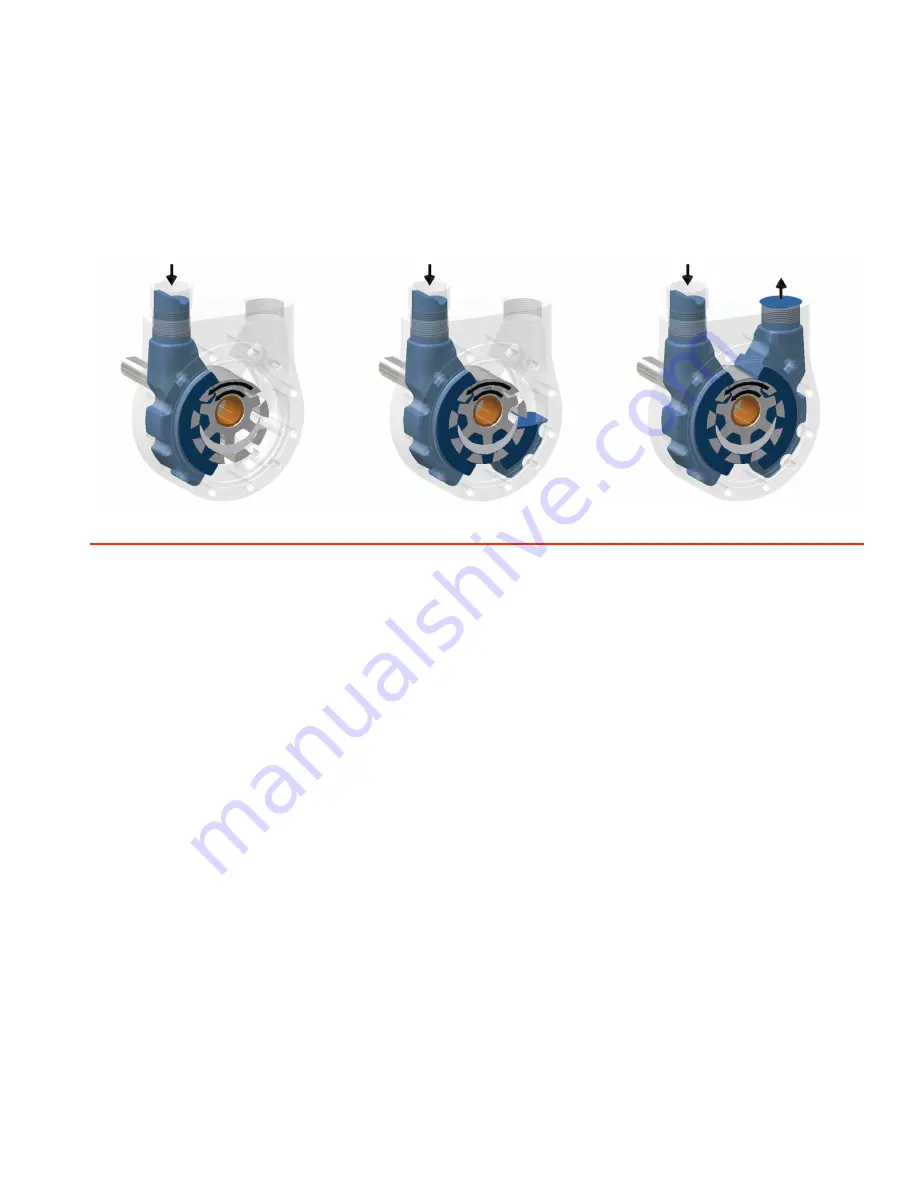
Page 4 of 18
The Pumping Principle
Tuthill 4000 Series cast iron pumps employ the internal gear pumping principle. There are only two moving parts. Pumping action is
based on a rotor, idler gear, and crescentshaped partition cast integral with the cover. Power applied to the rotor is transmitted to the
idler gear with which it meshes. The space between the outside diameter of the idler and the inside diameter of the rotor is sealed by
the crescent. As the pump starts, the teeth come out of mesh, increasing the volume. This creates partial vacuum, drawing the liquid
into the pump through the suction port. The liquid fills the spaces between the teeth of the idler and the rotor and is carried past the
crescent partition through the pressure side of the pump. When the teeth mesh on the pressure side, the liquid is forced from the
spaces and out through the discharge port.
WARNING
Failure to follow these instructions could result in serious bodily injury or death. These pumps should not be used for handling plain
water, corrosive or abrasive liquids or liquids not possessing adequate lubricity. Do not attempt to work on any Tuthill pump installation
before completing the steps below. Disconnect the drive so that it cannot be started while work is being performed. Review the Material
Safety Data Sheet (MSDS) applicable to the liquid being pumped to determine its characteristics and the precautions necessary to
ensure safe handling. Vent all pressure within the pump through the suction or discharge lines. All Tuthill pumps contain residual 200
SSU lube oil from the factory production test. Determine if this is compatible with the fluid you are pumping. If the fluid is incompatible,
consult the factory. If the pump is to be operated at elevated temperatures, the pump should be brought up to operating temperatures
gradually. Rapid or sudden introduction of liquids at elevated temperatures into the cold liquid chamber of the pump could cause
damage to pump externals, seals or other internal parts. Do not run the pump dry. Failure to comply with this could cause severe
damage to the internal seal, bushings and/or metal parts. Pump needs to be Earthed separately to avoid build up of Electro-Static
Charge.
Tuthill 4000 Series pumps are required to develop 25” mercury vacuum at 0 psi on factory test. While these pumps will develop as
high as 27” of vacuum, it is a sound engineering practice to avoid extreme vacuum whenever possible. Select a pipe size to reduce line
friction loss to a minimum.
The pump should be located as close to the source of supply as conditions permit and if possible, below the level of the liquid in the
reservoir. When necessary to locate the pump in a pit, provisions should be made to safeguard against flooding. Care must be taken to
properly support the suction and discharge piping so that no strain is put on the pump due to either weight or expansion. Piping strain
can result in misalignment, hot bearings, worn couplings, and vibration. It is important that the piping used be clean and free of chips
and scales.