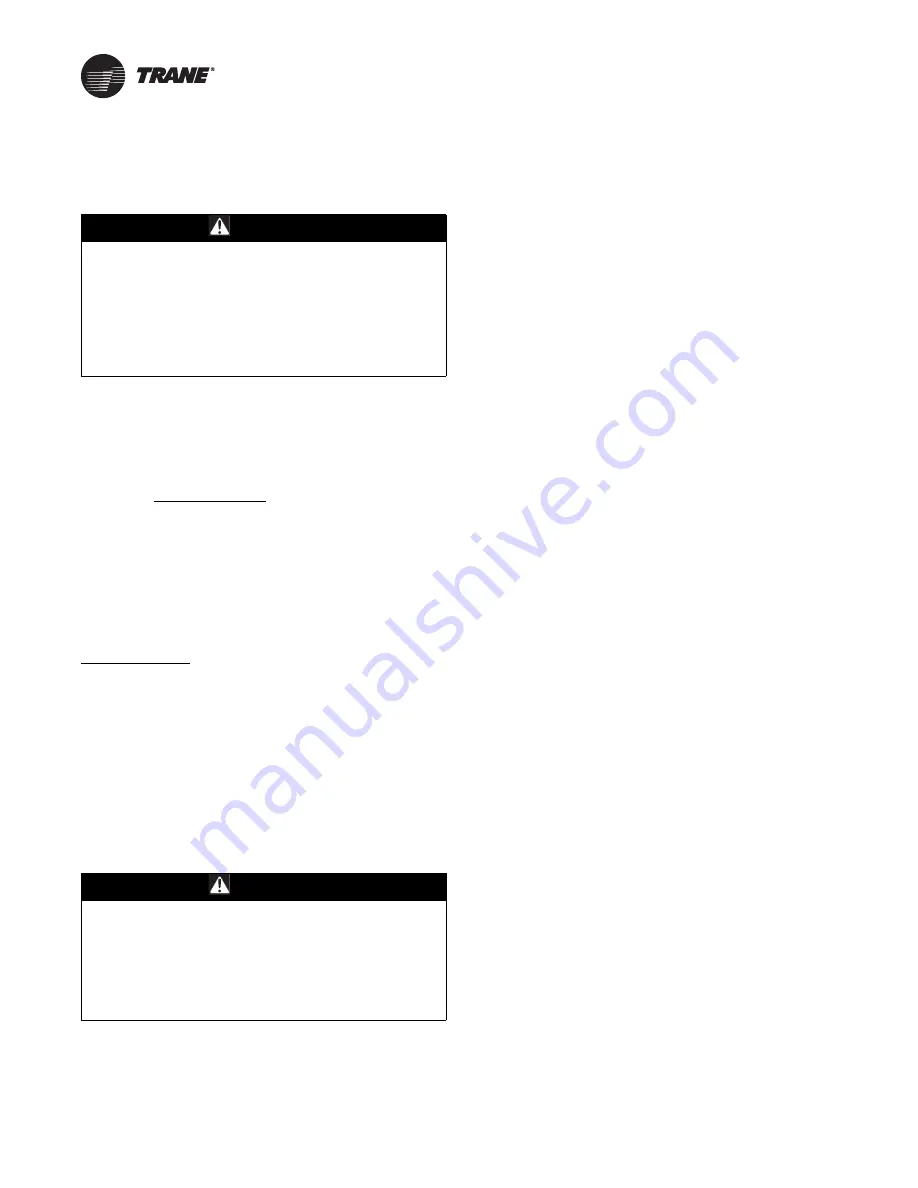
16
GMND-SVX01B-EN
Installation: Piping
Gas Piping
Pipe Sizing
To provide adequate gas pressure to the gas duct furnace,
size the gas piping as follows:
1.
Find the ft
3
/hr by using the following formula:
2. Refer to
Table 4, p. 17
. Match “Length of Pipe” with
appropriate “Gas Input - Ft
3
/Hr” value. This value can
then be matched to the pipe size at the left of the table.
Example: It is determined that a 67 foot (20.4 m) run of
gas pipe is required to connect a 200 MBtu gas duct
furnace to a 1,000 Btu/ft
3
(0.29 kW) natural gas supply.
Using
Table 4, p. 17
, a 1-inch pipe is needed.
Notes:
•
See
“General Safety Information,” p. 7
for English/SI
(metric) unit conversion factors.
•
If more than one gas duct furnace is to be served by the
same piping arrangement, the total cubic feet per hour
input and length of pipe must be considered.
•
If the gas duct furnace is to be fired with LP gas, consult
the local LP gas dealer for pipe size information.
Before any connection is made to an existing line
supplying other gas appliances, contact the local gas
company to make certain that the existing line is of
adequate size to handle the combined load.
WARNING
Flammable Vapors!
When connecting to existing gas lines be sure to valve
off the gas supply ahead of connection point. To avoid
explosion or possible fire, always purge all residual gas
from piping before cutting into existing line or
removing threaded fittings. Failure to remove all gas
vapors could result in death or serious injury or
equipment or property-only damage.
ft
3
/hr =
Input
Btu per ft
3
200,000 Btu/hr
= 200 ft
3
/hr
1,000 Btu/ft
3
WARNING
Hazard of Explosion and Fire!
Heater installation for use with propane (LP gas) must
be made by a qualified LP Gas Dealer or LP Gas Installer
to ensure that all appropriate codes, installation
procedures, and precautions have been followed.
Failure to follow these instructions could result in death
or serious injury.