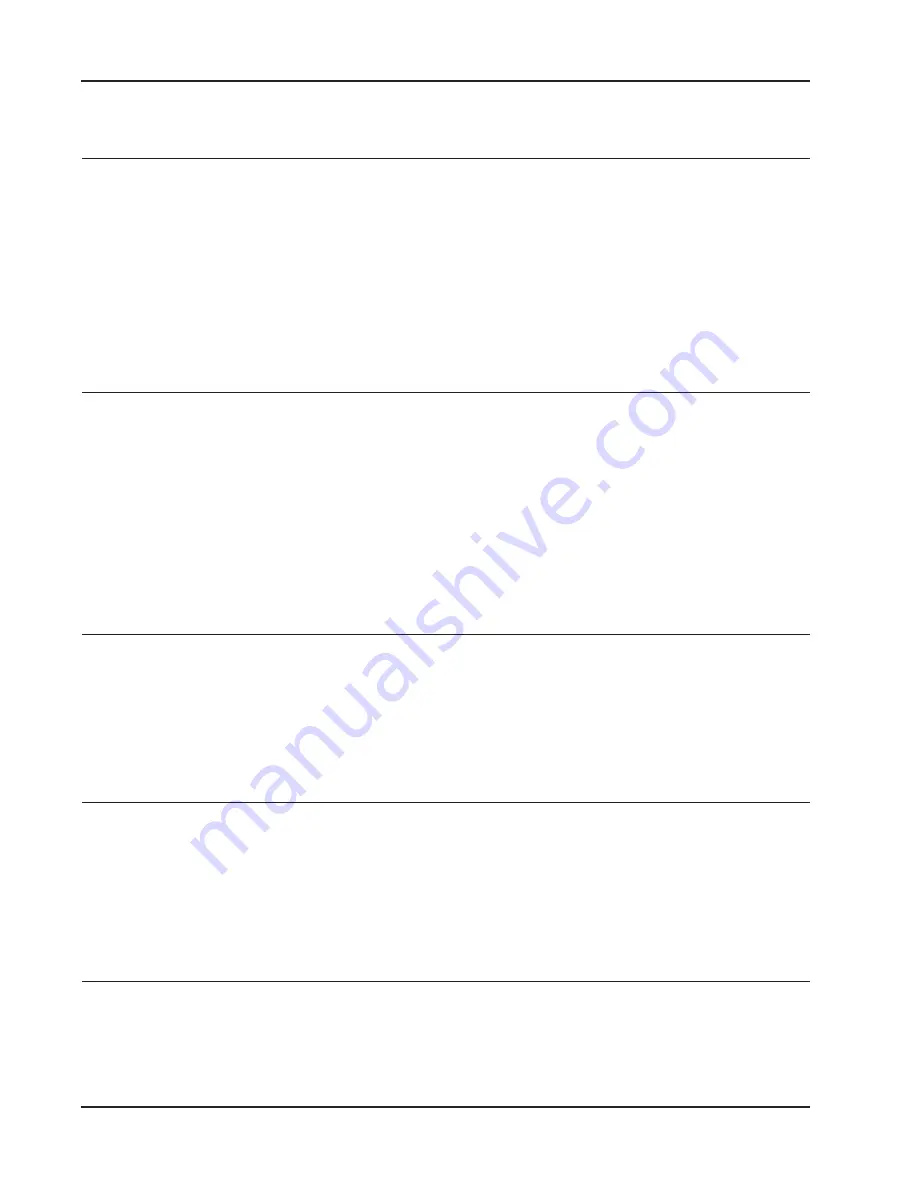
TRI TOOL INC.
92-0547 Rev. 210906
26
10. TROUBLESHOOTING
Problem: Tool Bit Chatters
The tool bit is loose or overextended.
The tool bit is damaged.
The tool holder is too loose in the slides.
The cutting speed is too fast.
The clamping pads are loose on the pipe or tube.
Cutting fluid is required.
The main bearing pre-load is loose.
Problem: Excessive Tool Bit Wear
The pipe or tube material is too hard or abrasive.
The cutting speed is too fast.
Cutting fluid is required.
A dull Tool Bit is causing surface hardening conditions (Stainless pipe or
tubing).
There is scale or other foreign matter on the pipe or tube, which is dulling
the tool bit at the start of the cut.
The tool bit is incorrect for the material being cut.
Problem: Rough Surface Finish
The tool bit is dull, chipped, etc.
Metal build-up on the cutting edge of the tool bit is creating a false cutting
edge.
Cutting fluid is required.
The cutting speed is incorrect.
Problem: Tool Holder is not Feeding
The feed pin is broken or out of position.
The feed sprocket shear pin is broken.
The feed screw is stripped.
The feed nut is stripped.
The slide rails are too tight.