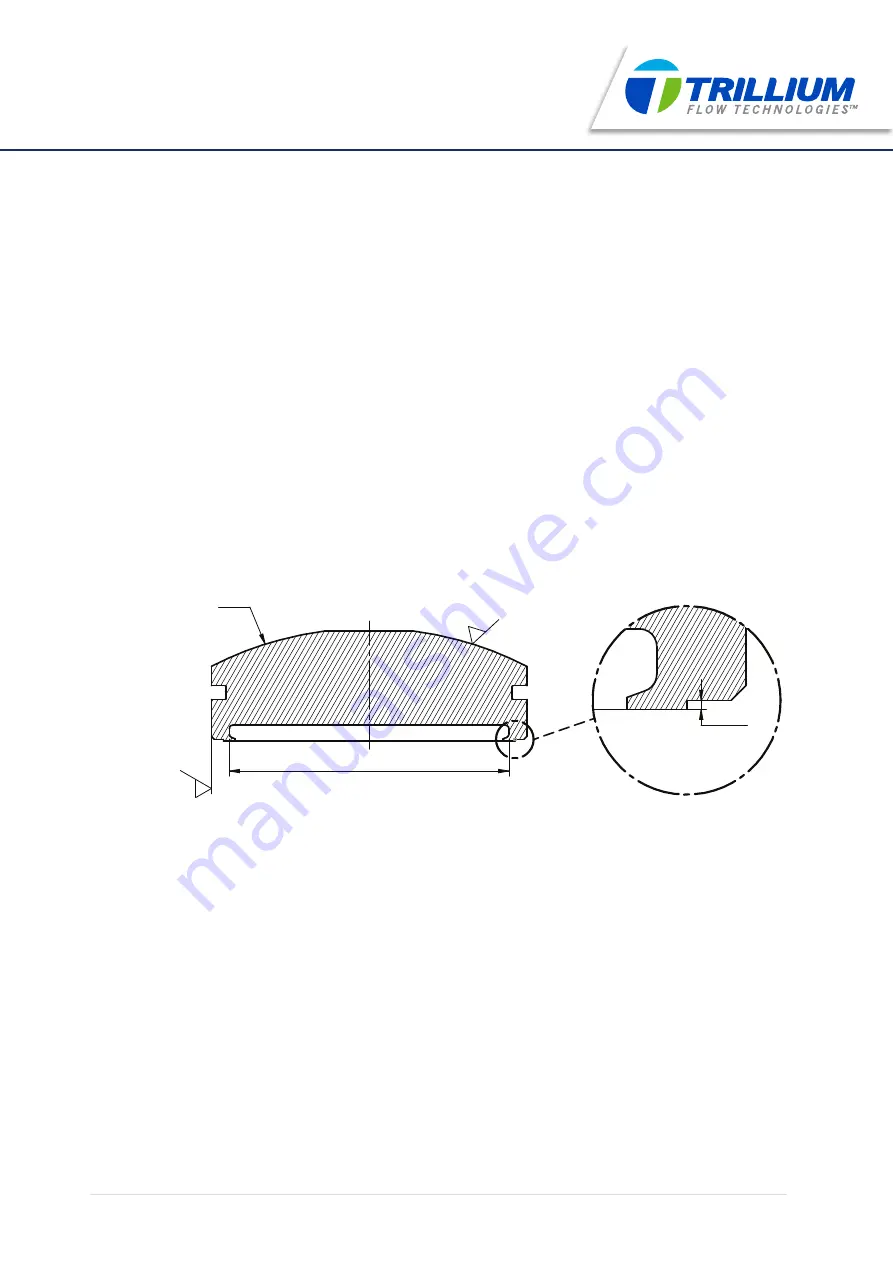
• Disc (11)
o General
•
Inspect the hinge surface (sphere) of the disc. If it is galled, scratched, corroded or pitted
the disc shall be replaced.
•
Inspect the disc seating surface (figure 13). Roughness of the seating surface of the
nozzle shall be Ra 0.4µm (16 RMS). Touch check the roughness of lapped seating
surfaces according to ISO 2632 (or equivalent) test specimen.
o Disc seat
•
Inspect the disc seat.
•
Any scratch or impact mark less than 0.5mm deep on the seating surface shall be
removed by lapping only according to 8.2.4.2. (Preffered operation).
•
The remachining of the nozzle seating surface is recommended if there is any impact
mark deeper than 0.5mm.
•
Lap the disc seat as deemed necessary
•
Final roughness of the seating surface of the disc shall be Ra 0.4µm (16 RMS or finer).
•
Planeity of the lapping machine shall have been checked.Inspect the nozzle seat. Any
scratch or impact mark less than 0.5mm deep on the seating surface shall be removed by
lapping. The remachining of the nozzle seating surface is recommended if there is any
impact mark deeper than 0.5mm.
Ra 0,8
R
a
1,
6
Disc seating
Sphere
x
The disc seat maximum repair (figure 15): X dimension must not go below 0.1 mm for all orifices. If the
repair dimension is out of the tolerance, the disc must be replaced.
• Nozzle (6)
o General
•
Inspect the nozzle wetted area. There shall be no trace of erosion, pitting.
•
Inspect the thread. There shall be no impact marks on it. Damaged can lead to seizing.
•
Inspect the centering diameter. It shall be free of any burrs to prevent seizing on
reassembly.
•
Inspect the nozzle base surface/groove.
If the surfaces are galled, scratched, the nozzle base surface shall be lapped according to the
flange finition chosen (written on GA drawing). RTJ groove may be reworked with very high
grade sandpaper (1200 mini) or lapping paste to Ra 0.4 to 1.6 (16-64 RMS).
If the surfaces are corroded or pitted, the nozzle shall be changed.
The nozzle seating surface inspection and rework are critical to ensure the tightness of the main
valve after reassembly.
o Nozzle seat
27
|
www.trilliumflow.com
STARFLOW V
™
PRESSURE RELIEF VALVE
SARASIN-RSBD
™