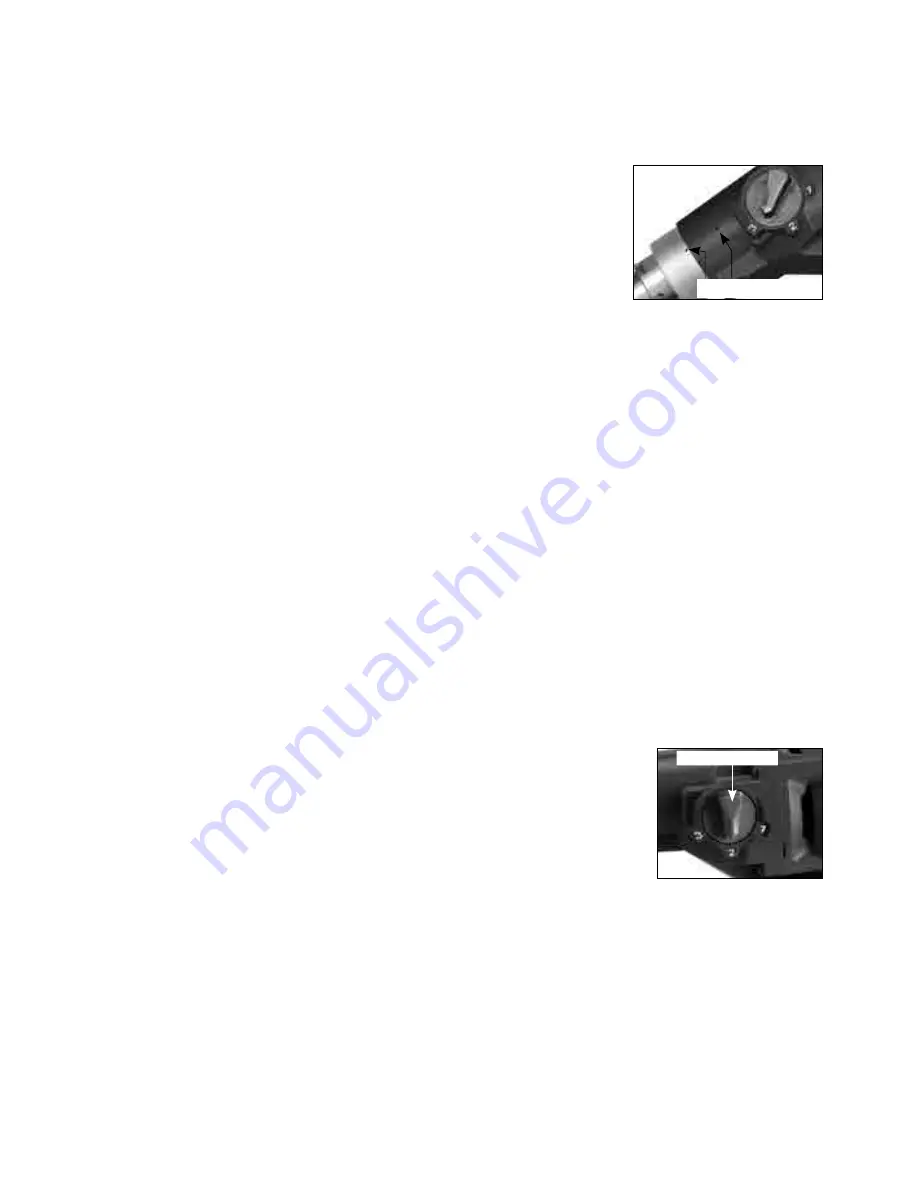
8
To connect the water supply. Attach the quick-release water coupling to a water hose.
WARNING: Never allow water to enter the motor. It could lead to an electric shock.
WARNING: Check all connections of the water feed system to ensure there
are no leaks. Inspect hoses and other critical parts which could deteriorate.
WARNING: The maximum water pressure should not exceed 70 psi (4 bar).
CAUTION: There are two small holes on the top of the gearcase. If either
of these holes leaks water, it indicates that the water seals are worn out.
Replace them immediately.
CAUTION: Never use a wet-only machine without water feed. Running dry will overheat and destroy its
water seals. Only convertible models may be used dry.
Use a water collector with a wet vacuum to collect cooling water if nearby objects could be damaged by water.
WARNING: Never allow water to enter the motor. A perfectly functioning water collector set up must be
used for any drilling performed at an upward angle.
Instructions for Inserting Adaptors for Convertible models:
To attach either the water feed adaptor head or the vacuum adaptor, the universal port on the machine's
gearbox is a bayonet connection. Align the slots on the adaptor with the tangs on the port. Insert fully and
then twist clockwise to tighten.
3) SELECTING SPEEDS
There are 3 speed ranges to suit the bit size and work piece hardness. Choose the
slowest speed for large diameter bits and hard materials. If when cutting the bit
stalls repeatedly, then you must change to a lower gear. If you are already in the
lowest gear and the bit stalls repeatedly, then you are using the machine over its
maximum capacity.
CAUTION: Never attempt to change gears on a running machine! Only adjust when the machine is
at rest.
Select the desired gear range by turning the gear selector either clockwise or counterclockwise into the desired
gear. It will usually be necessary to turn the spindle by hand a little to get it to shift all the way.
Gear Selector
Indicator Holes