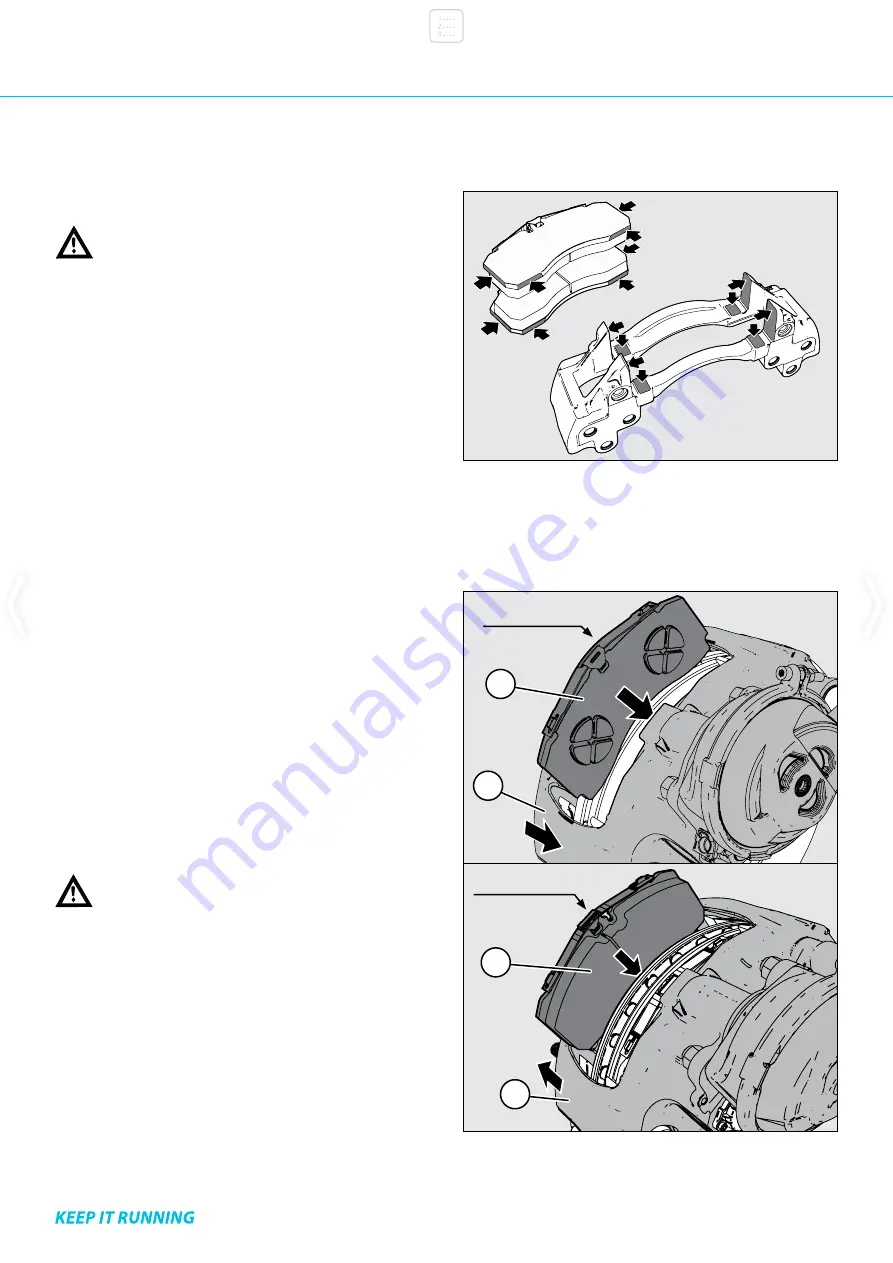
29
6
» Pneumatic Disc Brake SL7 - SM7
BRAKE PAD REPLACEMENT
6.2.4 - Insert brake pads
6.2 Fitting of Brake Pads
Pads must be changed as an axle set and NOT
individually. Use only pads which are permitted by the
vehicle manufacturer, axle manufacturer and disc brake
manufacturer. Failure to comply with this will invalidate
any Knorr-Bremse warranty.
Inboard brake pad
6.2.2 Check the carrier (2) and rubber seals for damage,
replace if necessary.
Important!
Brake Pad contact surface must be clean, devoid
of moisture and free from any dirt and debris.
6.2.3 Depending on the application, it may be necessary
for the abutments of the carrier and guiding surfaces of the
brake pad to be lightly coated with lubricant (K125122N50)
(see Fig.).
Important!
Do not use copper based lubricant.
Important!
Do not get any lubricant on the pad and/or disc
face or guide sleeve parts.
Refer also to specifications provided by the vehicle, axle and
brake system manufacturer.
Before inserting the brake pads, fully wind back the
tappet and boot assemblies (13) by rotating the shear
adapter (61) in an anti-clockwise direction (see Section
5.2).
6.2.4 Insert brake pads (12) as shown (see fig.).
Note:
With type SL7 and SM7 the inboard brake pad (12
1
) and
outboard brake pad (12
2
) are different, make sure they are
installed in their correct position.
6.2.3 - Areas to apply suitable lubricant
6.2.1 Depending on the intensity of contamination, clean
the brake pad bay area. Use suitable tools (wire brush, caliper
file, blunt scraper).
Important!
Take care not damage the Carrier and/or Rubber
Bush/Guide Sleeve seals.
Outboard brake pad
1
12
2
12
1
1