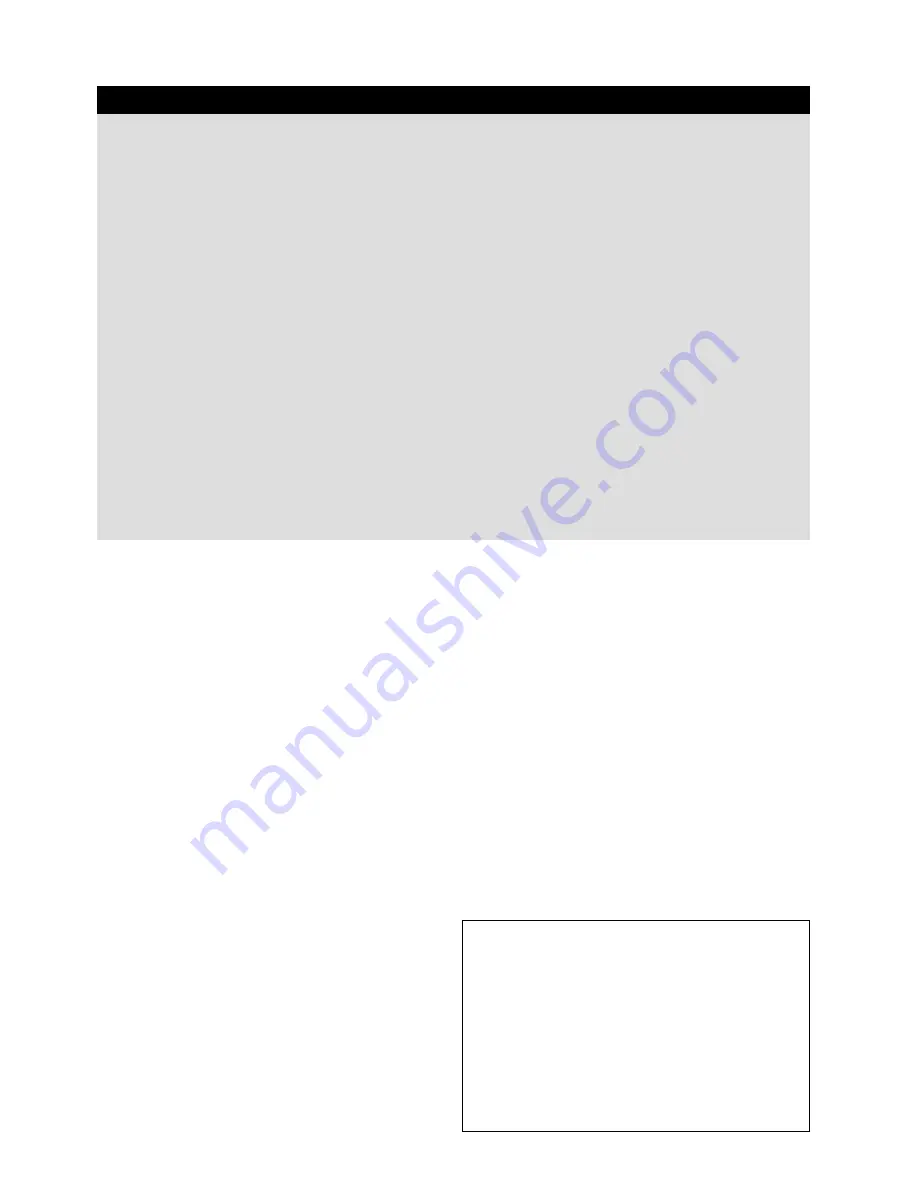
Service Policy
In the event of a complaint occurring, the following
procedure should be followed:
1
Telephone Customer Service on (024) 7637 2222
(08457 626591 in Scotland and in Northern Ireland),
having available the model number and power rating
of the product, together with the date of purchase.
2
Triton Customer Service will be able to confirm
whether the fault can be rectified by either the
provision of a replacement part or a site visit from a
qualified Triton service engineer.
3
If a service call is required it will be booked and the
date of call confirmed. In order to expedite your
request, please have your postcode available when
booking a service call.
4
It is essential that you or an appointed
representative (who must be a person of 18 years of
age or more) is present during the service engineer's
visit and receipt of purchase is shown.
5
A charge will be made in the event of an aborted
service call by you but not by us, or where a call
under the terms of guarantee has been booked and
the failure is not product related (i.e. scaling and
furring, incorrect water pressure, pressure relief
device operation, electrical installation faults).
6
If the product is no longer covered by the
guarantee, a charge will be made for the site visit and
for any parts supplied.
7
Service charges are based on the account being
settled when work is complete, the engineer will then
request payment for the invoice. If this is not made to
the service engineer or settled within 10 working
days, an administration charge will be added.
Replacement Parts Policy
Availability:
It is the policy of Triton to maintain
availability of parts for the current range of products
for supply after the guarantee has expired. Stocks of
spare parts will be maintained for the duration of the
product’s manufacture and for a period of five years
thereafter.
In the event of a spare part not being available a
substitute part will be supplied.
Payment:
The following payment methods can be
used to obtain spare parts:
1
By post, pre-payment of pro forma invoice by
cheque or money order.
2
By telephone, quoting credit card (MasterCard or
Visa) details.
3
By website order, www.tritonshowers.co.uk
Triton Plc, Shepperton Park, Caldwell Road,
Nuneaton, Warwickshire. CV11 4NR
T
R I T O N
S
T A N D A R D
G
U A R A N T E E
Customer Service
☎
(024) 7637 2222
Scottish and Northern Ireland
Customer Service
☎
08457 626591
Trade Installer Hotline
☎
(024) 7632 5491
Fax: (024) 7632 4564
www.tritonshowers.co.uk
E mail: [email protected]
Triton Plc guarantee this product against all
mechanical and electrical defects arising from faulty
workmanship or materials for a period of two years
for domestic use only, from the date of purchase,
provided that it has been installed by a competent
person in full accordance with the fitting
instructions.
Any part found to be defective during this guarantee
period we undertake to repair or replace at our
option without charge so long as it has been
properly maintained and operated in accordance
with the operating instructions, and has not been
subject to misuse or damage.
This product must not be taken apart, modified or
repaired except by a person authorised by Triton Plc.
This guarantee applies only to products installed
within the United Kingdom and does not apply to
products used commercially.
This guarantee does not affect your statutory rights.
What is not covered:
1
Breakdown due to:
a)
use other than domestic
use by you or your resident family;
b)
wilful act or
neglect;
c)
any malfunction resulting from the
incorrect use or quality of electricity, gas or water or
incorrect setting of controls;
d)
faulty installation.
2
Repair costs for damage caused by foreign objects
or substances.
3
Total loss of the product due to non-availability of
parts.
4
Compensation for loss of use of the product or
consequential loss of any kind.
5
Call out charges where no fault has been found
with the appliance.
6
The cost of repair or replacement of pressure
relief devices, sprayheads, hoses, riser rails and/or
wall brackets, isolating switches, electrical cable,
fuses and/or circuit breakers or any other accessories
installed at the same time.
7
The cost of routine maintenance, adjustments,
overhaul modifications or loss or damage arising
therefrom, including the cost of repairing damage,
breakdown, malfunction caused by corrosion,
furring, pipe scaling, lime scale, system debris or
frost.