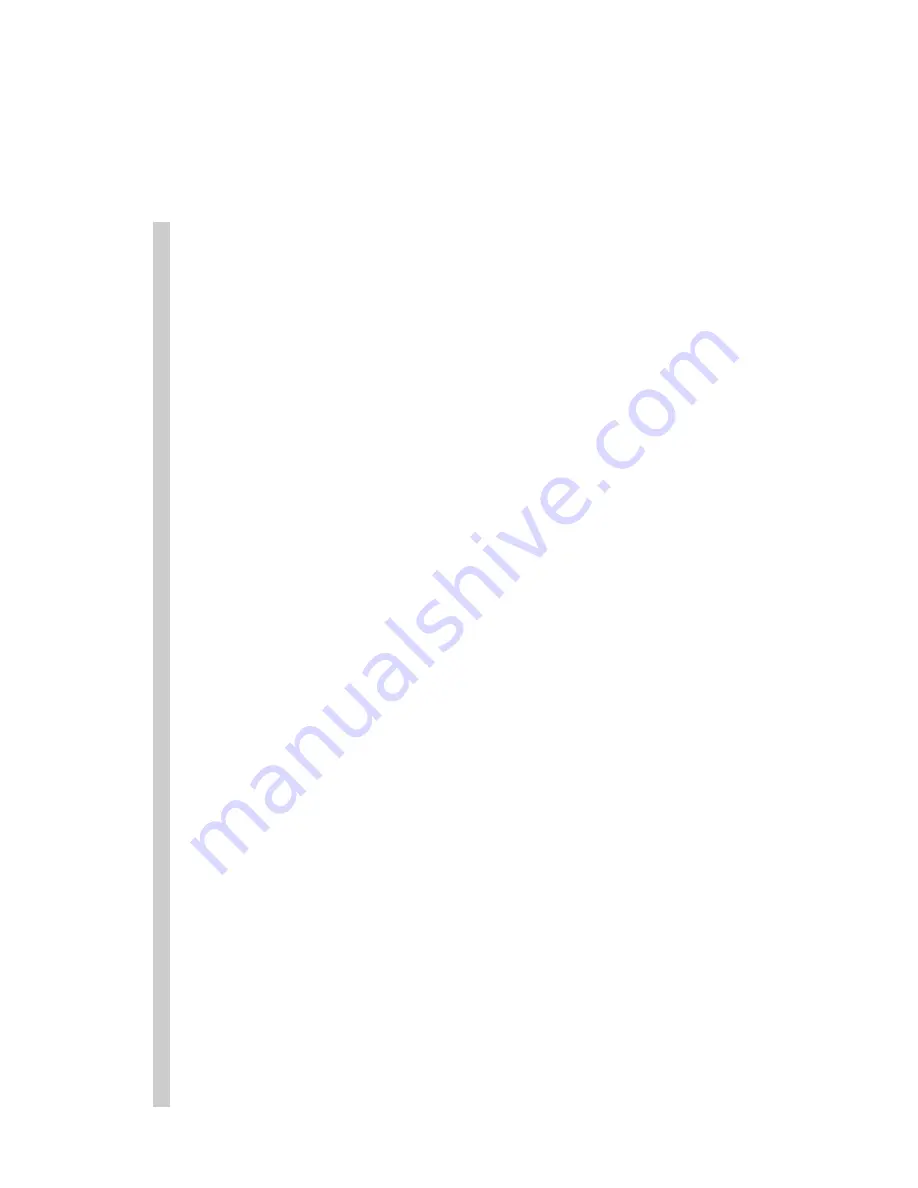
- 25 -
SP114
SP216
SP218
SP328
SP441
0
Key No.
