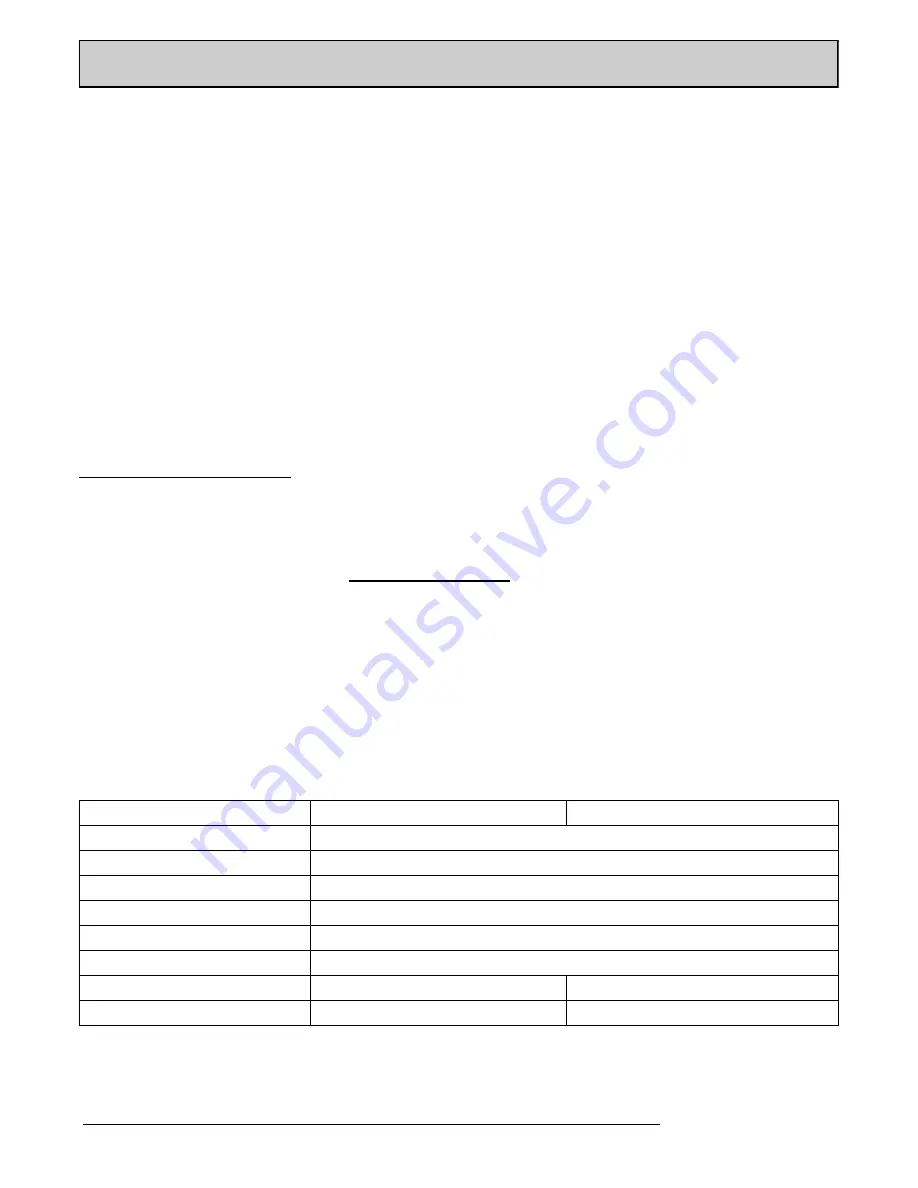
Using a 8mm punch align the hole in
the throttle lever (5) with the holes in
the handle (4). Using a small hammer
fit the throttle lever pin (7).
Tube to Handle Assembly.
Hold
handle tube (11) in vice, about six
inches (150mm) away from the valve
assembly.
Ensure that the threads of the Handle
and Tube are of Loctite 243 or a
similar product and free of oil; apply a
bead to the first few threads of the
Handle and screw in the handle (4)
until hand tight.
Looking from the top of the handle,
using a soft-faced hammer, strike the
air inlet boss downward in a clockwise
direction until tight.
Body to Handle Tube Assembly
Ensure that the thread of the lock nut
(16) is clean and free of oil; apply a
bead of Loctite 243 or a similar
product to the first few threads of the
lock nut (16).
Hold the handle tube (11) firmly in a
vice, take extra care while inserting
the spring (15) into the tube not to
contaminate the tube threads with
grease, otherwise the thread lock
adhesive will not cure, screw in the
locknut (16) until hand tight.
Using a suitable wrench, tighten the
locknut to a torque of 100lbs/ft
(135.5Nm).
Knock over the tab washer onto
one of the locknut flats.
Lubricate the mating faces of the
cowl and body with a general
purpose bearing grease.
Slide cowl (8) and spring (12)
down onto body assembly and
align the dimple on the body with
the dimple on the cowl, align the
holes using a 9mm bar.
Drive one of the spiral securing
pins (9) through the free hole.
Remove 9mm bar and fit the
second spiral pin (9).
It is important that the pins are
fitted centrally in the cowl.
Remove tool from vice and re-
position side handle (10) and
tighten the M8 caphead screw.
Machine Storage
Storage: over 3 months.
Clean the outside of the machine
and inspect the piston and
cutterhead for wear, replace any
worn parts as required.
Put a liberal amount of lubricant
into the air inlet of the tool and run
the tool for a few seconds to
disperse the oil around the tools
internal components.
Lubricate the exposed part of the
piston and cylinder.
(See recommended lubricants)
Cover the machine to protect it:
Store the machine in a dry place.
When next used, continue as per
“Starting work section”.
Disposal
When the tool and its accessories
are taken out of service for disposal,
it is recommended that: -
Dismantle into component form,
segregated according to material
composition and disposed of using
waste recycling processes specified
by local regulations.
Machinery Directive
Information
This tool has been designed and
produced in accordance with the
following directive:
2006/42/EC Machinery Directive
and applicable harmonised standard:
EN ISO 1 1148-4:2010
If your company has any problem
with our products or would like to
discuss
the
possibility
of
an
improvement being made to them,
then please do not hesitate to contact
us. Your comments are both
important and appreciated.
OPERATION / MAINTENANCE
TECHNICAL SPECIFICATIONS
COMPACTOR
SCABBLER
Length
1270mm (50)”
Weight
21.5kg (47.3lbs)
Blows per minute
1300
Air Pressure
6.2 bar (90psi)
Air Consumption
11.61 lps (25cfm)
Sound pressure level
98.0db(A)
Vibration Level (H1)*
3.5m/s
2
(K= -0% +40%)
4.2m/s
2
(K= -0% +40%)
Vibration Level (H2)*
2.9m/s
2
(K= -0% +40%)
3.9m/s
2
(K= -0% +40%)
*H1, Indicates test taken from the primary handgrip location at the trigger.
*H2, Indicates test taken from the secondary handgrip location.
Users should be aware that for other applications, the vibration readings may be higher than specified.
The 4.2 m/s² value is only applicable to compaction of MOT (DOT) type 1. sub-base material