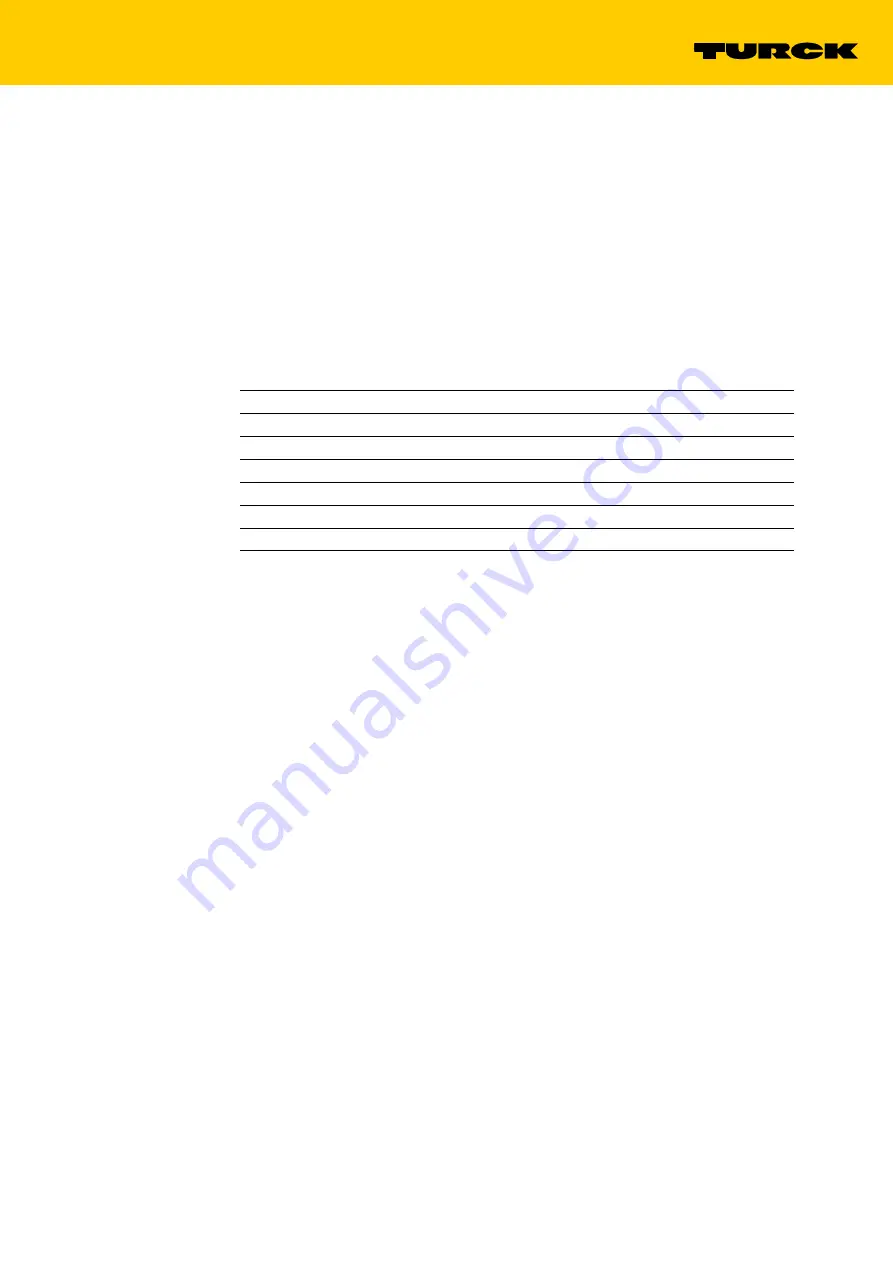
15
V01.0 | 2019/04
6
Safety Operating Instructions
6.1
General
➤
➤
The device must be registered online:
www.turck.com/SIL
or with the supplied SIL registrati-
on card. This must be filled in with all required information upon receipt and sent to Turck.
➤
➤
The device must only be carried out, fitted, installed, operated, commissioned and main-
tained by trained and qualified personnel.
➤
➤
The device is not specified for a certain application. Make sure that application-specific as-
pects are considered.
➤
➤
Data from other documents, e.g. data sheets, is not valid for functional safety operation.
Devices must be used in cabinets in an typical industrial field environment only. The follow-
ing restrictions describe the operation and storage conditions:
➤
➤
Ensure that the environment complies with the following ratings
Minimum ambient temperature
-25 °C
Maximum ambient temperature
70 °C
Minimum storage temperature
-40 °C
Maximum storage temperature
80 °C
Maximum air humidity
95 %
Minimum air pressure
80 kPa
Maximum air pressure
110 kPa
➤
➤
The average temperature over a long period of time directly on the exterior sidewall of the
housing must be maximum 40 °C.
ū
The temperature on the exterior sidewall of the housing can deviate considerably from the
temperature in the control cabinet.
ū
The temperature on the exterior sidewall of the housing must be observed in a steady state.
ū
In case the temperature on the exterior sidewall of the housing is higher, the failure rates
from
„5.3 FMEDA results“ on page 13
For a higher average temperature of 60 °C on the exterior sidewall of the housing, the failu-
re rates are multiplied by an experience factor of 2.5.
➤
➤
Ensure that sufficient heat dissipation is provided.
➤
➤
Protect the device from radiated heat and severe temperature fluctuations.
➤
➤
Protect the device from dust, dirt, moisture, shock, vibration, chemical stress, increased
radiation and other environmental influences.
➤
➤
Ensure a degree of protection of at least IP20 according to IEC 60529 at the mounting
location.
➤
➤
Ensure that the electromagnetic stress does not increase the requirements of
IEC 61326-3.1.
➤
➤
If there is a visible error, e.g. defective housing the device must not be used.
➤
➤
During operation of the device, surface temperatures may occur that could lead to burns if
touched.
➤
➤
The device must not be repaired. If problems occur with regard to functional safety, Turck
must be notified immediately and the device must be returned immediately to:
Hans Turck GmbH & Co. KG
Witzlebenstraße 7
45472 Mülheim an der Ruhr
Germany