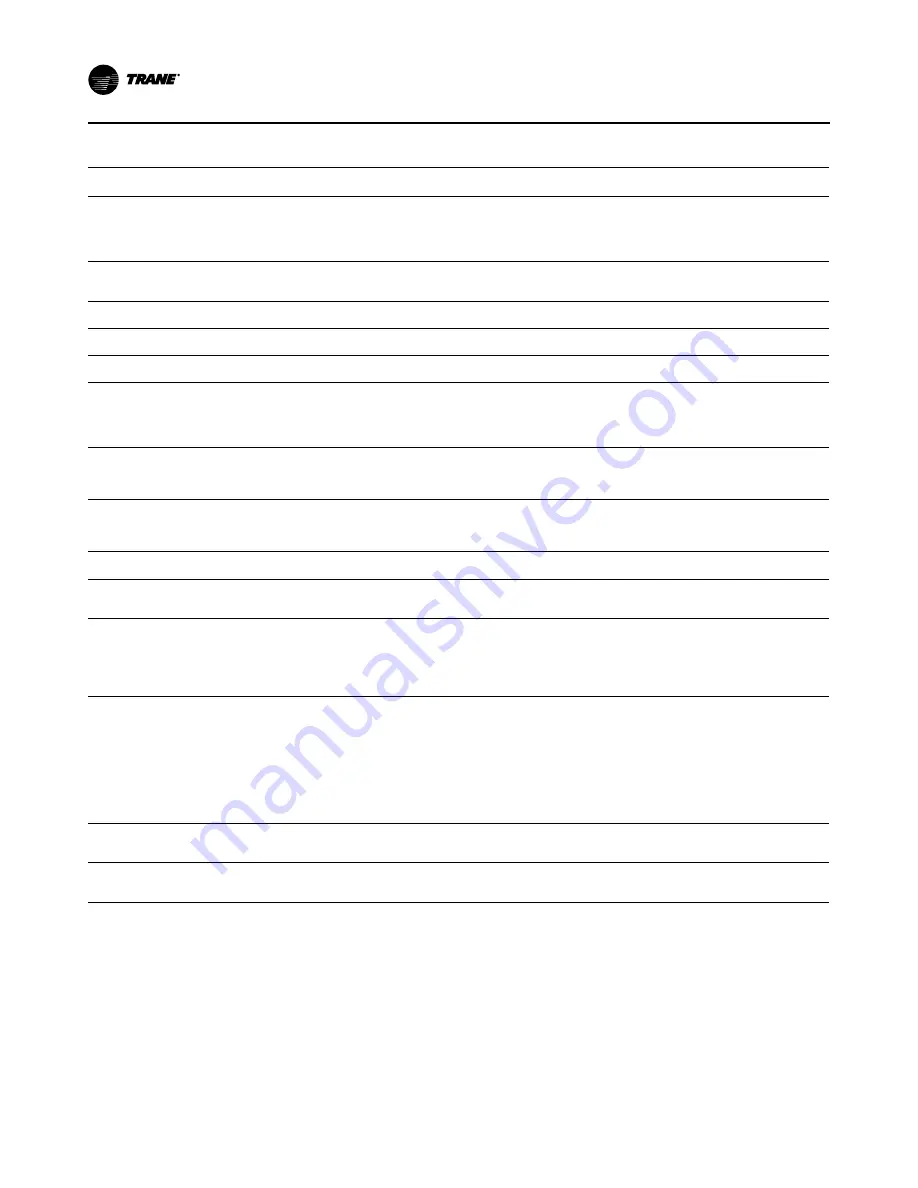
Diagnostics
116
RTHD-SVX02H-EN
Table 35. Diagnostics Table
Hex
Code
Diagnostic Name
and Source
Severity
Persistence Criteria
Reset
Level
1AD
MP Application Mem-
ory CRC Error
Immediate
Latch
App software inside the MP failed its own checksum test. Possible
causes: application software in the MP is not complete - software
download to the MP was not completed successfully - or MP hard-
ware problem. Note: User should attempt to reprogram the MP if
this diagnostic occurs.
Remote
6A1
MP: Could not Store
Starts and Hours
Info
Latch
MP has determined there was an error with the previous power
down store. Starts and Hours may have been lost for the last 24
hours.
Remote
5FF
MP: Invalid Configu
-
ration
Immediate
Latch
MP has an invalid configuration based on the current software
installed
Remote
6A2
MP: Non-Volatile
Block Test Error
Info
Latch
MP has determined there was an error with a block in the
Non-Volatile memory. Check settings.
Remote
69C
MP: Non-Volatile
Memory Reformat
Info
Latch
MP has determined there was an error in a sector of the Non-Vol-
atile memory and it was reformatted. Check settings.
