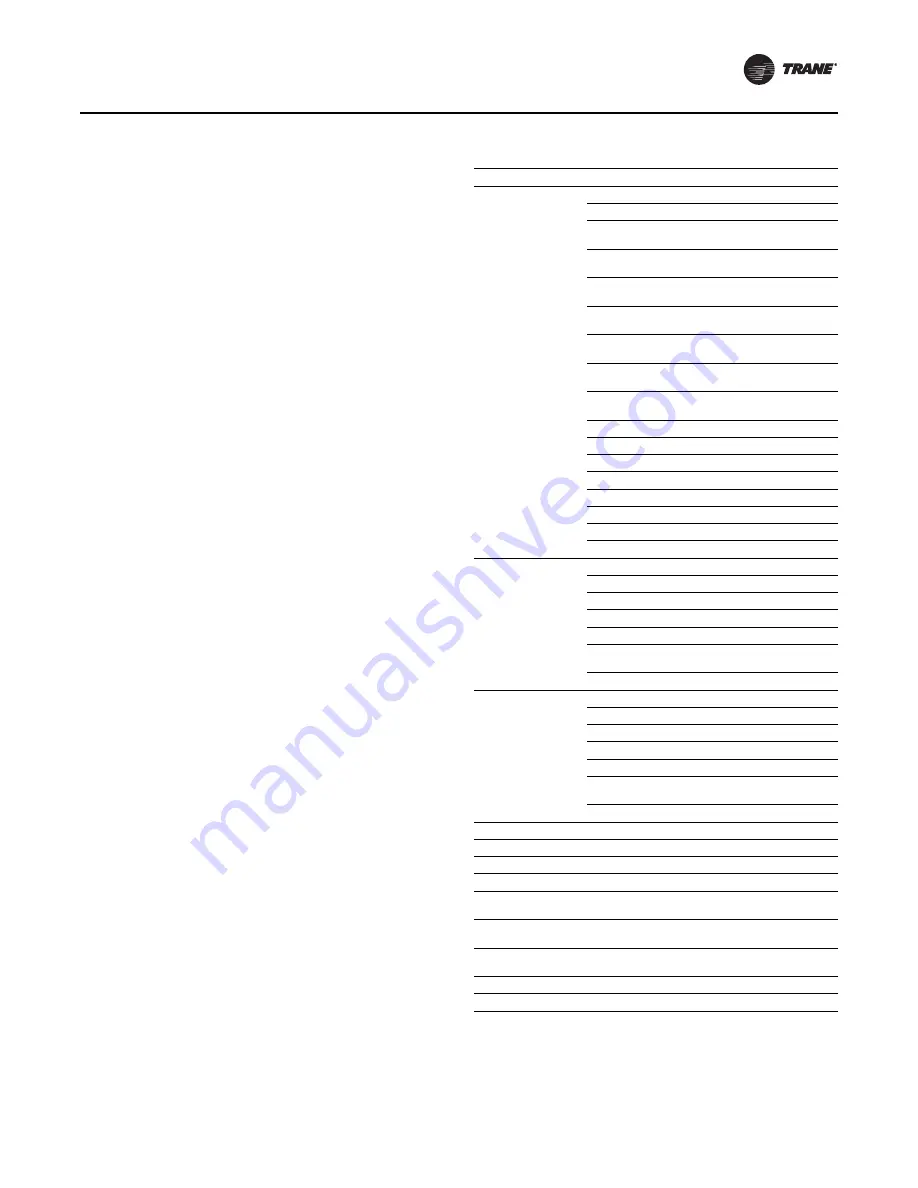
Drive and Cabinet
AFDK-SVU01C-EN
21
Tools Required
Common hand tools and hand-held power tools are
required to perform the retrofit. A trained service
technician with a well-stocked tool chest should have all of
the necessary tools to perform the job. The following list
is a sampling of the tools that one could expect to find
inside the technician’s tool chest:
•
Electric drill and bit set
•
Hacksaw or reciprocating saw
•
Extension cord
•
Screwdrivers
•
Wrenches
•
Ratchet and socket set
•
Torque Wrench
•
Nut driver set
•
Wire cutter
•
Wire stripper
•
Digital multi-meter, with phase detection capability
The following special tools are also required to perform
the retrofit:
Note:
Some field provided material will be required to
perform the replacement. This is a partial list in
addition to normal service tools and hardware.
