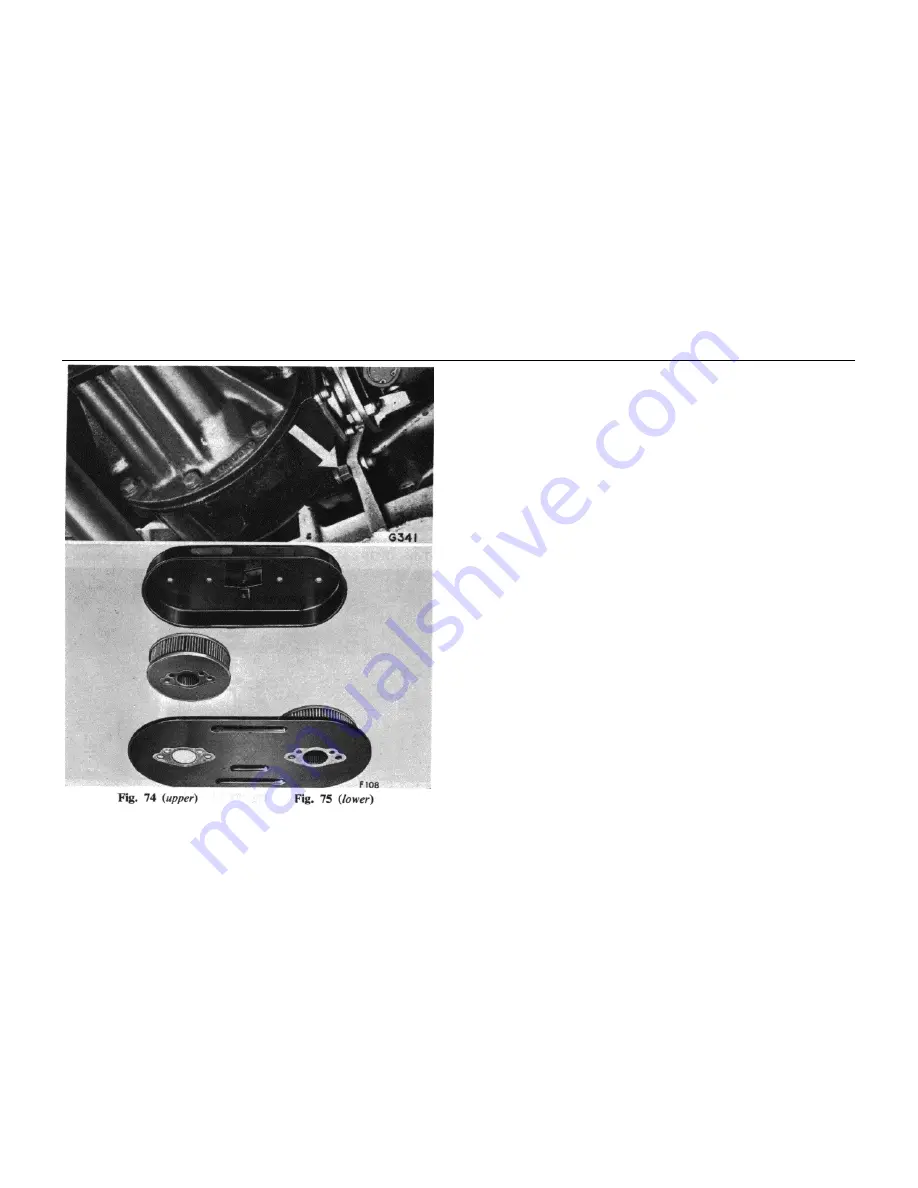
ROUTINE SERVICING
52
Top-up Rear Axle
(Fig. 74)
Remove the oil level plug (arrowed) and, using the same
dispenser as used for topping-up the gearbox, and the same oil,
i.e., extreme pressure (Hypoid) lubricant, top up the rear axle
until the oil is level with the bottom of the filler plug threads.
Allow surplus oil to drain away before refitting the level plug
and wiping clean.
Air Cleaners
(Fig. 75)
Remove and de-dust the paper elements.
Remove the bolts attaching the assembly to the carburettor
flanges, and detach the assembly.
Remove the centre bolt from the body, take off the cover plate
and lift out the element. Clean out the body and use a foot pump,
low pressure air line, or soft brush to remove foreign matter from
between the folds of the paper element.
Reverse the foregoing procedure to assemble the unit,
renewing the gaskets as necessary.
If the engine is operating in dusty conditions, clean the filters
more frequently.
Valve Rocker Clearances
(Fig. 95)
Check the valve rocker clearances and, if required, reset
them to 0.0l0 (0.25 mm.) (cold). See page 61.
Summary of Contents for Spitfire MK3
Page 1: ......
Page 2: ......
Page 3: ......
Page 7: ...CONTROLS INSTRUMENTS AND INDICATORS RIGHT HAND STEERING 6...
Page 8: ...CONTROLS INSTRUMENTS AND INDICATORS LEFT HAND STEERING 7...
Page 43: ...ELECTRICAL SYSTEM 42...
Page 45: ...ELECTRICAL SYSTEM 44...
Page 71: ...RECOMMENDED LUBRICANTS BRITISH ISLES ANTI FREEZE SOLUTIONS 70...
Page 72: ...RECOMMENDED LUBRICANTS OVERSEAS ANTI FREEZE SOLUTIONS 71...
Page 73: ...LUBRICATION CHART 72...