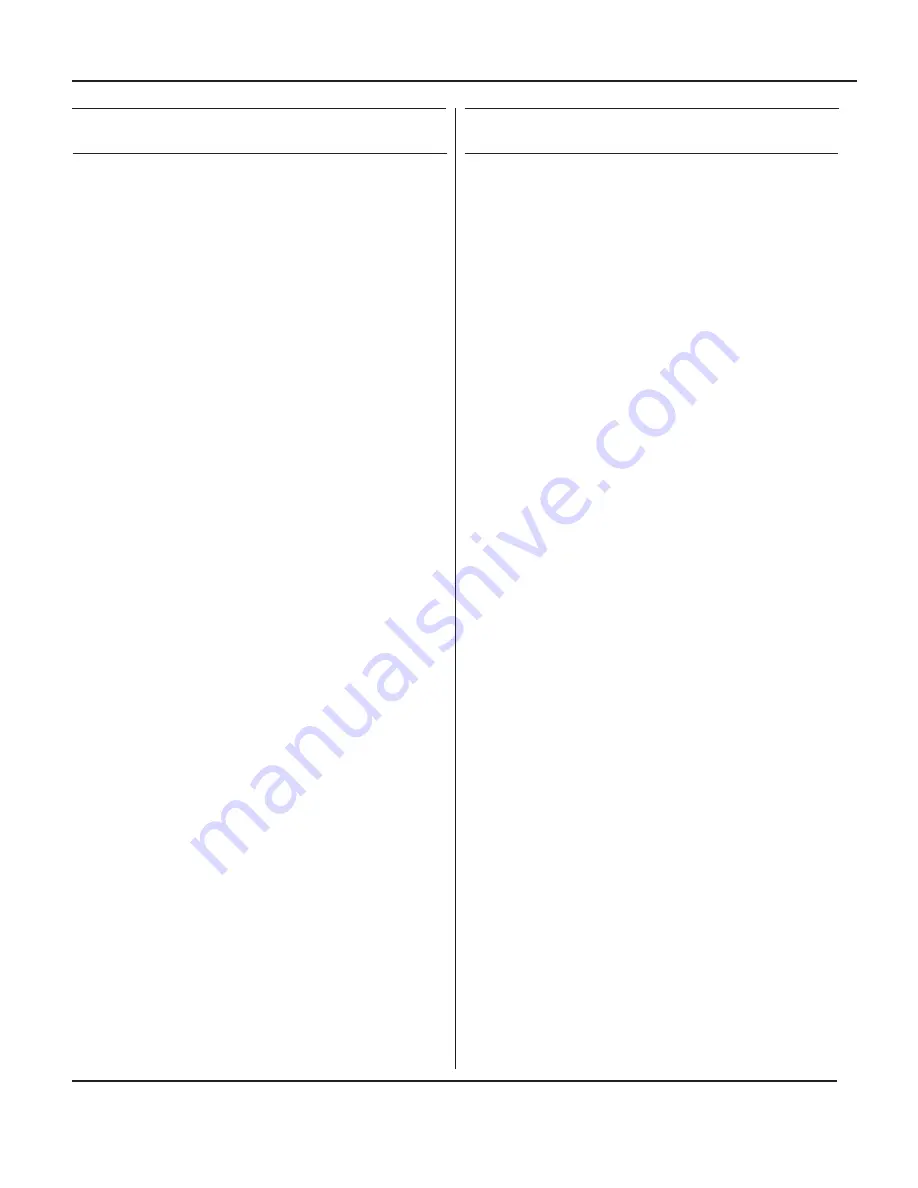
REF
PART
No.
No.
DESCRIPTION
QTY.
REF
PART
No.
No.
DESCRIPTION
QTY.
TRANSMISSION COVER & SHIFT LEVER
BRACKET ASSEMBLIES
1
1186299
Bolt–hex hd., #10-32 x 3/8",
self-locking flange .....................
3
2
GW-9463
Knob–tines/PTO clutch lever,
tapered, plastic ..........................
1
3
GW-2124
Detent Plate–tines/PTO clutch lever
1
4
777I20945
Decal–operating instructions,
detent plate................................
1
5
1186349
Bolt–flanged hex hd.,
3/8-16 x 1-1/2" ..........................
4
7
1186329
Bolt–flanged hex hd.,
5/16-18 x 3/4", Grade 5 ............
1
9
736-0275
Washer–flat, 5/16", S.A.E. .............
1
10
GW-2149
Bracket–shift levers.......................
1
11
GW-9362
Pin–spring, 1/8" ............................
1
12
GW-9838
Nut–castle (slotted), 1/2"-20, call
Tech Service for tightening
instructions. ............................
