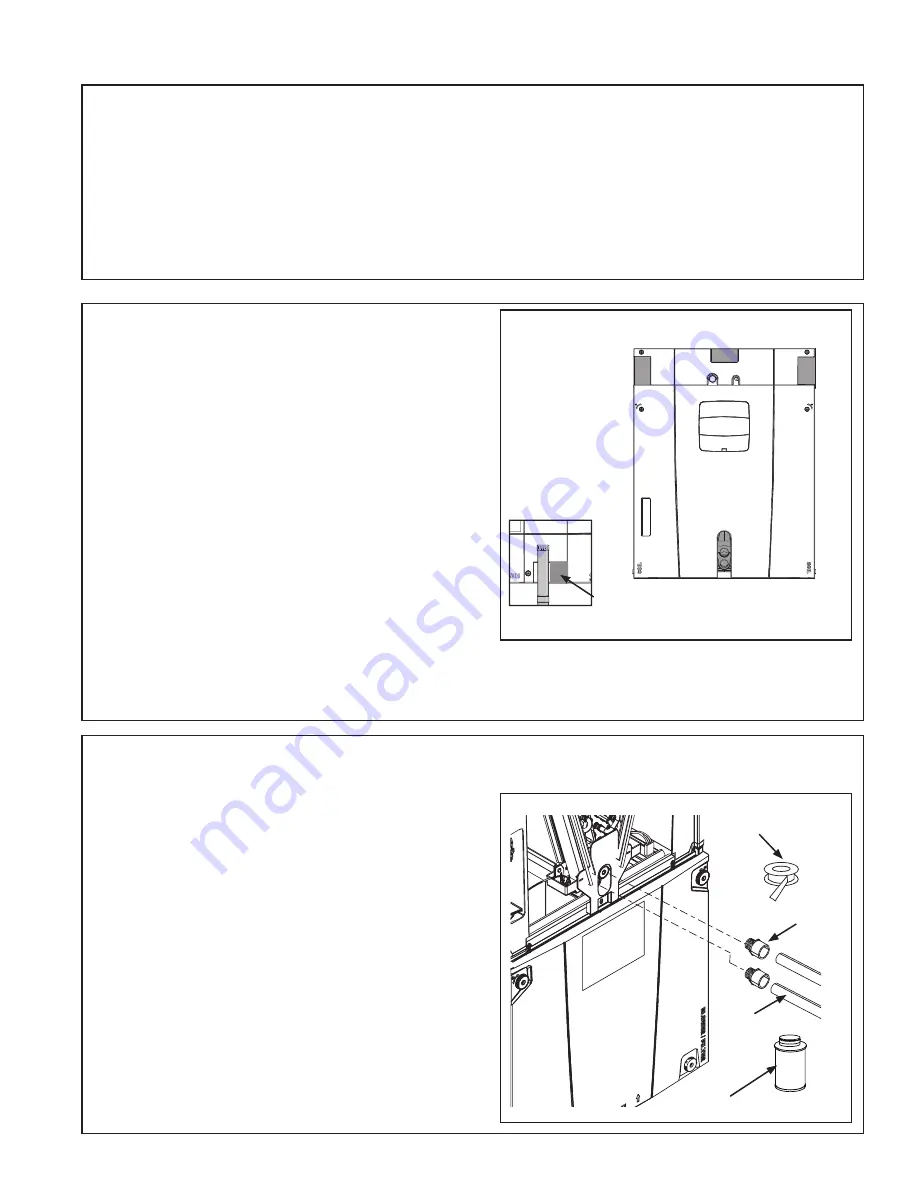
25
PVC
CEMENT
Section 12. Condensate Drain Piping
12.2 Connect Condensate Drain Piping
Note:
Downflow and horizontal orientations require the
Line Set panel to be removed in order to make the drain
connections.
Note:
Make certain that the unit has been installed in a
level position to allow for proper draining.
STEP 1
- Select the drain connections that are oriented
for your application.
STEP 2
- Prepare the condensate drain connections.
• From the factory, the unit comes with plugs in both
upflow condensate drains and an additional plug in the
documentation packet.
• For upflow applications, remove upflow condensate
plug(s) and connect condensate piping.
• For all other applications, do not remove upflow con-
densate plugs. Remove the cover from the needed
condensate drain connections and connect condensate
piping.
• If the secondary condensate opening is not used, plug
the condensate opening with the fitting supplied in the
documentation pack. Use scissors to cut the air seal in
half and re-install over the unused opening.
Horizontal Left
Condensate Drains
Upflow
Condensate
Drains
Downflow Condensate
Drains
Horizontal Right
Condensate Drains
S
P
S
P
S
P
S
P
Drain Nipple
3/4” PVC pipe
Teflon Tape
PVC/CPVC Cement
12.1 Condensate Drain Piping Considerations
• Condensate drain plumbing must comply with na-
tional, state, and local codes.
• Route condensate drain lines away from air handler
so they do not interfere with access panels.
• Slope the drain lines downward a minimum of 1/4”
per foot, support per local codes.
• A 1.5” minimum distance from the coil panel to the
inside of the condensate tubing is recommended
for coil panel removal.
• Do not use reducing fittings in the condensate
drain lines.
• Do not connect the drain line to a closed drain
system.
• Do not use a torch or flame near the plastic drain
pan coupling.
• A P-trap is not required for proper drainage due to
the positive pressure of the air handler; however,
it is recommended to prevent efficiency loss of
conditioned air.
Important:
For Horizontal and Downflow installations,
the following order must be observed:
1) Remove panel and insert the 3/4” nipples.
2) Reinstall the panel.
3) Connect the condensate lines to the nipples.
•
Dry fit and test clearance for coil panel removal
before applying PVC/CPVC cement
•
Use Teflon tape on the air handler drain line
connections. Do not use pipe joint compound
or PVC/CPVC cement on drain nipple.
•
Hand tighten the drain pipe.
STEP 3
- For Upflow installations, connect 3/4” PVC
pipe to the threaded drain nipple with PVC/CPVC
cement. 1.5” minimum clearance to the condensate
piping is needed for coil panel removal. Thread the
assembly into the primary drain connection (repeat
for the secondary drain connection if used).
Air seal
over secondary
drain
Note:
A small amount of sealant must be applied
around the drain line(s) passing through the panel
to prevent air leakage and possible water drips.
Note:
A small amount of sealant must be applied
around the drain line(s) passing through the panel
to prevent air leakage and possible water drips.
Optional pipe kit BAYCNDPIP01A is available
(10 pcs per kit).