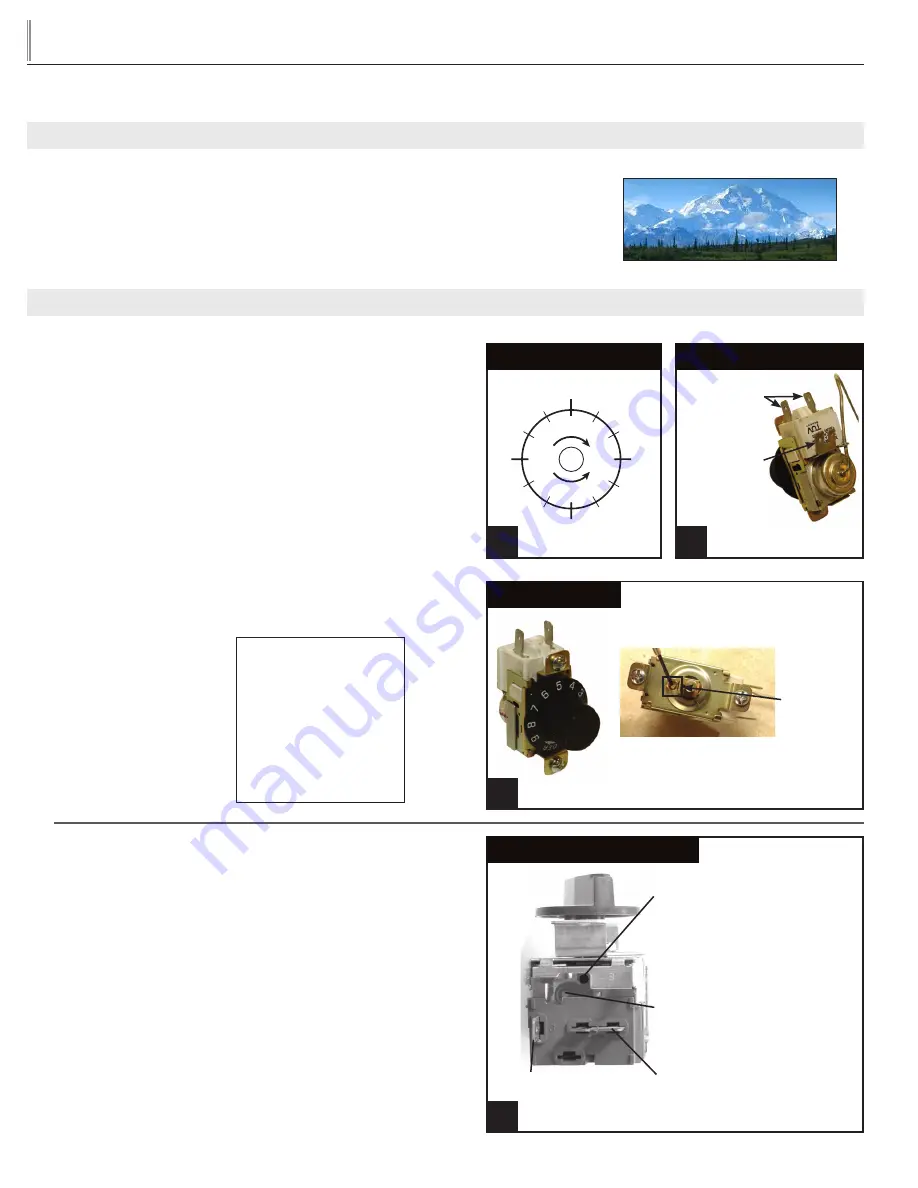
TRUE
SPEC SERIES®: STR, STA & STG, ROLL-IN AND ROLL-THROUGH
www
.
truemfg
.
com
11
1
INSTALLATION INSTRUCTIONS
DANFOSS TEMPERATURE CONTROL ADJUSTMENT
FOR HIGH ALTITUDE APPLICATIONS:
REQUIRED TOOLS:
• Allen Wrench (5/64")
• Torx Screw (T-7)
TERMS:
Cut-out
- Temperature sensed by the controller that shuts the
compressor off.
Cut-in
- Temperature sensed by the controller that turns the
compressor on.
WHEN TO MAKE AN ADJUSTMENT TO A MECHANICAL TEMPERATURE CONTROL
OPERATION INSTRUCTIONS:
REQUIRED TOOLS:
• Jewelers Screw Driver (Small Screw Driver)
GE CONTROL INSTRUCTIONS:
The scale to the right may be used as a guide for measuring
degrees of rotation required for altitude correction. See Figure 1.
The arrows indicate direction of screw rotation. Turn calibration
screw clockwise to obtain warmer operating temperatures.
NOTE:
Each 1/4 turn of the calibration screw is equal to
approximately 2 degrees F. Do not make more than 3/4 turn.
After making adjustment, measure temperature during three
cycles before adjusting again.
NOTE:
Only adjust the screw
(small flathead) on the face of
the control (next to the cam).
See Figure 3.
Follow the Altitude Correction
Table to the right.
WA
RMER
C OLDER
60
30
45
40
35
50
55
15
20
25
10
5
We advise to make a mechanical temperature control adjustment only for a high altitude location.
Compressor
Terminals
Ground
Terminal
To adjust the temperature control
take the control knob off to view the
cut-in screw. (See Photo Above)
Front of Temperature Control
Calibration
Screw
1
2
3
Cut-out Adjustment
Screw Allen (5/64" or 2 mm.)
Cut-in Adjustment
Screw Torx (T-7)
Compressor
Connection
ALTITUDE CORRECTION TABLE:
CALIBRATION SCREW ADJUSTS
BOTH CUT-IN AND CUT-OUT
Altitude (Feet)
2000
3000
4000
5000
6000
7000
8000
9000
10,000
Clockwise Turns
7/60
11/60
15/60
19/60
23/60
27/60
30/60
34/60
37/60
Compressor Connection
(double terminal)
HOW TO ADJUST A MECHANICAL TEMPERATURE CONTROL
Altitude Correction
Scale Guide for Measuring
Back of Temperature Control
Bottom of Temperature Control