Remote
D9
MP: Reset Has Oc-
curred
Info
NonLatch
The main processor has successfully come out of a reset and built
its application. A reset may have been due to a power up, install-
ing new software or configuration. This diagnostic is immediately
and automatically cleared and thus can only be seen in the His-
toric Diagnostic List in TechView
Remote
297
No Differential Re-
frigerant Pressure
Immediate
Latch
The system differential pressure was below 7.7 Psid. The occur-
rence of this diagnostic will saturate the above “Low Diff Rfgt
Press” Integral and invoke the same “Compressor Cool Down” op
mode.
Remote
1E1
Oil Flow Protection
Fault
Immediate
Latch
The Oil Pressure Transducer for this Chiller is reading a pressure
either above its Condenser Pressure by 15 Psia or more, or below
its Evaporator Pressure 10 Psia or more for 30 seconds continu-
ously.
Local
5BE
Oil Pressure Trans-
ducer
Normal
Latch
Bad Sensor or LLID
Remote
A1
Outdoor Air Tem-
perature Sensor
Info and Spe-
cial Action
Latch
Bad Sensor or LLID. This diagnostic will only occur if OA sensor
is configured.OA Chilled water reset will be suspended if selected
and Tracer OA unavailable.
Remote
D7
Over Voltage
Normal
NonLatch
a. Average of all monitored Line voltages above + 10% of nom-
inal. [Must hold = + 10 % of nominal. Must trip = + 15 % of
nominal. Reset differential = min. of 2% and max. of 4%. Time
to trip = minimum of 1 min. and maximum of 5 min.) Design:
Nom. trip: 60 seconds at greater than 112.5%, + or - 2.5%,
Auto Reset at 109% or less.
Remote
E4
Phase Loss
Immediate
Latch
a) No current was sensed on one or two of the current transform-
er inputs while running or starting (See Nonlatching Power Loss
Diagnostic for all three phases lost while running). Must hold =
20% RLA. Must trip = 5% RLA. Time to trip shall be longer than
guaranteed reset on Starter Module at a minimum, 3 seconds
maximum. Actual design trippoint is 10%. The actual design trip
time is 2.64 seconds. b) If Phase reversal protection is enabled
and current is not sensed on one or more current xformer inputs.
Logic will detect and trip in a maximum of 0.3 second from com-
pressor start.
Local
E5 or
E5
Phase Reversal
Immediate
Latch
A phase reversal was detected on the incoming current. On a
compressor startup the phase reversal logic must detect and trip
in a maximum of 0.3 second from compressor start.
Local
E3
Phase Unbalance Se-
vere Current Imbal-
ance
Normal
Latch
A 30% Phase cCurrent Unbalance imbalance has been detected
on one phase relative to the average of all 3 phases for 90 con-
tinuous seconds.
Local
Summary of Contents for RTHD series
Page 120: ...120 RTHD SVX02H EN...
Page 122: ...122 RTHD SVX02H EN...
Page 123: ...RTHD SVX02H EN 123 EXV...
Page 124: ...124 RTHD SVX02H EN...
Page 125: ...RTHD SVX02H EN 125...
Page 126: ...126 RTHD SVX02H EN RLA 0 10VDC RLA 0 10V 2 10VDC 4 20mA 2 10VDC 4 20mA TRACER SUMMIT LONTALK...
Page 127: ...RTHD SVX02H EN 127 2 10VDC 4 20mA TRACER SUMMIT LONTALK 4 20mA 2 10VDC 4 20mA 2 10VDC...
Page 128: ...128 RTHD SVX02H EN 1A24...
Page 129: ...RTHD SVX02H EN 129...
Page 130: ...130 RTHD SVX02H EN UC800 RLA 115V 27V 115V TD 7...
Page 132: ...132 RTHD SVX02H EN...
Page 133: ...RTHD SVX02H EN 133 EXV 2 EXV 1...
Page 134: ...134 RTHD SVX02H EN...
Page 135: ...RTHD SVX02H EN 135...
Page 136: ...136 RTHD SVX02H EN...
Page 137: ...RTHD SVX02H EN 137...
Page 138: ...138 RTHD SVX02H EN 1A24...
Page 139: ...RTHD SVX02H EN 139...
Page 140: ...140 RTHD SVX02H EN UC800 RLA 115V 27V 115V TD 7 27V...
Page 142: ...142 RTHD SVX02H EN...
Page 144: ...144 RTHD SVX02H EN HEAT RECOVERY OIL TANK EVAPORATOR CONDENSER Heat Recovery Model...
Page 145: ...RTHD SVX02H EN 145 ERY CONTROL PNAEL SEE DETAIL A G...
Page 146: ...146 RTHD SVX02H EN...
Page 147: ...RTHD SVX02H EN 147 C A DIVISION OF AMERICAN STANDARD INC ALL RIGHTS RESERVED...
Page 148: ...148 RTHD SVX02H EN HEAT RECOVERY OIL TANK EVAPORATOR CONDENSER DETAIL A Heat Recovery Model...
Page 149: ...RTHD SVX02H EN 149 ERY CONTROL PNAEL SEE DETAIL A...