Description
Part Number
Part Number
Part Number
Part Number
Part Num
1
Casing (Tri-Clamp) Sanitary
S114M-01C-316
S216M-01C-316
S218M-01D-316
S328M-01C-316
SP4410M-01
1
Casing (Bevel Seat) Sanitary
S114T-01C-316
S216T-01C-316
S218T-01D-316
S328T-01C-316
SP4410T-01
1
Casing (N.P.T.) Glass Beaded
S114S-01C-316
S216S-01C-316
S218S-01D-316
S328S-01C-316
SP4410S-01
1
Casing (Tri-Clamp) Glass Beaded
S114MI-01C-316
S216MI-01C-316
S218MI-01D-316
S328MI-01C-316
SP4410MI-0
1
1
Casing (Bevel Seat) Glass Beaded
S114TI-01C-316
S216TI-01C-316
S218TI-01D-316
S328TI-01C-316
SP4410TI-01
1
Casing (Flanged) Glass Beaded
S114F-01D-316
S216F-01D-316
S218F-01E-316
S328F-01D-316
SP4410F-01
2
Impeller (see note below)
S114-02C-316
S216-02C-316
S218-02C-316
S328-02C-316
SP5410-02
A
6
Shaft
SP114D-06E-316
SP216D-06E-316
SP328D-06E-316
SP328D-06E-316
SP5410D-0
6
6B
Shaft (Threaded)
SP114F-06E-316
SP216F-06E-316
SP328F-06E-316
SP328F-06E-316
SP5410F-0
6
11A
Backplate (Packing Seal)
SP114A-11A-316
SP216A-11A-316
SP328A-11A-316
SP328A-11A-316
SP5410A-11
11B
Backplate (Packing Water Seal)
Not Available
SP216B-11A-316
SP328B-11A-316
SP328B-11A-316
SP5410B-11
11D
Backplate (External Seal)
SP114D-11-316
SP216D-11-316
SP328D-11-316
SP328D-11-316
SP5410D-1
1
11F
Backplate Pin (External Seal)
216D-11-1-S
216D-11-1-S
216D-11-1-S
216D-11-1-S
SC1108D
11G
Backplate San. (E Balanced)
114E-11B-316
216E-11B-316L
328E-11B-316
328E-11B-316
SP5410E-11
11H
Backplate San. (DG Seat)
SP114G-11-316
SP216G-11-316
SP328G-11-316
SP328G-11-316
SP4410G-1
13
Packing
P214-13-12
P326-13-12
P438-13-12
P438-13-12
P438-13
-
16
Bearing (Inboard)
P214-16
P326-16
P438-16
P438-16
P438-1
17
Split Gland (2 required)
P214A-17C-1-316
P326A-17C-1-316
P438A-17C-1-316
P438A-17C-1-316
P438A-17C-
17A
Nut (Split Gland)
NU1100H-SS
NU1300H-SS
NU1300H-SS
NU1300H-SS
NU1300H
17B
Stud (Split Gland)
SP114-82-S
SP216-82-S
P326A-17D-S
P326A-17D-S
P326A-1
7
17F
Follower (E Balanced)
114E-17A-316
216E-17A-316
328E-17-316
328E-17-316
328E-17-
3
17G
Machine Screw
SC1106E-SS
SC1308H-SS
SC1308H-SS
SC1308H-SS
SC1308H
17H
O-Ring
17-106-U-25*
17-275-U
17-274-U
17-274-U
17-274
-
17I
Lockwasher (DG Seat)
Not Available
LWA1300-SS
LWA1300-SS
LWA1300-SS
LWA1300
17J
Gland Ring (DG Seat)
SP114G-17-316
SP216G-17-316
SP328G-17-316
SP328G-17-316
SP328G-1
7
17K
Bolt / Screw (DG Seat)
SC1110H-SS
SC1310H-SS
SC1311H-SS
SC1311H-SS
SC1310H
17M
Lockwasher
LWA-1100-SS
LWA-1300-SS
LWA-1300-SS
LWA-1300-SS
LWA-130
0
18
Bearing (Outboard)
P214-18
P326-18
P438-18
P438-18
P438-1
19
Frame
SP114D-19C-C
SP216D-19B-C
SP328D-19B-C
SP328D-19B-C
SP5410D-1
22
Locknut (Shaft)
P214-22
P326-22
P438-22
P438-22
P438-2
24
Impeller Retainer
114D-24B-316
216D-24B-316
328D-24B-316
328D-24B-316
328D-24
C
24A
Castellated Nut (Impeller)
SP114F-24-316
SP216F-24-316
SP328F-24-316
SP328F-24-316
SP328F-24
24B
Cotter Pin (Impeller)
16-113-1/8-x1-316
16-113-1/8-x1½-316
16-113-1/8-x2-316
16-113-1/8-x2-316
16-113-1/8-x
29
Seal Cage
P214B-29-G
P326B-29-G
P438B-29-G
P438B-29-G
P438B-29
35
Bearing Cover (Inboard)
P214-35A-C
P326-35A-C
P438-35A-C
P438-35A-C
P438-35A
37
Bearing Cover (Outboard)
P214-37A-C
P326-37A-C
P438-37A-C
P438-37A-C
P438-37A
37A
Bearing Cover Screw
SC907H-SS
SC910H-S
SC111H-SS
SC1111H-SS
SC111H-
44
Grease Fitting
P214-133
MS-100-44
MS-100-44
MS-100-44
MS-100-
Contact Tri-Clover for information on old style Type E Sanitary Water Cooler Rotary Seal replacement components. Key # 2 Impel
lers: Contact Tri-Clover for availability on other sized impellers not shown.