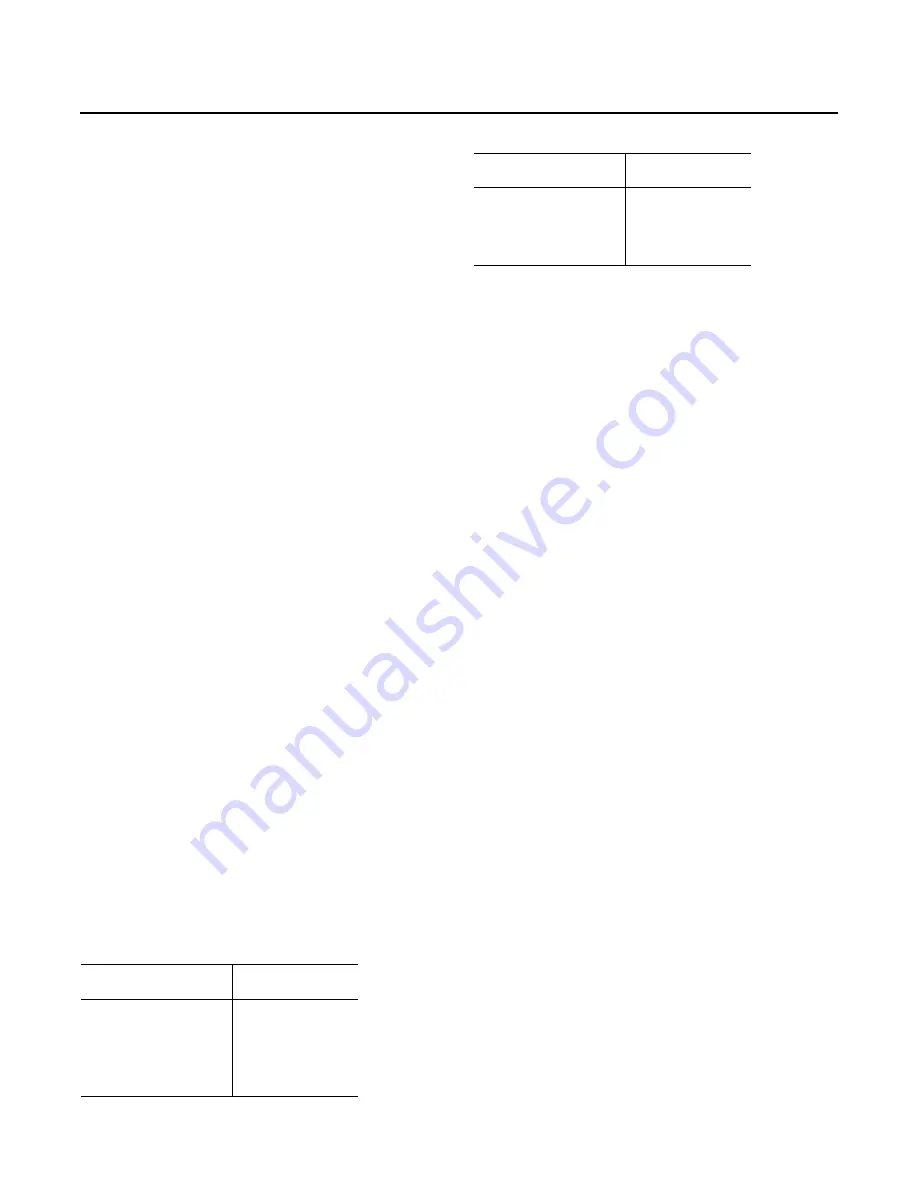
Troubleshooting
RT-SVX22J-EN
55
The RTRM will ignore the closing of this Normally Open
switch for 2 (±1) minutes. This helps prevent nuisance
SERVICE LED indications. The exception is the LED will
flash 40 seconds after the fan is turned “On” if the Fan
Proving Switch is not made.
Clogged Filter Switch
This LED will remain lit the entire time that the Normally
Open switch is closed. The LED will be turned off
immediately after resetting the switch (to the Normally
Open position), or any time that the IDM is turned “Off”.
If the switch remains closed, and the IDM is turned “On”,
the SERVICE LED will be turned “On” again after the 2 (±1)
minute ignore delay.
This LED being turned “On”, will have no other affect on
unit operation. It is an indicator only.
Fan Failure Switch
When the “Fan Failure” switch is wired to the RTOM, the
LED will remain flashing the entire time the fan proving
switch is closed, indicating a fan failure, and it will shut the
unit operations down.
Condensate Overflow Switch
When the “Condensate Overflow Switch" is closed, a drain
pan overflow condition is indicated and it will shut unit
operations down.
Zone Temperature Sensor (ZTS)
Test
Note:
These procedures are not for programmable or
digital models and are conducted with the Zone
Sensor Module electrically removed from the
system.
Test 1 - Zone Temperature Thermistor
(ZTEMP)
This component is tested by measuring the resistance
between terminals 1 and 2 on the Zone Temperature
Sensor. Below are some typical indoor temperatures, and
corresponding resistive values.
Test 2 - Cooling Set Point (CSP) and
Heating Set Point (HSP)
The resistance of these potentiometers are measured
between the following ZSM terminals. Refer to the chart
above for approximate resistances at the given setpoints.
Cool SP = Terminals 2 and 3
Range = 100 to 900 Ohms approximate
Heat SP = Terminals 2 and 5
Range = 100 to 900 Ohms approximate
Test 3 - System Mode and Fan Selection
The combined resistance of the Mode selection switch and
the Fan selection switch can be measured between
terminals 2 and 4 on the Zone Sensor. The possible switch
combinations are listed below with their corresponding
resistance values.
Test 4 - LED Indicator Test, (SYS ON, HEAT,
COOL & SERVICE)
Method 1
Testing the LED using a meter with diode test function. Test
both forward and reverse bias. Forward bias should
measure a voltage drop of 1.5 to 2.5 volts, depending on
your meter. Reverse bias will show an Over Load, or open
circuit indication if LED is functional.
Method 2
Testing the LED with an analog Ohmmeter. Connect
Ohmmeter across LED in one direction, then reverse the
leads for the opposite direction. The LED should have at
least 100 times more resistance in reverse direction, as
compared with the forward direction. If high resistance in
both directions, LED is open. If low in both directions, LED
is shorted.
Method 3
To test LED’s with ZSM connected to unit, test voltages at
LED terminals on ZSM. A measurement of 32 VDC, across
an unlit LED, means the LED has failed.
Relative Humidity Sensor Test
This component is measured by measuring the mA output
signal on the Relative Humidity Sensor. Verify accuracy of
the sensor annually. If the output reading is 0 mA, first
verify that power is applied to the sensor. A reading of 4
mA corresponds to 0% RH and 20 mA corresponds to 100%
RH.
Table 14. Cooling setpoint and heating setpoint
Zone Temperature
Nominal ZTEMP
Resistance
50° F
10.0°C
19.9 K-Ohms
55° F
12.8°C
17.47 K-Ohms
60° F
15.6°C
15.3 K-Ohms
65° F
18.3°C
13.49 K-Ohms
70° F
21.1°C
11.9 K-Ohms
75° F
23.9°C
10.50 K-Ohms
80° F
26.7°C
9.3 K-Ohms
85° F
29.4°C
8.25 K-Ohms
90° F
32.2°C
7.3 K-Ohms
Table 14. Cooling setpoint and heating setpoint
Zone Temperature
Nominal ZTEMP
Resistance
Summary of Contents for Precedent THC036E
Page 37: ...Installation RT SVX22J EN 37 Figure 51 Examples...
Page 63: ......