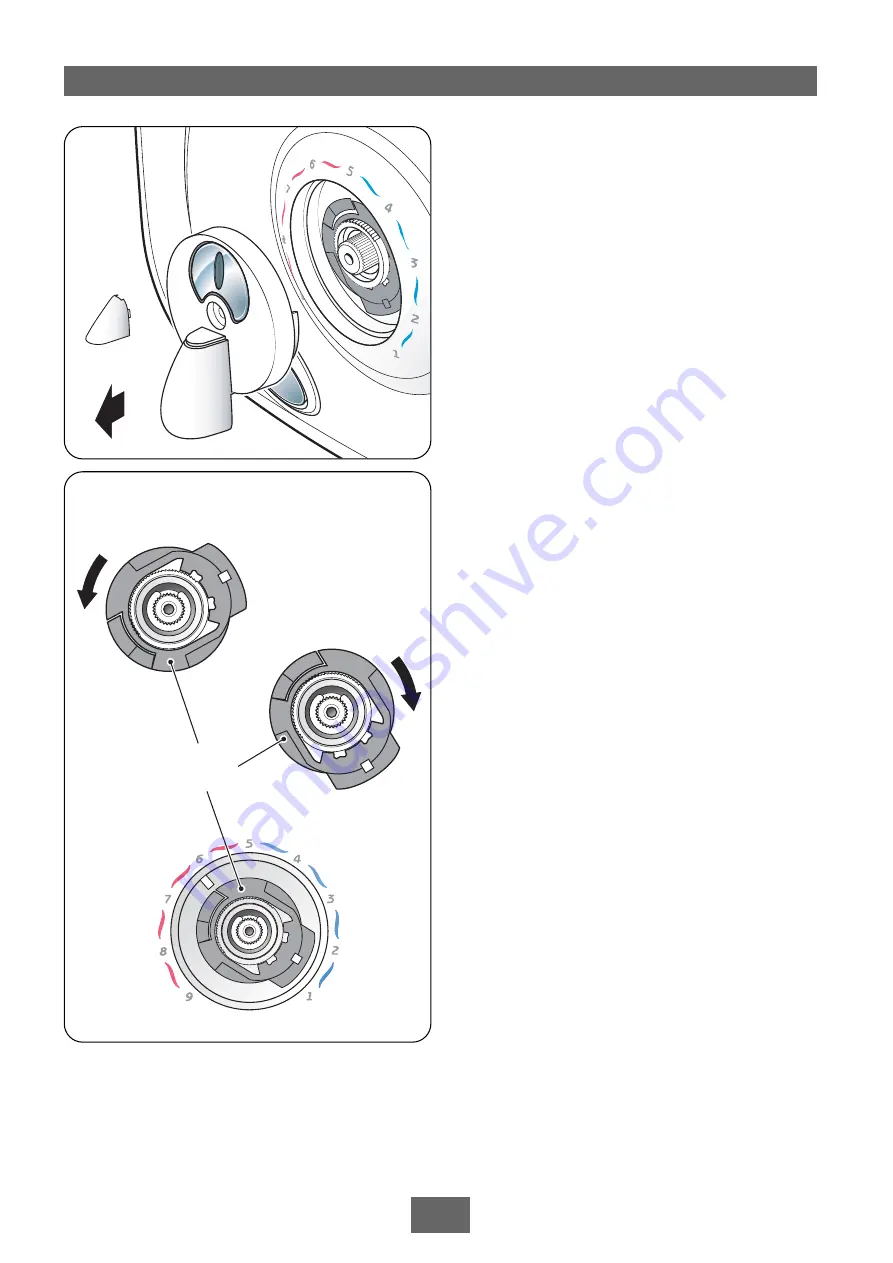
S p r a y h e a d
18
Fig.41
Maximum
temperature
stop
Increase stop position
Decrease stop position
Fig.42
Note:
As the flow control is adjusted it is quite
normal for the sound of the pump to alter in
pitch.
ADJUSTING THE MAXIMUM
TEMPERATURE STOP
As a safety feature the shower has a built-in
maximum temperature stop to prevent you
accidentally exceeding your highest desired
temperature. This is set in the factory to provide
a maximum temperature based on the hot and
cold water supplies being 65°C and 15°C
respectively.
Procedure
Rotate the temperature control to setting ’5’ on
the temperature scale.
Remove the cover trim to gain access to the
retaining screw. Unscrew the retaining screw
and pull off the temperature control
(fig.41).
Carefully pull off the maximum temperature
stop mechanism.
To increase the temperature stop setting,
reposition the mechanism anti-clockwise within
the arc of the grooves
(fig.42)
.
To decrease the temperature stop setting,
reposition the mechanism clockwise within the
arc of the grooves
(fig.42)
.
Replace the temperature control by push fitting
onto the spindle, making sure the pointer relates
to the ‘5’ on the temperature scale.
Refit the retaining screw and push the cover trim
into place.
IMPORTANT:
Only adjust the maximum
temperature stop when the hot water is at its
usual storage temperature.