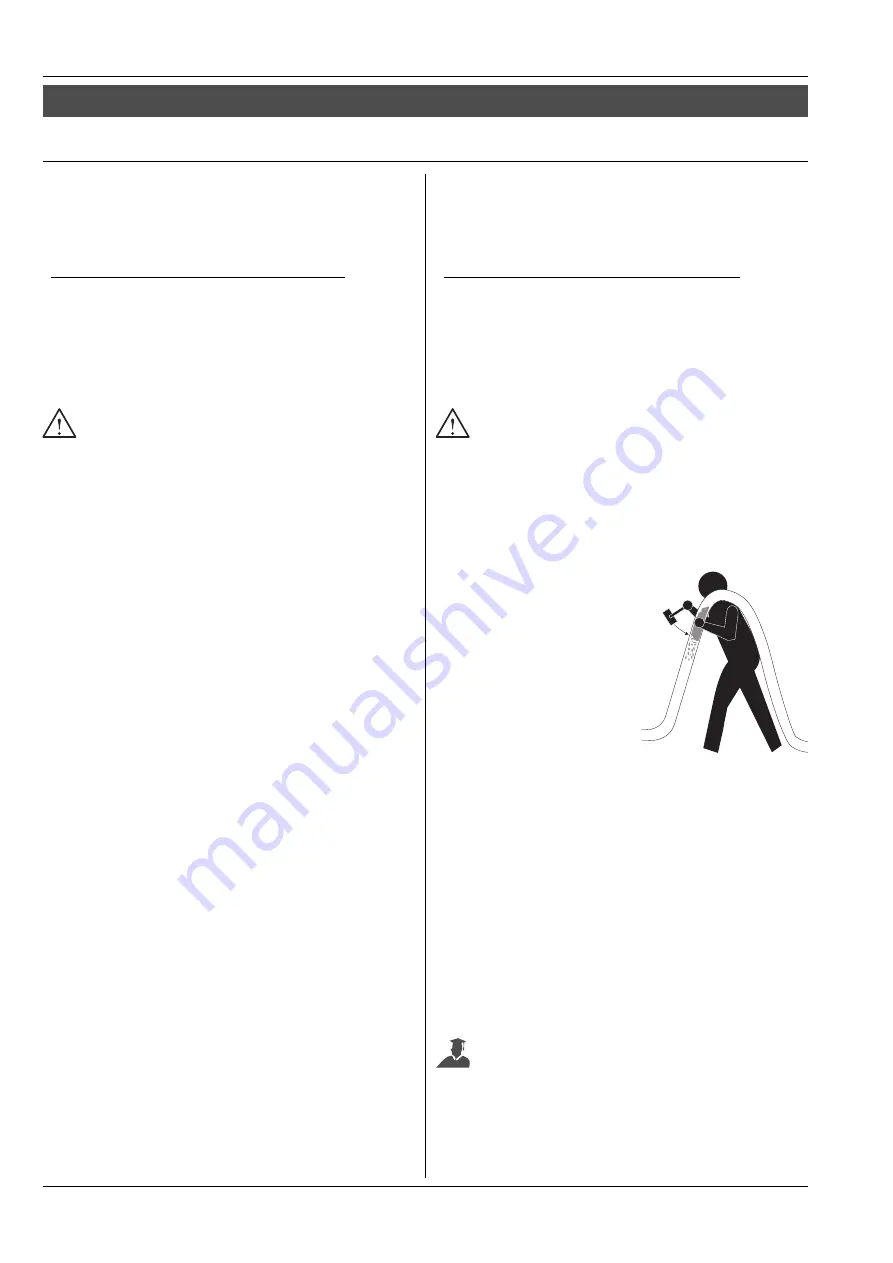
20
6 - PROBLEMS – CAUSES – REMEDIES
6.1 - MORTAR IS NOT FLOWING OUT OF THE SPRAY GUN
The spray gun is blocked
A hardened crust of material, a pebble or a deflector
whose orifice is too small for the material being used may
cause a clogging-up in the spray gun:
•
THE
MATERIAL
DOES
NOT
FLOW
OUT
OF
THE
SPRAY
-
GUN
In this case:
• Stop the machine by using the main switch.
• Release pressure in the delivery material hoses by turning
the pump reverse for a few seconds.
Release always pressure in the hoses by turning
the pump reverse for a few seconds (5-10) before
disconnecting them.
• Disassemble the deflector and, if necessary, the spray
gun so as to remove the cause for clogging.
• Before mounting the deflector and spray gun once again,
be certain that the nozzle is free (and, if necessary, clean
it with a piece of wire).
If the mortar is dripping from the spray gun during work,
try to replace the deflector and/or nozzle with one having
a smaller hole
• Start the machine once again and check that the material
flows out normally of the hoses.
Worn out stator
A worn out stator can prevent the material from flowing
out of the gun and may even cause blockage due to
overheated material at the beginning of the hose.
It is necessary to replace the stator and remove the
clogging in case.
Lack of material in the hopper
If, during the work, mortar is flowing in a non-continuous
way, check, at first , that there is material in the hopper.
Mortar hose blocked
A faulty mix or an overly prolonged pause may cause a
clogging up of the material delivery hose:
• material is not flowing out from the spray-gun.
In this case:
•
Stop the machine by using the main switch.
•
Release pressure in the delivery material hoses by turning
the pump reverse for a few seconds.
Release always pressure in the hoses by turning
the pump reverse for a few seconds (5-10) before
disconnecting them.
Find out just where the mortar delivery line is blocked: the
hose will be hard and stiff at this point.
The worse points are near the couplings.
Disconnect the clogged hose,
hit it with a hammer at the
clogged point so as to break
up the “plug”, and let the
hardened mix flow out.
• Turn the machine on for several seconds, and make
certain that the hose has been freed of the “plug”:
the material will flow normally from the hose.
Pour some slurry into the hose before the point where the
blocking occurred (gun direction), connect the hose line
once again, and start over again.
Mortar hose bent
Same as for mortar hose blocking.
Find the bend and straighten the hose.
If the material inside the hopper is not pumpable,
empty the hopper by disconnecting the hose from
the pump and let the material flow out.
Remove, if necessary, the discharge cap of the hopper
and wash out all the material with a stream of water.
Prepare the right mix and start again.