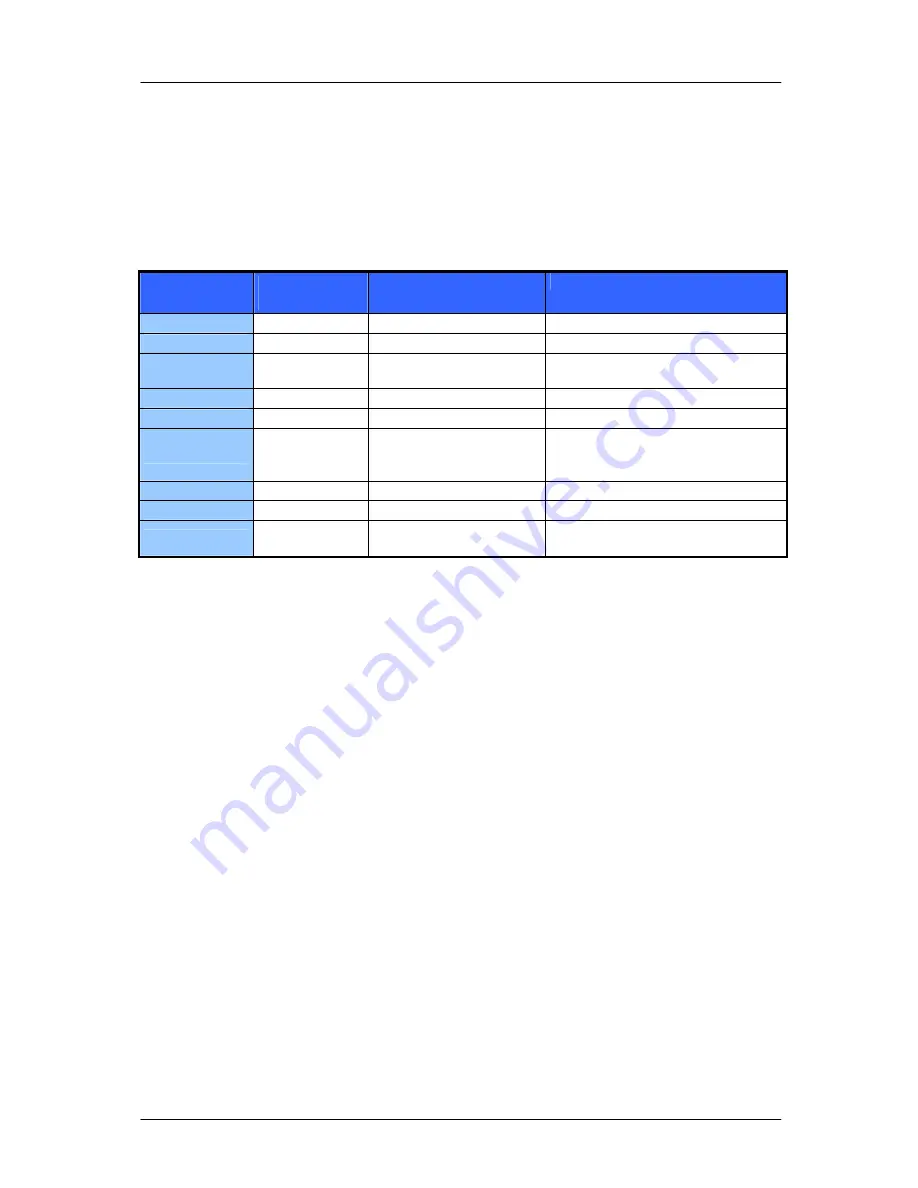
QSH4218 Manual (V1.03 /13-November-2007)
9
Copyright © 2007, TRINAMIC Motion Control GmbH & Co. KG
5.2 Motor
Current
Setting
Basically, the motor torque is proportional to the motor current, as long as the current stays at a
reasonable level. At the same time, the power consumption of the motor (and driver) is proportional
to the square of the motor current. Optimally, the motor should be chosen to bring the required
performance at the rated motor current. For a short time, the motor current may be raised above this
level in order to get increased torque, but care has to be taken in order not to exceed the maximum
coil temperature of 130°C respectively a continuous motor operation temperature of 90°C.
Percentage of
rated current
Percentage of
motor torque
Percentage of static
motor power dissipation
Comment
150%
≤
150%
225%
Limit operation to a few seconds
125%
125%
156%
Operation possible for a limited time
100%
100%
100%
= 2 * I
RMS_RATED
* R
COIL
Normal operation
85%
85% 72%
Normal operation
75%
75% 56%
Normal operation
50%
50% 25%
Reduced microstep exactness due to
torque reducing in the magnitude of
detent torque
38%
38% 14%
-“-
25%
25% 6%
-“-
0%
see detent
torque
0%
Motor might loose position if the
application’s friction is too low
Table 5.1: Motor current settings
Hints:
Q: How to choose the optimum current setting?
A1:
Generally, you choose the motor in order to give the desired performance at nominal current.
For short time operation, you might want to increase the motor current to get a higher torque than
specified for the motor. In a hot environment, you might want to work with a reduced motor
current in order to reduce motor self heating.
The Trinamic drivers allow setting the motor current for up to three conditions:
-
Stand still (choose a low current)
-
Nominal operation (nominal current)
-
High acceleration (if increased torque is required: You may choose a current above the nominal
setting, but be aware, that the mean power dissipation shall not exceed the motors nominal
rating)
A2:
If you reach the velocity limit, it might be a good idea to reduce the motor current, in order to
avoid resonances occurring. Please see the hints on choosing the driver voltage.
Q: What about energy saving – how to choose standby current?
A1:
Most applications do not need much torque during motor stand-still. You should always reduce
motor current during stand still. This reduces power dissipation and heat generation. Depending on
your application, you typically at least can half power dissipation. There are several aspects why
this is possible: In stand still, motor torque is higher than at any other velocity. Thus, you do not
need the full current even with a static load! Your application might need no torque at all, but you
might need to keep the exact microstep position: Try how low you can go in your application. If
the microstep position exactness does not matter for the time of stand still, you might even reduce
the motor current to zero, provided that there is no static load on the motor and enough friction in
order to avoid complete position loss.