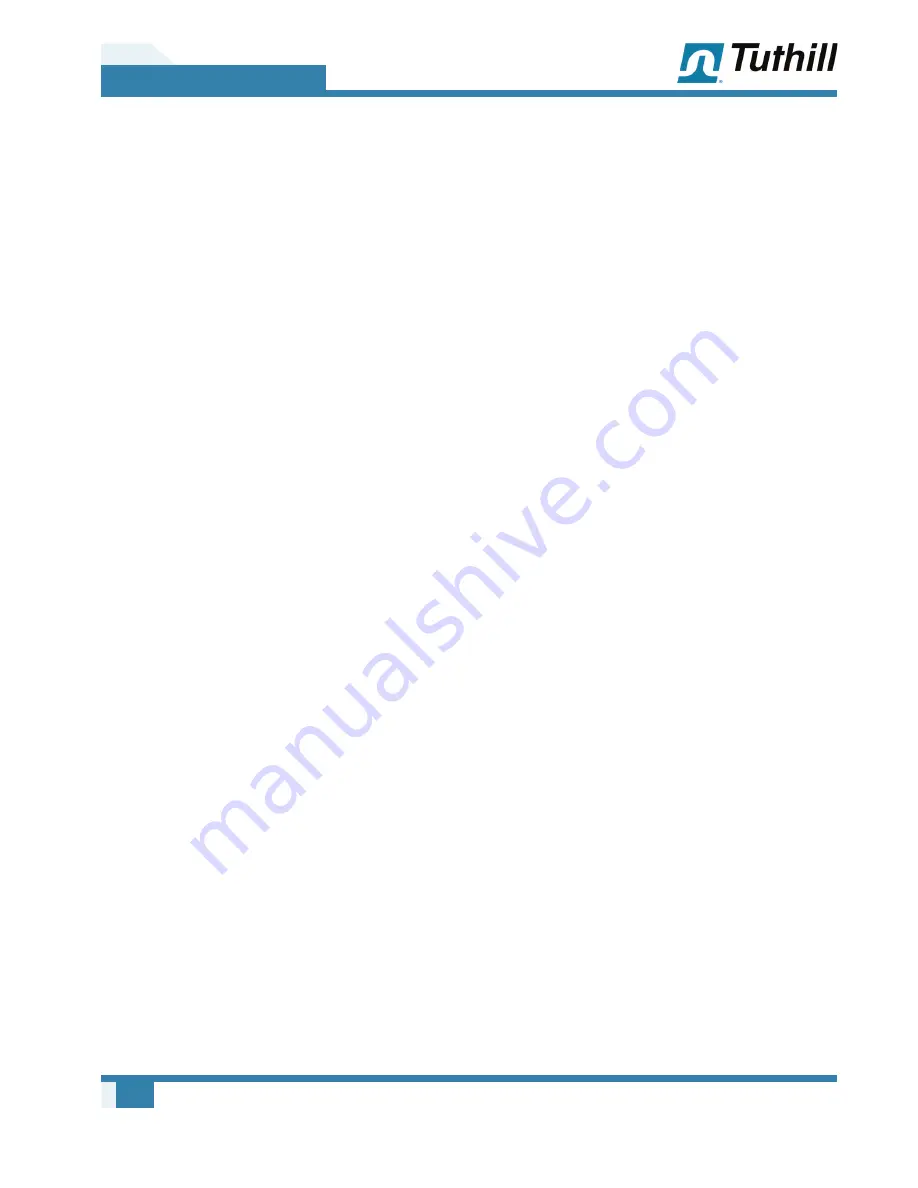
22
06
Troubleshooting
Manual 1807 Rev B p/n 001807 0000
discharge holes. Clean this from the valve
and check that the holes are not worn into the
valves.
4. Check the discharge valve block. It should not
be worn out of round in the holes or damaged
around the lower edge. Check for flatness with
a straightedge.
5. Check the discharge valve springs. They
should show no signs of weakening such as
unevenness or bulging of coils.
6. Check the guide rods. They should be smooth
and not worn in ridges, damaged, or worn in
any way that would allow the block to bind as it
slides up and down.
7. Check the valve seat in the cylinder. It should
be smooth and flush with the surrounding area.
8. Replace any worn components as required.
9. Replace the discharge valve, valve block,
discharge valve springs, and guide rods in the
same order and position in which they were
removed. Replace the cylinder cover and
secure it in place. Replace the oil drain plugs
(or close the drain valves) and fill the pump
with oil as described in
Filling the Pump with
Oil on page 10
. Test the pump as described
in
Checking Pump Performance on page
19
.
SHAFT SEAL
Although the shaft seal has a long, trouble-free life
under normal conditions, it may become worn or
scratched on the sealing faces by contaminated oil
and it may be damaged by inadequate lubrication.
To inspect the shaft seal:
1. Position the pump so that it rests on the closed
head to prevent oil from draining out of the
shaft seal housing.
2. Remove the belt guard and belts. Remove
the pump pulley and drive key from the pump
shaft.
3. Remove the shaft seal retaining ring from the
shaft.
4. Remove the rotating portion of the shaft seal
from the shaft. This may require a heavy pull,
especially if the unit has heat bonded to the
shaft. In extreme cases, it may be necessary to
remove the open head (or shaft seal housing)
to remove the seal.
5. If necessary, remove the seal seat from the
pump.
6. Check the mating seal faces on the stationary
and rotating segments of the seal assembly.
They should be smooth and shining with no
scratches or indentations.
7. Check the rubber friction ring. It should have
no scratches or grooves on the inside diameter
that seals to the shaft. It should be flexible –
not hardened.
8. Check the seal seat gasket. It should not be
cut, nicked, or hardened. Cracks or hardening
of rubber components indicate exposure to
excessive temperatures, and the seal should
be replaced.
9. If the components are defective or damaged,
replace the entire seal assembly.
10. Coat the seat gasket and seal seat with AX
Vacuum Oil and insert in position on the open
head and shaft seal housing. Use caution so
that the gasket does not roll or twist, since
creases or cuts cause a vacuum leak.
11. Coat the rotating portion of the shaft seal with
AX Vacuum Oil. Cover the keyway on the shaft
with a plastic tape or by forming a thin piece of
metal over the shaft. Coat the shaft and metal
cover with oil.
12. Carefully push the rotating portion of the shaft
seal (consisting of the seal face retainer shell,
friction ring, spring, and spring holder) over
the shaft by means of a pipe sleeve or a large
washer against the outer spring holder.
Note that the friction ring fits tightly on the shaft
to prevent slippage of the rotating portion of
the shaft seal. Be careful not to damage the
seal faces or cut the rubber. Check that the
seal face is not tilted. Remove the cover from
the shaft and install the retaining ring.
Summary of Contents for KINNEY KC Series
Page 6: ...iv Table of Contents Manual 1807 Rev B p n 001807 0000 ...
Page 17: ...11 Manual 1807 Rev B p n 001807 0000 04 OPERATION Figure 4 1 Pump Components ...
Page 22: ...16 05 Maintenance Manual 1807 Rev B p n 001807 0000 Figure 5 1 Oil Return Line ...
Page 34: ...28 08 Reassembly Manual 1807 Rev B p n 001807 0000 ...
Page 44: ......
Page 45: ......