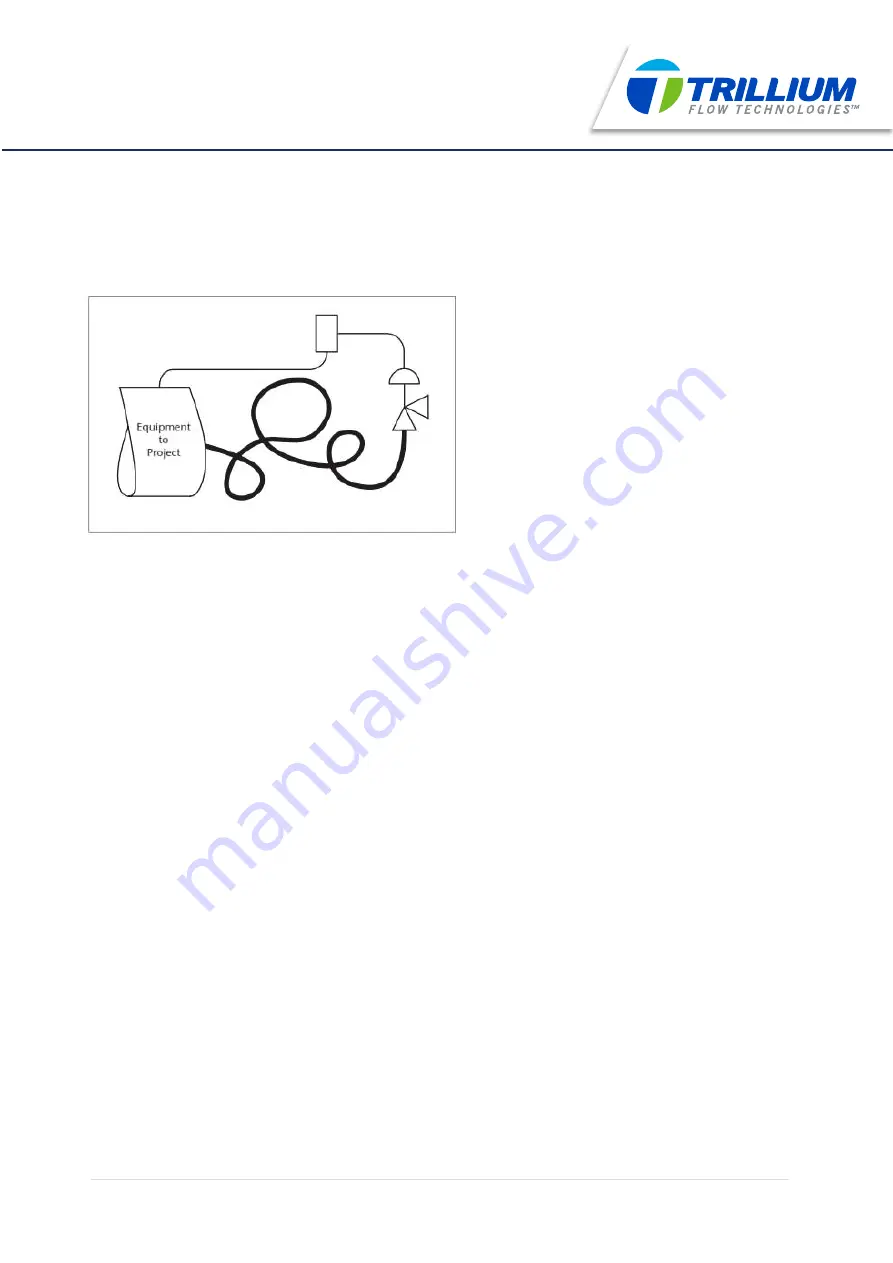
7.5 OPTIONS
7.5.1 REMOTE SENSE
• Safety valve will respond to actual system pressure conditions.
• Eliminates undesirable cycling due to excessive inlet pressure losses.
• Improves safety, under adverse operating conditions.
This optional feature permits the pilot to sense system pressure at a location that most accurately reflects the actual operating
pressure of the protected system.
A remote pressure sense connection eliminates the false system pressure indication that will occur during relieving conditions, due
to pressure losses in the inlet piping to the safety valve. Most applicable codes recommend that the inlet piping system be designed
for a maximum anticipated non-recoverable pressure loss of 3 percent. If this is not possible, the remote pressure sense connection
should be specified.
Please note that the addition of a remote pilot sense line allows the pilot to correctly sense system pressure and to keep the valve
from rapid cycling or chattering. With remote sensing the piston type, pilot operated safety valves described in this catalogue will
remain stable against the effects of high inlet pressure loss phenomena. However, relieving capacity will be proportionately reduced
whenever there is inlet pressure loss to the safety valve.
15
|
www.trilliumflow.com
78 SERIE SAFETY RELIEF VALVE
SARASIN-RSBD
™