•
Overhead or Portable Hoist (minimum 2-ton rated
capacity)
•
Spreader Bar
•
Type A to Type B USB cable
•
Computer having Tracer™ TU version 4.0 or newer
Additional Components
Additional components may be required to perform the
AFDK retrofit. These components depend on the options
selected and the existing equipment. A list of additional
components available from Trane is provided in
Some of these components may be added to an order
depending on the model number selected.
Table 2.
Options and accessories
Item Part Number Description
Qty
1
20600790100 Kit; Valve and Hardware kit for AFDK
1
Corrosion Inhibitor
1
Low pressure transducer; (PX) 0–50 PSIA,
with integral male global connector
1
Branching cable; Male to two Female, 39.37
inches long
1
Extension cable; Male to Female, 39.37 inches
long
1
Shorting buss bar kit; contains 3 bars and 12
x 0.75-16 in. hex jam nuts
1
Shorting buss bar kit; contains 3 bars and 12
x 0.75-16 in. hex jam nuts
1
Shorting buss bar kit; contains 3 bars and 12
x 0.75-16 in. hex jam nuts
1
Shorting buss bar kit; contains 3 bars and 12
x 1.12-12 in. hex jam nuts
1
Strainer; 3/4 NPTI x 3/4 NPTI w/drain
1
Valve; Ball, 3/4 copper to copper
2
Bushing; 1 NPTE x 3/4 NPTI
2
Adapter; 3/4 FTG x 1/2 M
2
Adapter; 3/4 FTG x 3/4 M
1
Adapter; 3/4 FTG x 3/4 F
1
Valve; Ball, 1/4 copper to copper
1
Adapter; 1/4 FTG x 1/4 F
1
2
20600080100 Hardware; Primary Loop Fittings
1
Adapter; 3/4Female JIC Flare X 3/4 ID Hose 8
Elbow; 3/4NPTE X 3/4 Male JIC Flare, 90°
4
Clamp; Hose—1.00 ID
8
Adapter; 3/4NPTI X 3/4 Male JIC Flare
1
Elbow; 3/4Female JIC Flare X 3/4 Male JIC
Flare, 45°
1
Elbow; 3/4NPTE X 3/4 Male JIC Flare, 45°
4
3
20600090100 Hardware; Secondary Loop Fittings
1
Adapter; 3/4Female JIC Flare X 3/4 ID Hose 8
Elbow; 3/4NPTE X 3/4 Male JIC Flare, 90°
4
Clamp; Hose—1.00 ID
8
Adapter; 3/4NPTI X 3/4 Male JIC Flare
1
Elbow; 3/4Female JIC Flare X 3/4 Male JIC
Flare, 45°
1
Elbow; 3/4NPTE X 3/4 Male JIC Flare, 45°
4
4
20600880100 Assembly; PUMP/HX Water to Water Frame 3 1
5
20600890100 Assembly; PUMP/HX Water to Water Frame 4 1
6
20600900100 Assembly; PUMP/HX Water to Air Frame 3
1
7
20600910100 Assembly; PUMP/HX Water to Air Frame 4
1
8
HSE01285
Hose; 3/4 ID, Rubber, Cloth Braid, 300 PSI
30
FT
9
HSE01286
Hose; 3/4 ID, Rubber, Cloth Braid, 300 PSI
60
FT
10
HSE01287
Hose; 3/4 ID, Rubber, Cloth Braid, 300 PSI
120
FT
11
CHM00481
Corrosion Inhibitor
1
12
PAI00061
Paint; Executive Beige, Spray
1
In addition to the required components listed in
,
motor brushes may optionally be installed. Motor brushes
reduce the wear on compressor motor bearings due to the
additional stresses from the application of adjustable