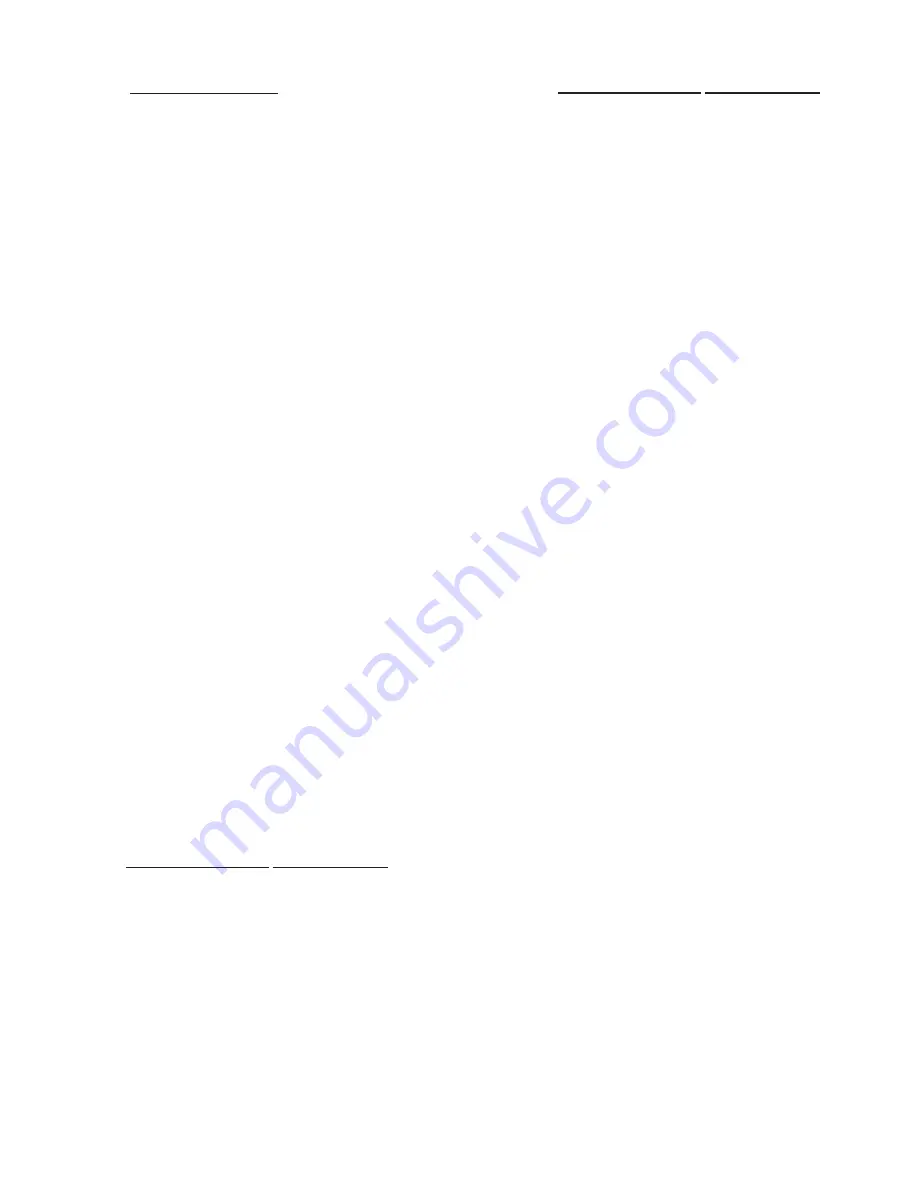
VIII. SERVICE PROCEDURES (cont
’
d)
IX. m - CHARGING SYSTEM:
WARNING: DISCONNECT THE ELECTRICAL POWER
TO THE MACHINE AND FOLLOW LOCKOUT/TAGOUT
PROCEDURES.
WARNING: THIS PROCEDURE REQUIRES THE USE OF
REFRIGERANTS. BE CERTAIN THE WORK AREA IS
WELL VENTILATED. SAFETY GOGGLES AND GLOVES
SHALL BE WORN SINCE REFRIGERANTS MAY CAUSE
INJURY TO THE SKIN.
