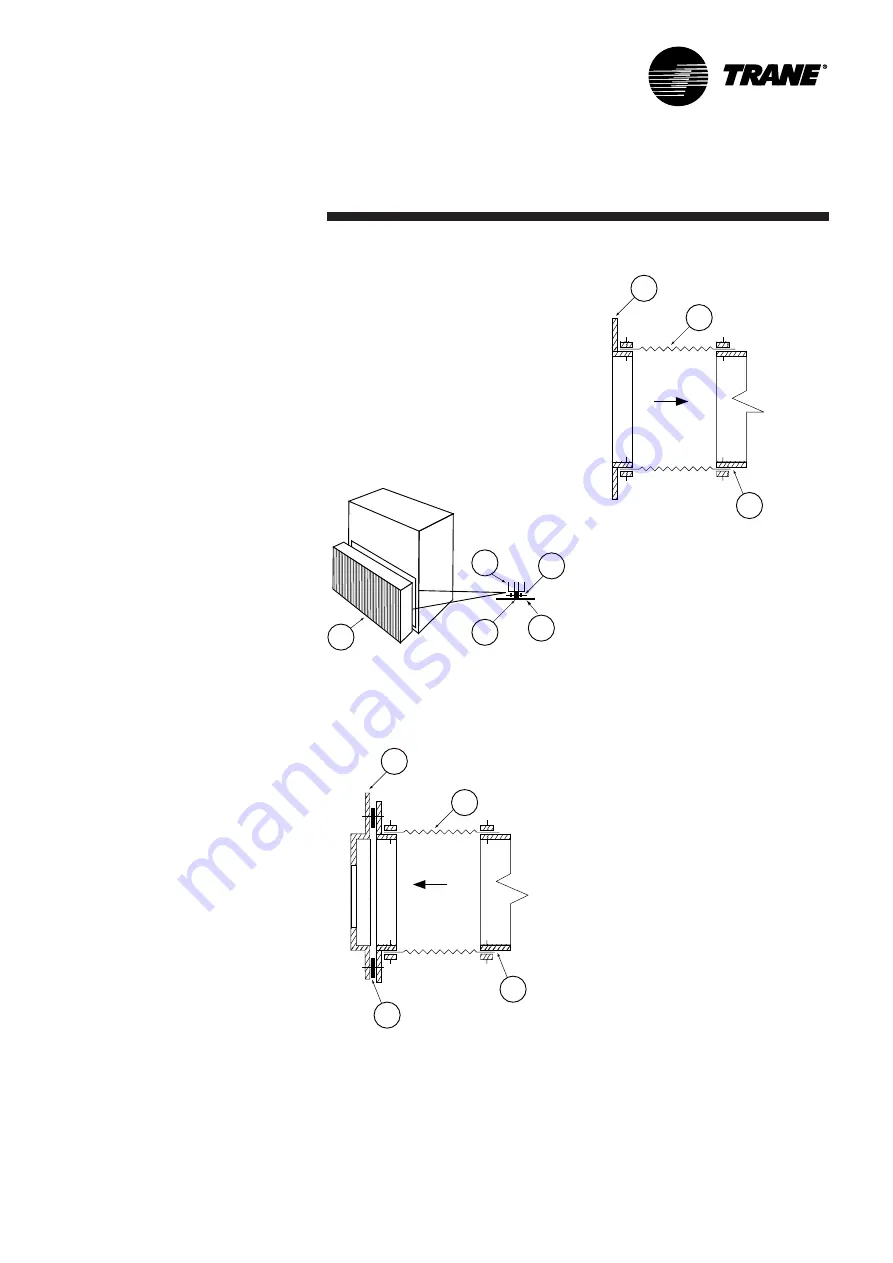
Duct connections
Duct connections of suction and
discharge of the unit and accessories
must be made of flexible hose. The
duct connection must be flexible
enough to prevent transmitting
vibrations to the tube network (see
Figures 2, 3 and 4).
CAUTION!: When fixing the duct to
the condenser inlet, make sure the
fixing screws do not pierce the coil.
Figure 2
1. Accessory
2. Attachment bolts
3. Unit frame
4. Sealing strip
5. Accessory (filter)
Figure 3 - Inlet
1. Unit body
2. Flexible coupling
3. Ductwork
4. Seal
4
1
2
3
CGCL-SVX01B-E4
9
Installation
5
4
1
2
3
Figure 4 - Outlet
1. Unit body
2. Flexible coupling (field supply)
3. Ductwork
To prevent a reduction in fan
efficiency, which would reduce the
air flow and the unit's cooling
capacity, the duct connections must
be designed and connected
according to normal trade practice.
1
2
3
Summary of Contents for CGCL 200
Page 22: ...22 CGCL SVX01B E4 Notes...
Page 23: ...CGCL SVX01B E4 23 Notes...