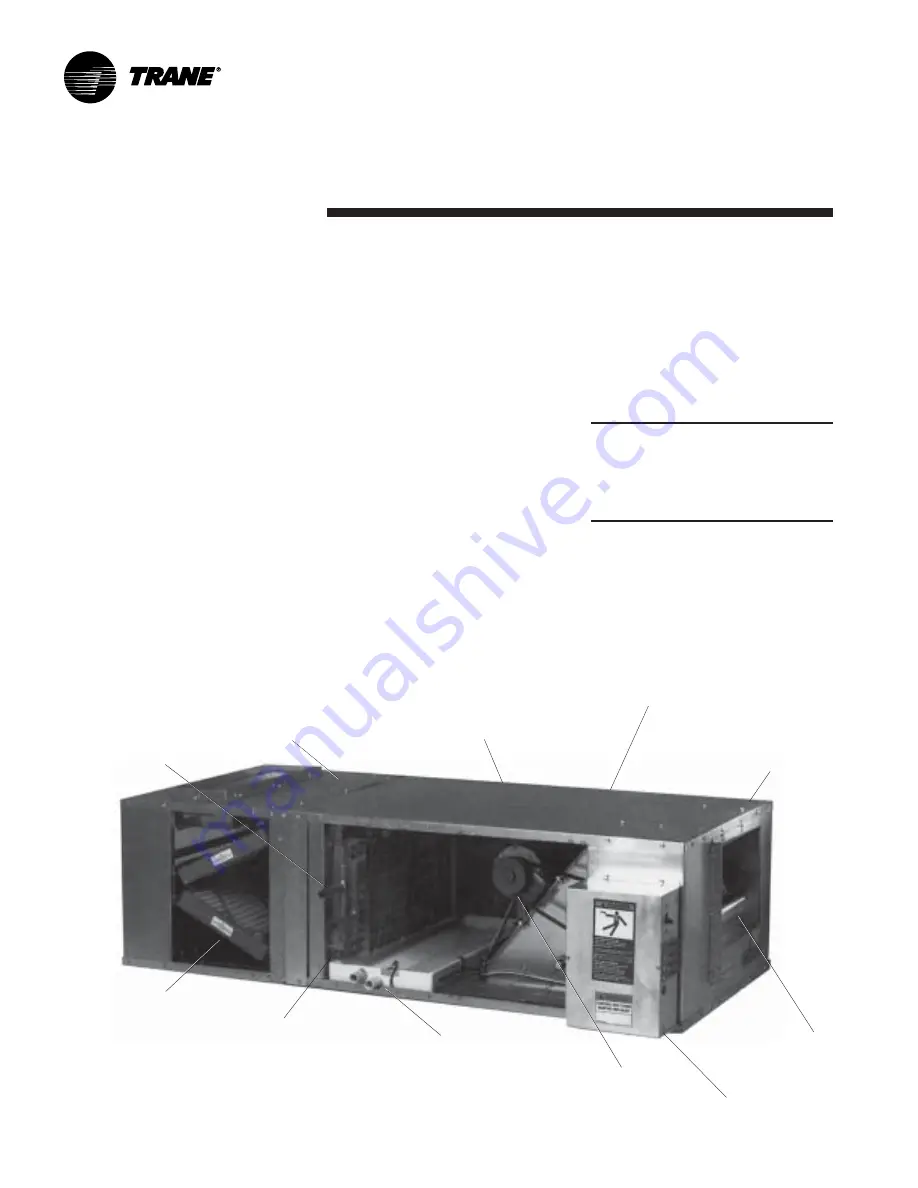
4
BCXC-SVX01A-EN
Figure I-GI-1. Blower coil air handler unit components. Model BCHC, horizontal unit, is shown.
Installation
General
Information
Blower Coil General
Information
Blower coil units are draw-thru air
handlers for cooling load conditions of
400-3000 cfm. Units are available in
either horizontal (model BCHC) or vertical
(model BCVC) configurations. Horizontal
units are typically ceiling suspended via
threaded rods. Knockouts are provided in
all four corners to pass the rods through
the unit. Horizontal units can also be floor
mounted. Vertical units are typically floor
mounted. They have a side inlet for easy
duct connection, and do not require a field
fabricated inlet plenum. Vertical units ship
in two pieces and can be set up in either a
pre-swirl or counter-swirl configuration.
Basic unit components consist of a water
coil, condensate drain pan, filter, duct
collars, one fan wheel, and motor with
drive. See Figure GD-1. Drive compo-
nents consist of sheaves, belt, and motor.
The coil, drain pan, and motor/drive
assembly can easily be field-converted
from right hand to left hand configura-
tions or vice versa.
Two, four, or six-row main coils are
available for either hydronic cooling or
heating. Four or six-row direct expansion
(DX) coils are also available for cooling.
An optional one, two, four, or six-row
heating coil is available factory-installed
in either the preheat or reheat position.
Also, a one-row preheat steam is
available.
All units have an internal flat filter frame
for one or two-inch filters. An optional
angle filter box (two inch only), mixing
box, bottom/top filter access box, or
combination angle filter mixing box is
available.
In addition, all units are available with
either a basic or deluxe piping package
option that includes a variety of control
valve sizes in two or three-way configura-
tions. The basic package consists of a
control valve and stop (ball) valves. The
deluxe package consists of a control
valve, a stop (ball) valve, a circuit setter,
and strainer.
Belt-drive motors range from
1
/
3
to 3
horsepower in a wide range of voltages.
All motors have internal thermal and
current overloads, permanently sealed
ball bearings, and a resilient cradle mount
to reduce noise and vibration transmis-
sion.
Variable pitch sheave drive kit options
help make it possible to more accurately
select design static pressure. For addi-
tional flexibility, 115 volt single phase, two
speed motors are optional.
Note: Sheaves are factory set in the
middle of the range.Field adjustment of
sheaves, motor, and belt are required to
arrive at desired rpm. Refer to the
original sales order and Table GD-1 for
drive information.
Units may have no controls (4 x 4 junction
box) or any of four different control types:
1. control interface
2. Tracer ZN010
3. Tracer ZN510
4. Tracer ZN520
All control options are factoryinstalled
and tested.
Two, four, or six–row
main coil with copper
tubes and enhanced
aluminum fins
Internal filter frame
accomodates one or
two–inch filters
Galvanized steel
cabinet in 14, 18, 22,
and 28 inch heights
Unit sizes 12, 18, 24, 36,
54, 72, and 90 MBh
Knockouts in all four
corners for hanger
rods
Angle filter option
and/or mixing box
accomodates 2–
inch filters
Internal one or two–
row auxiliary coil in
preheat or reheat
position
Main and auxiliary
drain connections on
same side of unit
1
/
4
to 3 hp motor with
drive selections from
400 to 1800 rpm
Control box
Forward curved fan