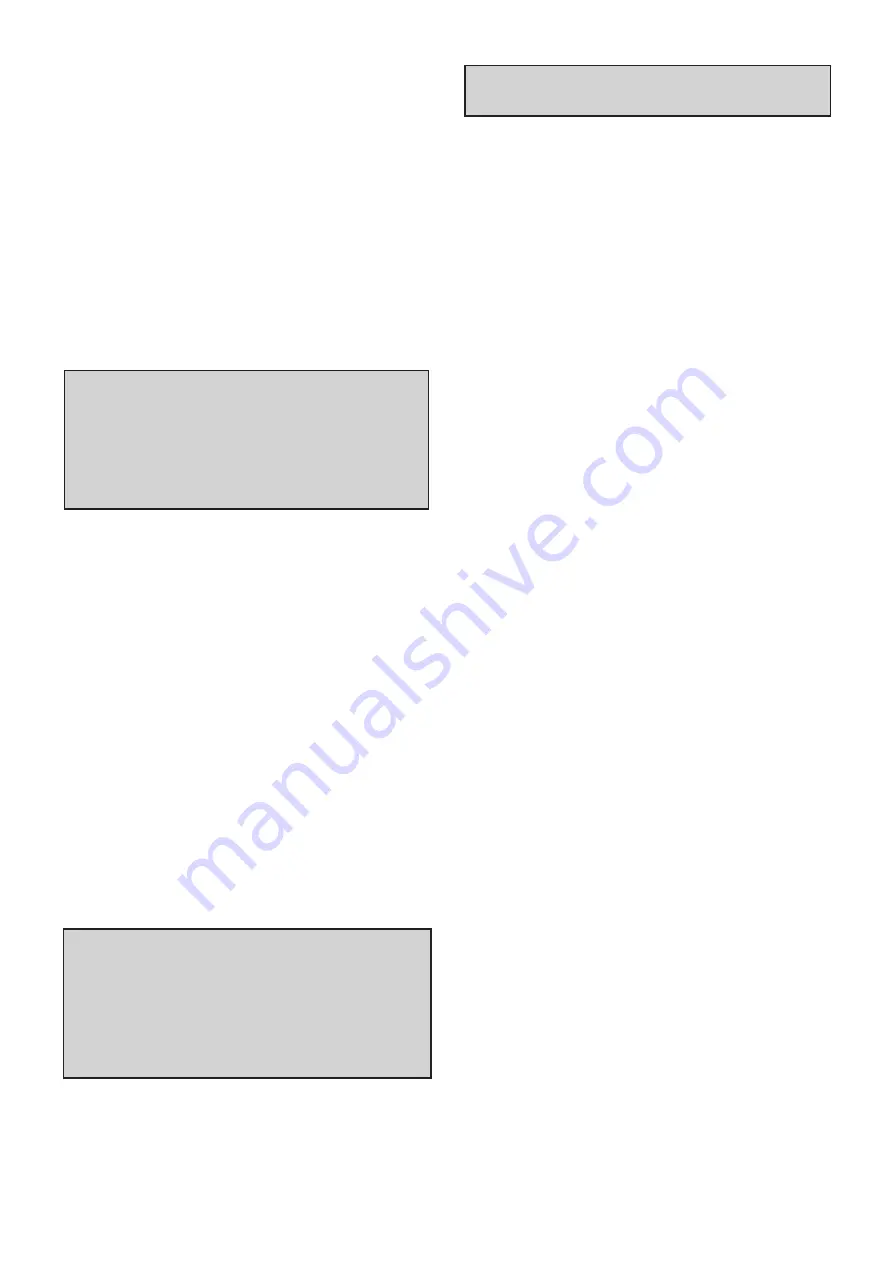
UCM-CLD set-up
Refer to manual of operation of the UCM-CLD,
reference L80 IM 025 E.
Start-up procedures
If the pre-start checkout, as discussed above, has been
completed, the unit is ready to start.
