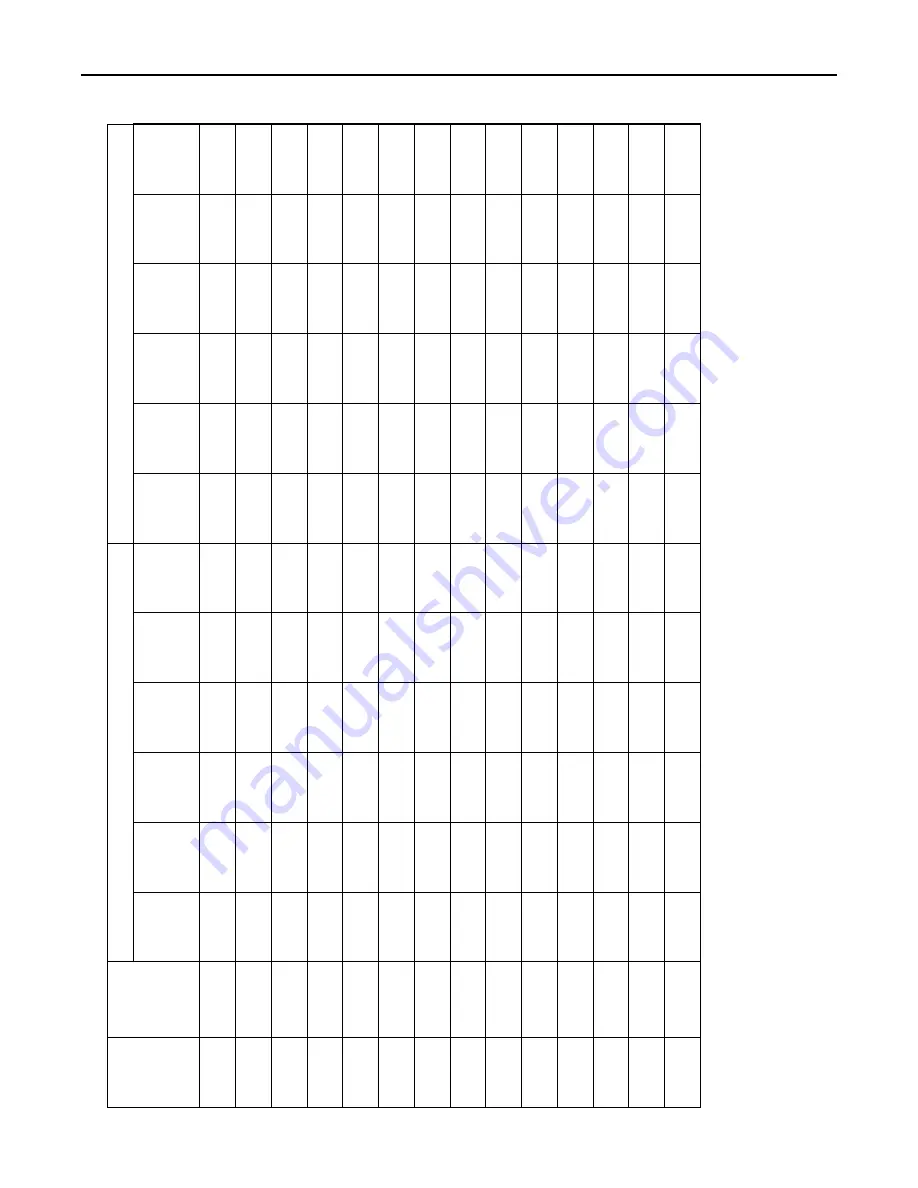
44
RT-SVX51H-EN
Table
24.
Sample
maintenance
log
Date
Current
Ambient
Temp
F/
C
Refrigerant
Circuit
#1
Refrigerant
Circuit
#2
Compr.
Oil
Level
Suct.
Press.
Psig/
kPa
Disch.
Press
Psig/
kPa
Liquid
Press
Psig/
kPa
Super-
heat
F/C
Sub-
cool
F/C
Compr.
Oil
Level
Suct.
Press.
Psig/
kPa
Disch.
Press
Psig/
kPa
Liquid
Press
Psig/
kPa
Super-
heat
F/C
Sub-
cool
F/C
-
ok
-
low
-
ok
-
low
-
ok
-
low
-
ok
-
low
-
ok
-
low
-
ok
-
low
-
ok
-
low
-
ok
-
low
-
ok
-
low
-
ok
-
low
-
ok
-
low
-
ok
-
low
-
ok
-
low
-
ok
-
low
-
ok
-
low
-
ok
-
low
-
ok
-
low
-
ok
-
low
-
ok
-
low
-
ok
-
low
-
ok
-
low
-
ok
-
low
-
ok
-
low
-
ok
-
low
-
ok
-
low
-
ok
-
low
-
ok
-
low
-
ok
-
low
Summary of Contents for Foundation GBC180
Page 50: ...50 RT SVX51H EN N No ot te es s...