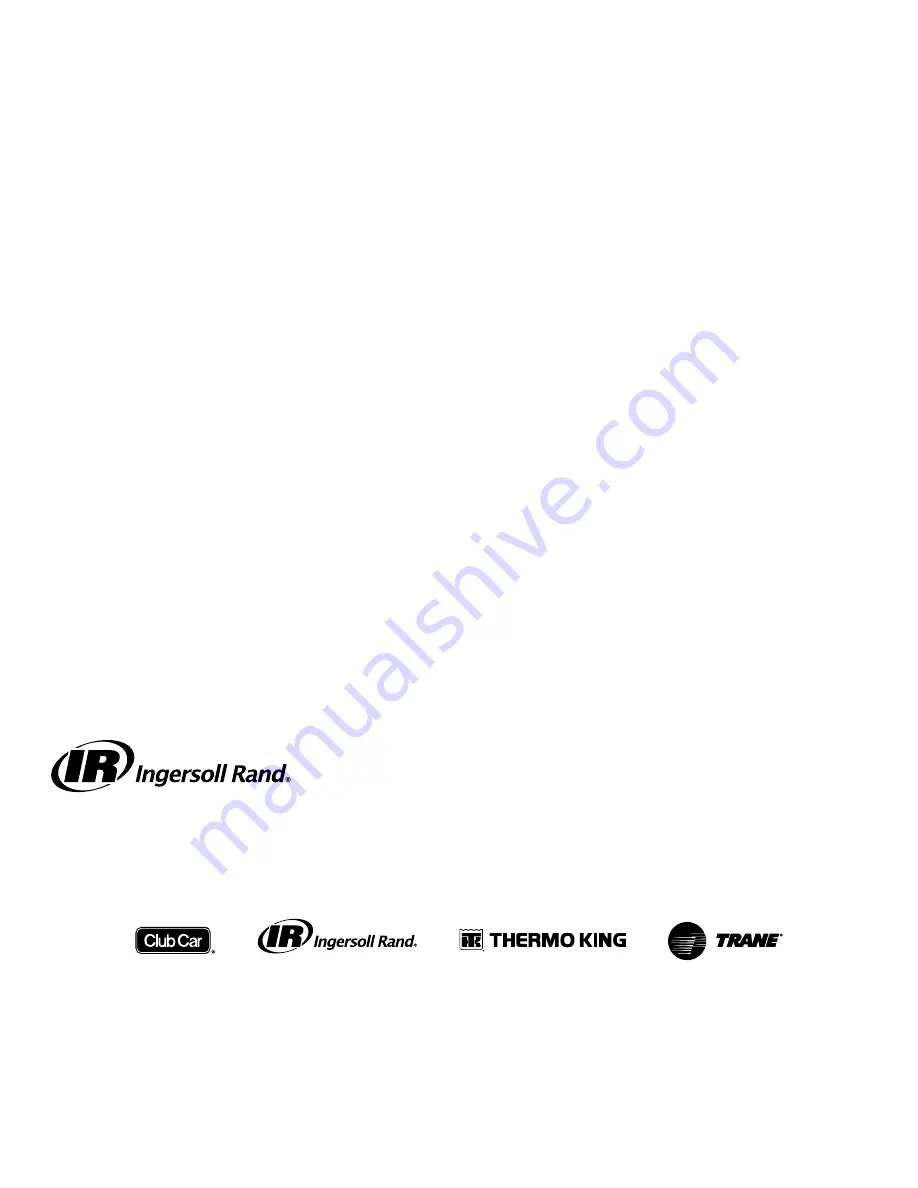
Ingersoll Rand (NYSE: IR) advances the quality of life by creating comfortable, sustainable and efficient
environments. Our people and our family of brands — including Club Car
®
, Ingersoll Rand
®
, Thermo King
®
and
Trane
®
— work together to enhance the quality and comfort of air in homes and buildings; transport and protect
food and perishables; and increase industrial productivity and efficiency. We are a global business committed to a
world of sustainable progress and enduring results.
ingersollrand.com
Ingersoll Rand has a policy of continuous product and product data improvements and reserves the right to change design and specifications
without notice.
We are committed to using environmentally conscious print practices.
PRGD-SVX01F-EN
20 Jul 2017
Supersedes PRGD-SVX01E-EN
(November 2016)
©2017 Ingersoll Rand
Summary of Contents for PRGD series
Page 35: ...PRGD SVX01F EN 35 S Sc ch he em ma at ti ic c W Wi ir ri in ng g D Di ia ag gr ra am m ...
Page 36: ...36 PRGD SVX01F EN S Sc ch he em ma at ti ic c W Wi ir ri in ng g D Di ia ag gr ra am m ...
Page 37: ...PRGD SVX01F EN 37 N No ot te es s ...
Page 38: ...38 PRGD SVX01F EN N No ot te es s ...