1
13
GW-9934
Washer–shoulder, 1/2" .................
1
14
GW-9932
Washer–disc spring ......................
2
15
GW-2178
Lever–wheel speed shift................
1
16
GW-2523
Cover–power unit transmission ....
1
17
GW-1123
Gasket–transmission cover...........
1
18
710-0376
Bolt–hex hd., 5/16-18 x 1", Grade 5,
(
remove with care
) ...................
1
19
712-0267
Nut–hex, 5/16"-18 .........................
1
20
1901439
Spring–neutral plunger (
remove
with care
)..................................
1
21
GW-1035-1
Plunger–neutral (
remove with care
) 1
22
1901440
Clip Ring–retains neutral plunger..
1
23
1186393
Nut–hex, flange locknut, 3/8"-16 ...
1
24
1902004
Bolt–hex hd., 3/8-16x1-1/2",
threaded full length....................
1
TINES/PTO CLUTCH LEVER ASSEMBLY
25
786-04002
Lever–eccentric, tines/PTO clutch.
1
26
741-04008
Bolt–hex hd., 1/4-20 x 1/2" ...........
1
27
GW-2123
Bushing–tines/PTO clutch lever
eccentric shaft ...........................
1
28
GW-9516
Retaining Ring–(snap ring),
external......................................
2
29
GW-2461
Eccentric–shaft, tines/PTO clutch
lever...........................................
1
30
GW-9911
Lockwasher–hi-collar, 1/4"............
1
31
GW-9672
Screw–socket hd., 1/4-20 x 3/8" ...
1
DRIVE SHAFT ASSEMBLY
33
716-0101
Retaining Ring–external ................
1
34
1909139
Dog Clutch–power unit .................
1
35
GW-9301
Key–3/16 sq. x 1" ..........................
3
36
1100004
Bolt–hex hd., 5/16-24 x 3/4", self-
locking flange, Grade 5 ..............
1
37
GW-9944
Washer–disc spring (concave)......
1
38
GW-2107
Pulley–transmission drive, cast iron 1
39
GW-50027
Washer–flat, hardened shoulder
1-1/4".........................................
1
40
1186310
Bolt–hex hd., 1/4-20 x 3/4", front
bearing cap................................
3
42
718-04007
Cap–front bearing .........................
1
43
1983632
Seal–oil, front bearing cap ............
1
44
GW-1124-2
Gasket–front bearing cap ..............
1
45
GW-1224-1
Shim–front bearing cap, .
010" thick ..............................As Req'd
45
GW-1224-2
Shim–as above, .030"...............As Req'd
45
GW-1224-3
Shim–as above, .005" ...............As Req'd
45
GW-1224-4
Shim–as above, .062" ...............As Req'd
46
GW-1714
Bearing & Race
(incl. one bearing GW-9400
and one cup (race) GW-9401) ...
2
47
GW-2655
Shaft–main drive, power unit ........
1
48
GW-9617
Seal–oil, drive shaft, rear ..............
1
49
GW-9517
Retaining Ring–(snap ring), internal........1
PINION SHAFT ASSEMBLY
50
715-0121
Pin–roll (spirol), 1/4 x 2" ...............
2
51
718-04006
Plug–retaining, pinion bearing ......
2
52
GW-9604
O-Ring–retaining plug...................
2
53
GW-1132-1
Shim–retaining plug, 1-1/64" inner
dia., .033" thick (on right side
only one GW-1132-1 shim is also
used between bearing and washer,
Ref. No.’s 54 & 55).................... As
Req'd
53
GW-1132-2
Shim–same as GW-1132-1, .062" .
As
Req’d
53
GW-1132-3
Shim–same as GW-1132-1, .010" As
Req'd
54
GW-9404
Bearing–ball, pinion shaft .............
2
55
GW-1126
Washer–pinion shaft .....................
2
56
GW-1222
Stem Pinion–slow speed gear &
shaft ..........................................
1
57
GW-9502
Ring–retaining, external ................
1
58
GW-2656
Worm Gear–bronze, wheel drive ...
1
59
GW-9300
Key–3/16" x 5/8"............................
1
60
GW-1233
Gear–fast speed pinion .................
1
(continued on page 55)
MODELS 682J &, E682L
Parts List
51
Summary of Contents for 21A-682J063
Page 50: ...POWER UNIT TRANSMISSION ASSEMBLIES See Page 50 16A Parts List MODELS 682J E682L 50 ...
Page 56: ...BOLO TINE ASSEMBLIES Parts List MODELS 682J E682L 56 ...
Page 58: ...Parts List MODEL E682L ELECTRIC START SYSTEM 58 ...
Page 61: ...Notes 61 ...
Page 62: ...Notes ...
Page 63: ...Notes ...