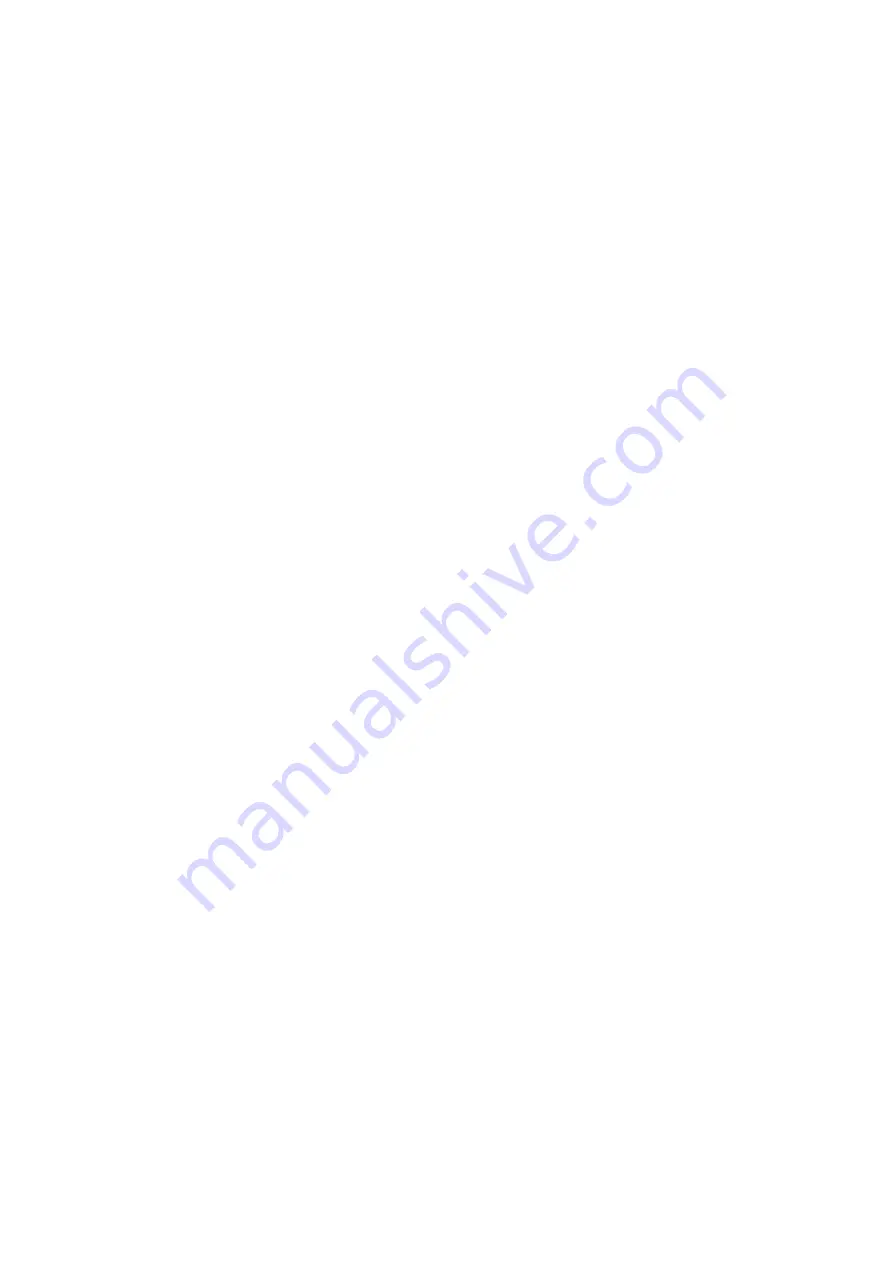
Generic TT31 Minor Modification
21 February 2008
SUP/TT31/001
Issue
1.6
______________________
Trig Avionics Limited
Page 8
4. Accomplishment Instructions
4.1 Equipment and tools required
You will need a Mode S transponder ramp test set, a pitot/static system test set, an inspection lamp or
torch, and a 3/8
th
inch Allen key. Depending on the accessibility of the mounting tray and rear
connector wiring, you may also need screwdrivers – including a long screwdriver – to inspect the
mounting brackets and connectors.
4.2 Preparation
During the installation you will need to program the unique Mode S airframe address into the
transponder. Allocation of Mode S addresses comes from the appropriate national authority of aircraft
registration; ensure that you have applied for and been issued with a Mode S address before you start.
4.3 Pre-test Existing Installation
This step is optional, but may assist in fault finding if a problem is found later in the process. Pre-
testing will not be possible if the reason you are replacing the Mode A/C transponder is because the
transponder itself is faulty.
The pre-test activities involve testing the existing installation and noting in particular:
•
Transponder receiver sensitivity – Minimum Triggering Level or MTL. The existing
transponder MTL should have an MTL between -71 dBm and -77 dBm. Sensitivity below
this range may indicate a problem with the antenna or antenna cable, although could also be
an indication of a fault in the existing transponder.
•
Transponder transmitted power. The existing transponder should provide not less than 125
Watts (Class 1) or 70 Watts (Class 2) at the antenna. Power levels below this may also
indicate a problem with the antenna or antenna cable, although could also be an indication of
a fault in the existing transponder.
•
Altitude reporting. Test the altitude reporting system, ideally over the service ceiling of the
aircraft. A problem with the altitude reporting may indicate a fault in the altitude encoder or
wiring between the encoder and the transponder tray, although could also be an indication of a
fault in the existing transponder.
If a fault is identified in the pre-testing, you will need to trace the fault cause. If the fault is in the
transponder to be replaced, then the upgrade process described here would clear the fault. If the fault
is in the existing installation however, upgrading the transponder will not fix it.
4.4 Process
4.4.1
Verify Circuit Breaker Status
Trace and identify the existing transponder circuit breaker. Verify that the circuit breaker is in
satisfactory condition and is of the correct type and rating. The circuit breaker for the TT31 should
rated between 3 Amps and 5 Amps.
4.4.2
Verify Antenna Status
Trace and identify the existing transponder antenna. The transponder antenna will be a small stub or
blade antenna on the bottom of the aircraft. Note that on an aircraft with DME the antenna for the
DME will look similar to the transponder antenna; ensure you are looking at the right one. Check the