1. Access the refrigeration system.
2. Be sure the refrigeration system is checked for
leaks and properly evacuated before charging as
outlined under
“
LEAK CHECK
”
and
“
EVACUATING SYSTEM.
”
3. Connect high side of gauge manifold to the
liquid line (make certain both valves on the gauge
manifold are closed).
NOTE: Put initial charge to system through the high
side to prevent liquid refrigerant from reaching the
compressor.
4. Connect refrigerant bottle to center connection
of gauge manifold (check the refrigerant bottle to
confirm direction for liquid).
5. Purge the hose from the refrigerant tank to the
manifold gauge.
6. Open high side of gauge manifold and allow
appropriate amount of refrigerant to flow into the
refrigeration system.
7. Disconnect the hose from the receiver valve
8. Reconnect power to the unit and check for
proper operation and high pressure leaks.
NOTE: Adjust charge as needed based on superheat
and operating pressures. Through low side of system.
9. Disconnect power to the unit and replace any
panels or covers removed.
10. Reconnect power to the unit.
IX. n - SYSTEM CLEAN UP/INTRODUCTION:
When a refrigeration system is accessed in servce
some degree of system clean up is required. There
are two levels of clean up:
•
BASIC - Conduct procedure as outlined under
“
EVACUATING SYSTEM
”
and incorporating a
drier change, this is recommended only when
system exposure is limited.
•
MASSIVE - The use of Polyol Ester (POE) oil in
systems using R-134a and R-404A, as well as in
many other applications, require that every
system failure be treated as a massive clean-up.
-14-
IX. n - SYSTEM CLEAN UP/INTRODUCTION (cont
’
d):
WARNING: DISCONNECT THE ELECTRICAL POWER
TO THE MACHINE AND FOLLOW LOCKOUT/TAGOUT
PROCEDURES.
WARNING: THIS PROCEDURE REQUIRES THE USE OF
REFRIGERANTS. BE CERTAIN THE WORK AREA IS
WELL VENTILATED. SAFETY GOGGLES AND GLOVES
SHALL BE WORN SINCE REFRIGERANTS MAY CAUSE
INJURY TO THE SKIN.
If a compressor burn-out or failure has occurred, DO
NOT install a new compressor until the clean-up pro-
cedure has been completed.
If a massive moisture contamination or POE oil break-
down has occurred, remove the old compressor as
outlined in section
“
IX. E
”
, drain the oil and hold for
replacement.
1. Recover refrigerant based on current EPA
guidelines.
2. Remove filter/drier and metering device.
NOTE: In POE oil applications, it should always be
assumed that the metering device is restricted aftre a
contamination. These devices CAN NOT be flushed
clean and reused.
3. Flush high and low sides of refrigeration system
with nitrogen to displace any trapped oil and
contaminates.
4. Reassemble refrigeration system to include
compressor, 032 size liquid line drier and new
metering device.
NOTE: The use of low flow nitrogen through the sys-
tem while welding is mandatory to prevent oxidation/
carbon plating that will lead to further contamination.
NOTE: The use of a suction drier is recommended
when moisture contamination is present. The suction
drier should be removed within 48 hours of installtion
to prevent further performance issues. Also install a
new liquid line drier for maximum system clean-up.
5. Replace new oil into the compressor.
6. Purge system with nitrogen for 5 minutes.
Pressure should be applied to the high side and
allowed to vent through the port on top of the
compressor.
7. Evacuate system for 30 minutes.
8. Repeat steps 5 and 7 two additional times.
NOTE: The final vacuum should be 200 microns or less.
9. Charge the system and replace any panels or
covers removed.
10. Reconnect power and check for proper opertion.
Summary of Contents for TBC13
Page 17: ... 16 IX WIRING DIAGRAM MODEL TBC5 ...
Page 18: ... 17 X WIRING DIAGRAM MODEL TBC13 ...
Page 19: ... 18 XI WIRING DIAGRAM MODEL TBC1H TBC1HR ...
Page 25: ... 24 ...