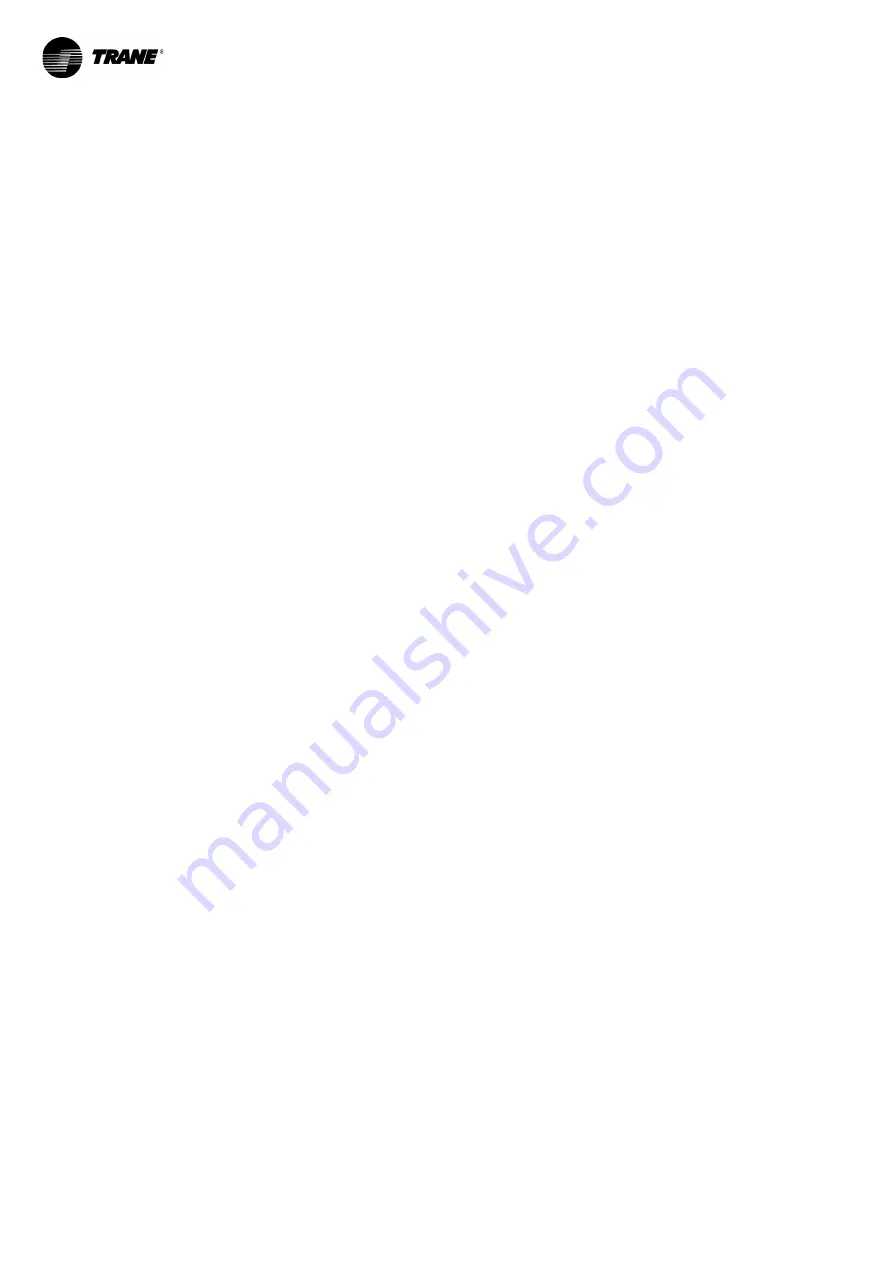
Page 23
10 ELECTRICAL PANEL
When reviewing this manual keep in mind:
• All field-installed wiring must be in accordance with local regulations, CE directives and guidelines. Be sure to satisfy
proper equipment grounding requirements according to CE
• The standardized values - Maximum Amps –Maximum kW are displayed on unit nameplate.
• All field-installed wiring must be checked for proper terminations, and for possible shorts or grounds.
Ensure total protection against the possible penetration of water into the connection point.
All the cables and the terminals are univocally numbered according to the electrical scheme in order to avoid possible
misinterpretation. The identification system of the cables connected to the components allow also an easy and intuitive
recognition of the component. Each component of the electrical panel is provided with an identification plate according to
what is shown on the electrical scheme. All the connections to the electrical panel are made from the bottom and are
equipped with cover preventing from break. The electrical panel supply is 400V/3ph+n/50Hz suitable for TN-S system and
no additional power supply is necessary. If the unit is powered by a TN-C, TT or IT power supply system the TRANE
catalogue option “power supply without neutral 400V/3ph/50Hz” must have been ordered and implemented in the unit’s
electrical cabinet. The entrance for the power cables is provided on the bottom of the box where a dismountable flange
suitable for the purpose is provided.
The control circuit is powered with 24 VAC. Each unit is provided with auxiliary transformer control circuit 230/24V. It
requires no additional power cable for the control equipment.
The circuit also an electric resistance installed in the compressor in order to keep warm the oil and thus avoid the
transmigration of the refrigerant in its interior. Obviously, the operation of the electrical resistors is ensured as long as the
unit is power supplied.
The unit is equipped with an alarm relay, which changes state every time an alarm occurs in one of the cooling circuits.
Connect the terminals as per the wiring diagram on the unit - terminal “X” - a visual or audible alarm or any external
supervision system.
BMS to monitor its operation is allowed. See the wiring diagram of the unit for wiring.
WARNING
Hazardous Voltage with Capacitor! Disconnect all electric power, including remote disconnects and discharge
all motor start/run and capacitors before servicing. Follow proper lockout/tagout procedures to ensure the power cannot be
inadvertently energized.
For variable frequency drives or other energy storing components provided by TRANE or others, refer to the appropriate
manufacturer’s literature for allowable waiting periods for discharges capacitors. Verify with an appropriate voltmeter that
all capacitors have discharged.
After disconnecting input power, wait five (5) minutes for units which are equipped with EC fans and wait twenty (20)
minutes for units which are equipped with variable frequency drive (0V DC) before touching any internal components.
Failure to follow these instructions could result in death or serious injury.
IMPORTANT
if the unit is powered by a TT power supply system a differential protection should be suited for industrial
machinery with current leak than can be higher than 500 mA (several motors and frequency drives)