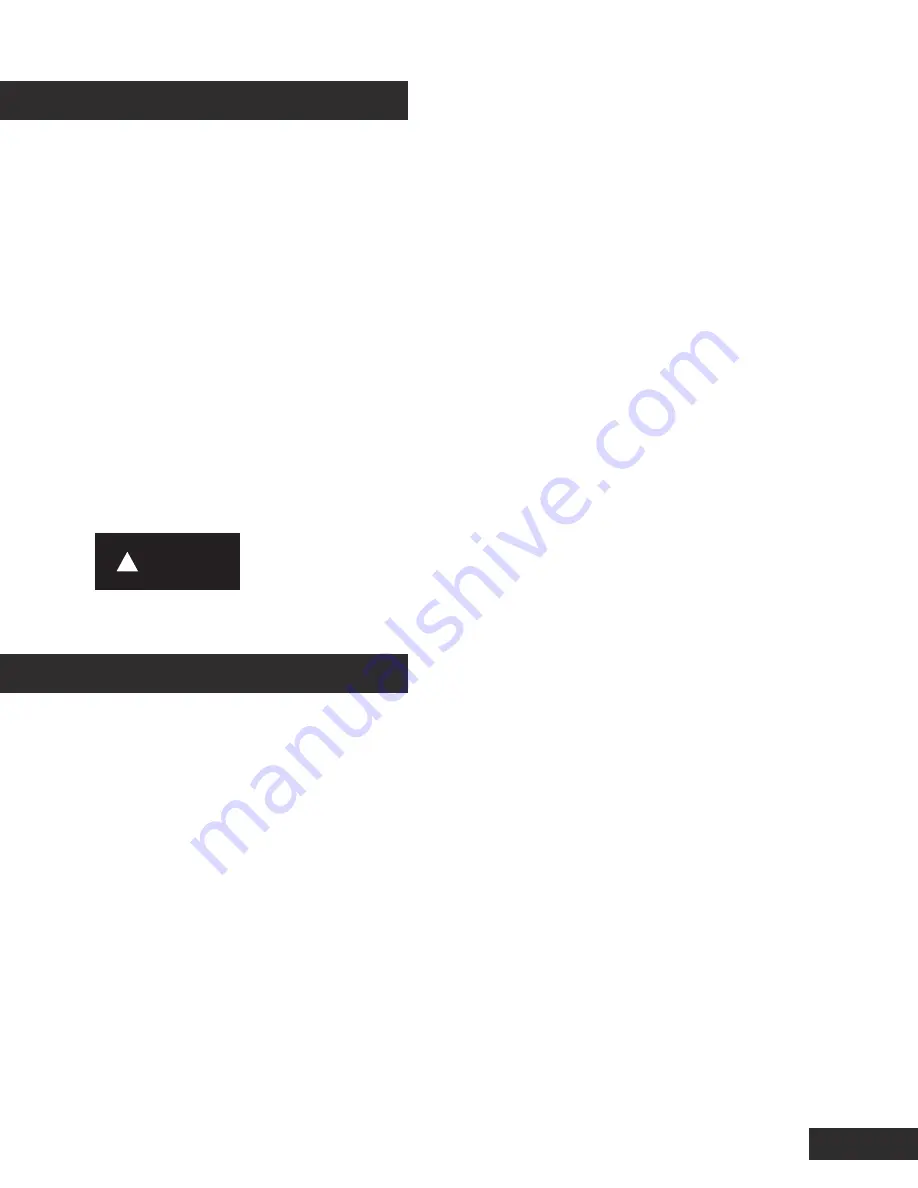
5
CLEARING A JAM
SHUT-DOWN PROCEDURE
Should a jam occur, the machine will automatically go in the reverse direction for
approximately two seconds, then after a brief pause the machine will automatically start
in the forward direction. This forward and reverse automatic process will occur three
times to clear the jam, if the machine remains jammed after the third cycle the machine
will automatically turn itself off.
1. Ensure that all personnel are clear of both the input chute and the cutter head.
2. Momentarily depress the yellow Reverse pushbutton. This will cause the cutters to
run backwards for as long as the Reverse pushbutton remains depressed.
3. Release the Reverse pushbutton. The machine will come to a stop. After the machine
has completely stopped, press the forward button and try to shred material.
4. If machine jams again, reverse shredder, Lock Out Power, and manually remove
offending material.
5. Re-start machine in the forward direction to resume operation.
1. Allow conveyors to clear all material before shut down if applicable.
2. Depress E-Stop pushbutton. Remove power cable from receptacle.
3. Clean any remaining debris from the machine and from the immediate area.
NEVER Hold the forward button in the depressed position, as damage
to the machine and the electrical system could occur.
!
WARNING
Summary of Contents for Shredmaster
Page 2: ......
Page 15: ...13 CONTROL PANEL LAYOUT CUTTER HEAD ASSEMBLY...
Page 18: ...16...
Page 19: ...17...
Page 20: ......