- Move the chiller switch on the UCM-CLD to the
STOP/RESET position.
- As necessary, adjust the setpoint values in the UCM
menus, as describe in the Operation Manual.
- Close the fused-disconnect switch for the chilled water
pump. Energize the pump to start chilled water circula-
tion.
- Check the service valves on the discharge line, suction
line, oil line and liquid line for each circuit. These valves
must be open (backseated) before starting the com-
pressors.
Caution :
To prevent compressor damage, do not oper-
ate the unit until all refrigerant and oil line service valves
are opened.
Caution :
The compressor sump heaters must be ener-
gized for a minimum of 24 hours prior to unit opera-
tion, to prevent compressor damage caused by liquid
refrigerant in the compressor at start-up.
- Energize the evaporator heat tape by closing the field-
installed fused-disconnect.
- Move the chiller switch to AUTO LOCAL. If the chiller
module calls for cooling and all safety interlocks are
closed, the unit will start. The compressor(s) will load
and unload in response to the temperature of the leav-
ing chilled water temperature.
Once the system has been operating for approximately 30
minutes and has become stabilized, complete the start-up
procedures, as follows :
- Check the evaporator and condenser refrigerant pres-
sures on the UCM-CLD.
- Measure the system superheat. Refer to «System super-
heat», below.
- Measure the system subcooling. Refer to «System sub-
cooling», below.
- A shortage of refrigerant is indicated if operating pres-
sures are low and subcooling is also low. If the operat-
ing pressures, superheat and subcooling readings indi-
cate a refrigerant shortage, gas charge refrigerant into
each circuit, as required. With the unit running, add refrig-
erant vapor by connecting the charging line to the suc-
tion service valve until operating conditions become nor-
mal.
Caution :
If both suction ans discharge pressures are
low but subcooling is normal, a problem other than
refrigerant shortage exists. Do not add refrigerant, as this
may result in overcharging the circuit.
Caution :
Use only refrigerants specified on the unit
nameplate, to prevent compressor damage and insure
full system capacity.
- If operating conditions indicate a refrigerant overcharge,
remove refrigerant at the liquid line service valve. Allow
refrigerant to escape slowly, to minimize oil loss. Do not
discharge refrigerant into the atmosphere.
Warning :
Do not allow refrigerant to directly contact
skin or injury from frostbite may result.
System superheat
Normal superheat for each circuits is approximately 4°C at
full operating load. Superheat temperature can be expect-
ed to be moving around the 4°C setpoint when the chiller
is pulling down, the compressor slide valve is being mod-
ulated, or the fans are staging on either the same or oppo-
site circuits. Superheat can be expected to settle out at
approximately 4°C when the above items stabilize.
System subcooling
Normal subcooling for each circuit is 5°C to 7-8°C. If sub-
cooling for either circuit does not approximate these figures,
check the superheat for the circuit and adjust, if required.
If superheat is normal but subcooling is not, contact a qual-
ified Trane service technician.
Unit shutdown procedures
Temperatures shutdown and restart
To shut the unit down for a short time, use the following
procedure :
1. Move the chiller switch to STOP/RESET. The compres-
sors will continue to operate and, after unloading for
20 seconds, will stop when the compressor contactors
de-energize. The condenser fans will be de-energized
at this time.
2. The unit disconnect switch and unit mounted disconnect
(if installed) should remain closed to keep the com-
pressor sump heaters energized.
3. Maintain power to 1TB3-11 and 1TB3-12 to keep the
evaporator heat tape energized.
4. Stop the chilled water circulation by turning off the
chilled water pump.
To restart the unit after a temporary shutdown, restart
the chilled water pump and move the chiller switch to
either of the AUTO positions. The unit will start normal-
ly, provided the following conditions exist :
1. The UCM must receive a call for cooling and the dif-
ferential to start must be above the setpoint.
2. All system operating interlocks and safety circuits
must be satisfied.
24
Summary of Contents for RTRA 107
Page 30: ...30 Notes ...
Page 31: ...31 Notes ...