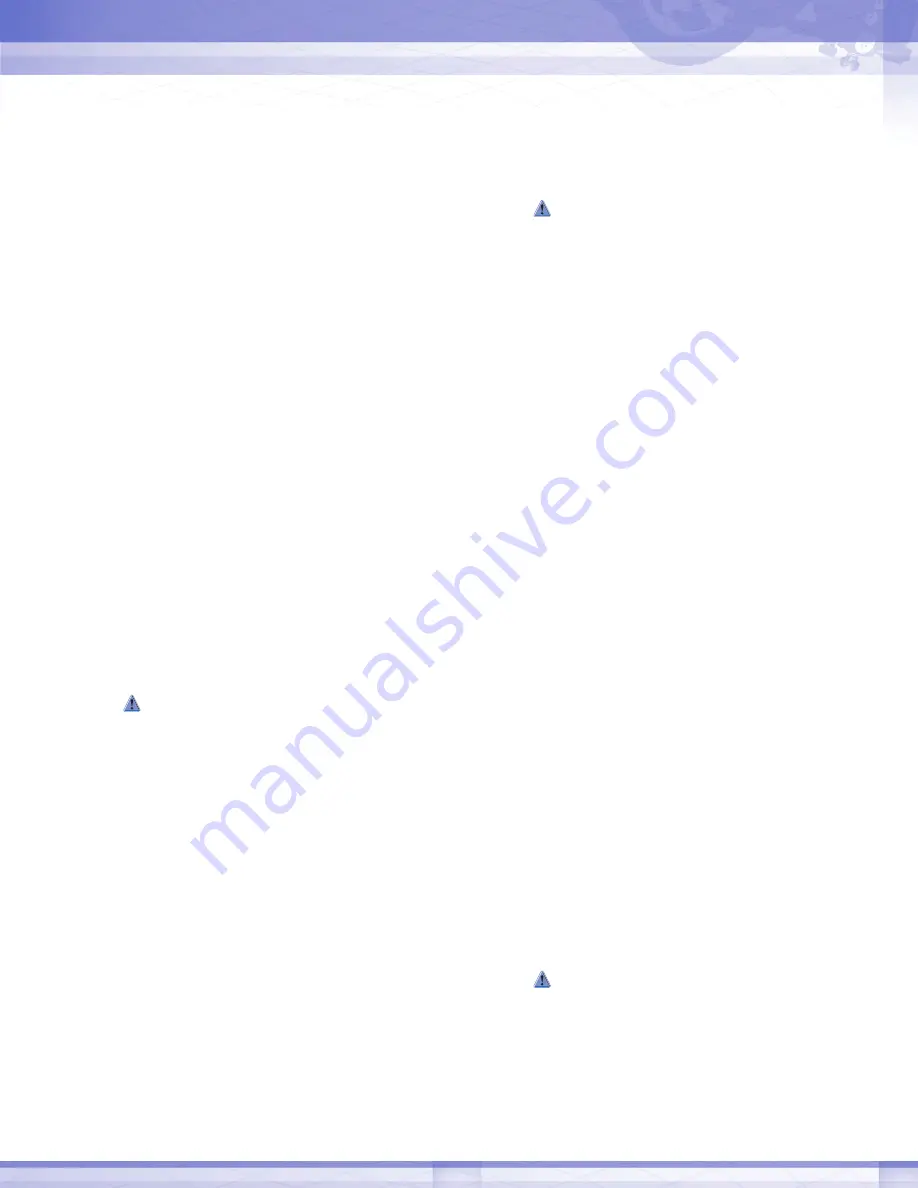
Product Instruction Manual
5
Body Disassembly
To disassemble the body, refer to Figures 1, 2
and 5 and proceed as follows:
1. On Optimux valves supplied with seat
retainer screws, remove the seat retainer
screws and retainer clips. Lift the seat
retainer out of the valve body. (Refer to
Figures 1A, B, C).
2. On valves supplied with retainer snap-ring
configuration, carefully insert a screwdriver
in the key slot provided in the retainer; pry
the retainer and snap ring out of the valve
body. (Refer to Figure 1D).
3. Remove the gland flange by removing both
packing nuts. It is not necessary to remove
the studs.
4. Drive the taper pins out of the disc by
tapping on the small end of the pins using a
punch and hammer.
5. Remove the end plug (optional bolted
flange and seal if applicable).
6. Remove shaft by inserting a press or a
nylon rod (or similar material) into body’s
blind end, and using a hammer, carefully
tap the shaft through the body.
CAUTION:
Take special care not
to damage the splined end of
the shaft during disassembly.
To prevent scratching the sealing surface of
the disc while removing the shaft, place
supports underneath the disc. This also
prevents the shaft from binding in the body
as the shaft comes off the bearing surfaces.
7. Push the packing and bearings out of the
body using a dowel of appropriate
diameter. Push the packing from the center
of the valve.
Body Reassembly
To reassemble the body subassembly, refer to
Figures 1, 2, 3, and 5 and proceed as follows:
1. Clean all parts.
2. Check the disc seating surface to make
sure it is smooth and free of scoring and
scratches.
CAUTION:
Damaged or dirty
seat surfaces can cause
excessive seat wear and high
torque requirements. Damaged
discs should be replaced.
3.
Inspect shaft for scratches or galled
surfaces. For maximum performance,
Optimux shafts are machined to a very
smooth finish. If damage exists, replace the
shaft or contact factory representative.
Note:
Disc and shaft are interchangeable in
recent designs. Replacing the disc does not
require replacing the shaft. Earlier designs
require that the disc and shaft be machined
together. Contact the factory for matched
disc and shaft.
4. Insert new sliding stem shaft bearings into
the body. (A press may be required with
some designs.)
Note:
Earlier Optimux designs require the
disc to be aligned in the body in such a way
that it can rotate properly. Align the shaft
bearings on either side of the disc and insert
the shaft through the body, bearings and
disc.
5. Position the disc in the body, making sure it
will rotate in the proper direction with
respect to the body’s internal disc stop.
Slide the shaft through the body, bearings
and disc.
CAUTION:
Exercise care while
sliding the shaft into the sliding
stem shaft bearings to avoid
damage to both the shaft and
bearings.