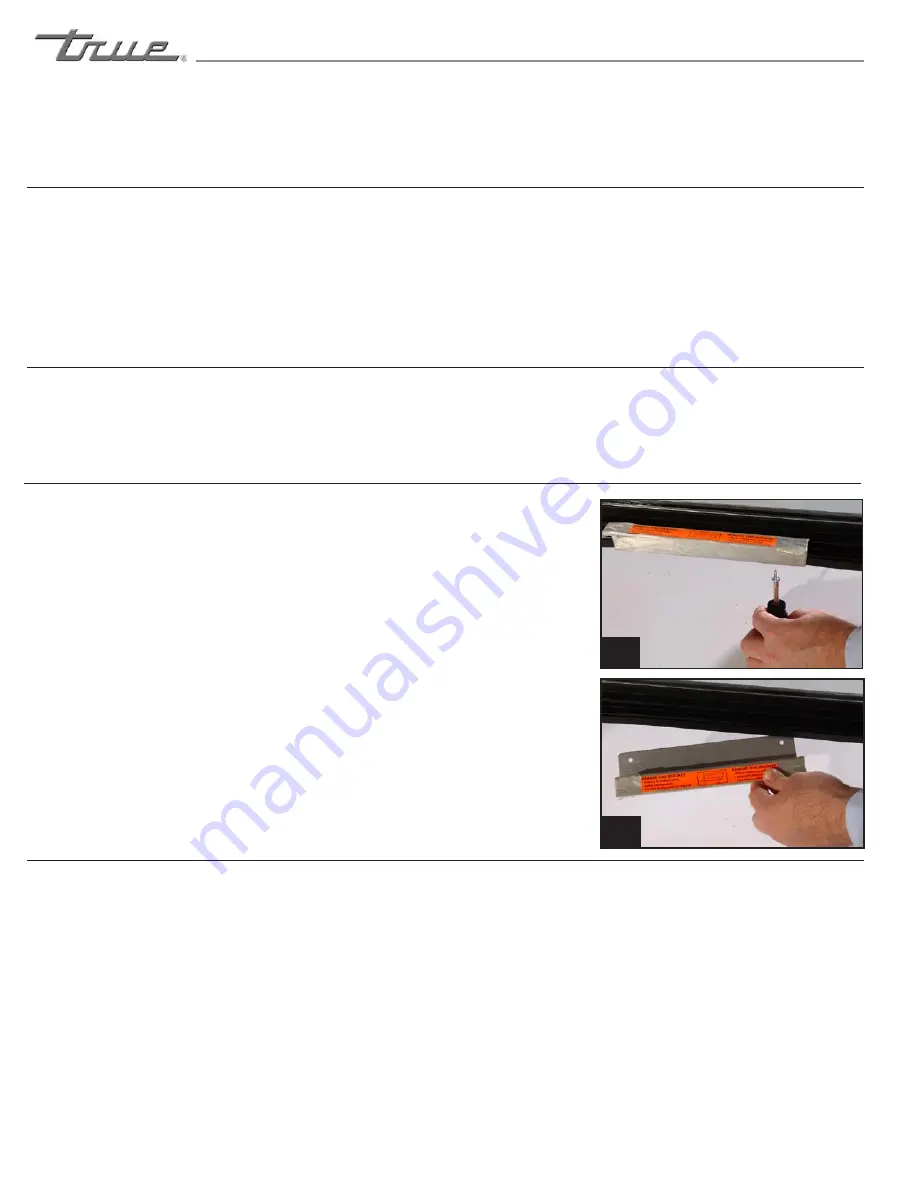
............ www.truemfg.com ............
True Food Service Equipment, Inc.
INSTALLATION / OPERATION INSTRUCTIONS
4
4
To ensure that your unit works properly from the first
day, it must be installed properly. We highly recommend
a trained refrigeration mechanic and electrician install
your TRUE equipment. The cost
of a professional installation is money well spent.
Before you start to install your TRUE unit, carefully
inspect it for freight damage. If damage is discovered,
immediately file a claim with the delivery freight carrier.
TRUE
is not responsible for damage incurred during shipment.
OWNERSHIP
• Adjustable Wrench
• Phillips Head Screwdriver
• Level
REQUIRED TOOLS
The following procedure is recommended for uncrating
the unit:
A.
Remove the outer packaging, (cardboard and bubbles
or styrofoam corners and clear plastic). Inspect for
concealed damage. Again, immediately file a claim
with the freight carrier if there is damage.
B.
Move your unit as close to the final location as
possible before removing the wooden skid.
C.
Remove door bracket on swinging glass door models
(see image 1-2).
NOTE
Keys for coolers with door locks are located in warranty
packets.
UNCRATING
INSTALLATION / OPERATION INSTRUCTIONS
1
2
REMOTE UNITS (This section applies to remotes only!)
• Remote cabinets must be ordered as remote.
We do not recommend converting for a
standard self contained to remote system.
• All remote cabinets must be hard wired.
• No castors available.
• All remote cabinets come standard using 404A
refrigerant.
• All remote units come standard with expansion
valve, liquid line solenoid, heated condensate
pan, and defrost timer when applicable.
• Contact TRUE Technical Service for BTU
requirements.
• No wiring necessary between cabinet
and condensing unit.
• All remote condensing units purchased
from TRUE are 208/230 volts single phase.
If you have any questions regarding this section,
please call TRUE at 1-(800)-325-6152.