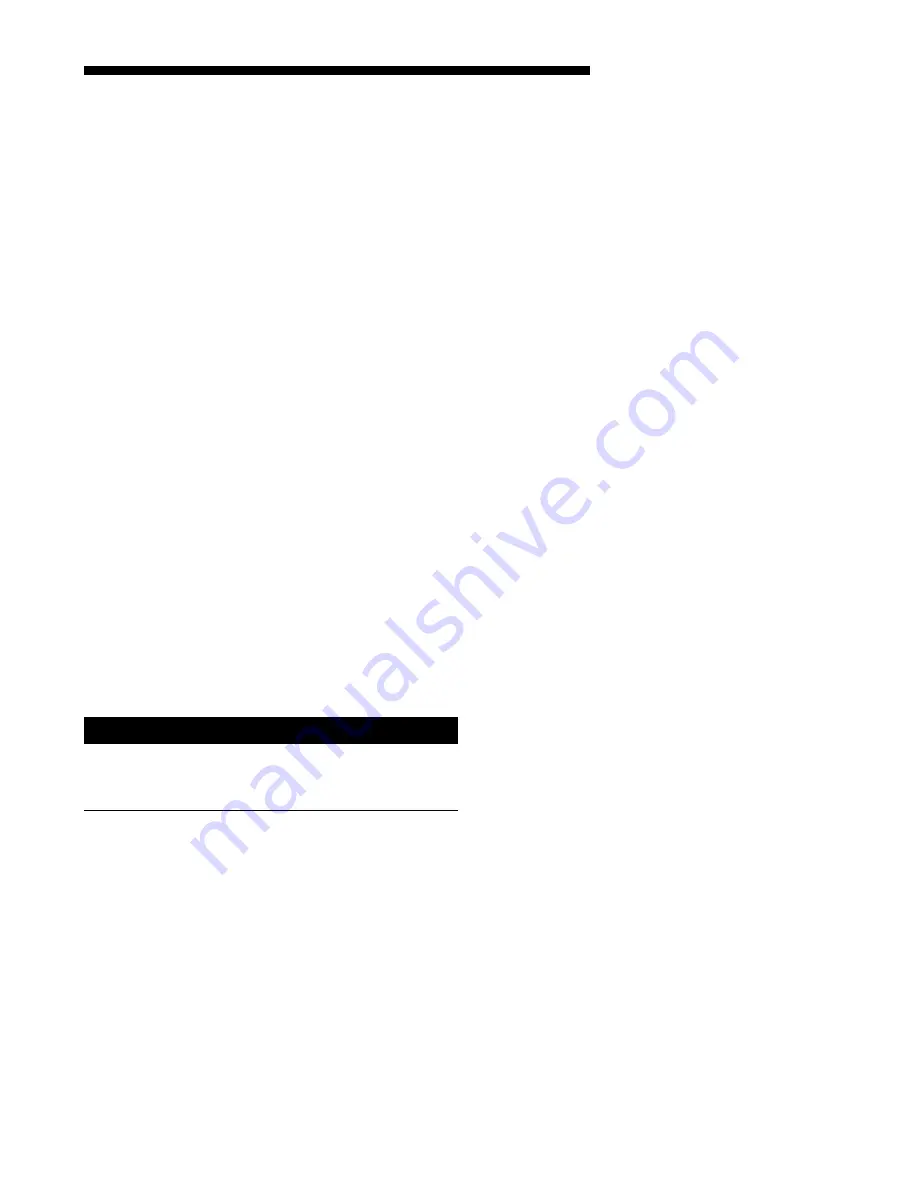
18-CD19D8-18
35
Installer’s Guide
Thermostat call for heat (1-stage Thermostat)
W1/W2 (jumpered) thermostat contacts close signaling a call
for heat. 1st stage sequence of operation remains the same
as above. 2nd stage heat will energize after the stage delay
timer (field selectable at .5, 5, 10 or 15 minutes) has expired.
Thermostat satisfied:
W1/W2 (jumpered) contacts open signaling the control
module to close the gas valve. The induced draft blower is
switched to low speed and de-energized after the post purge
timer has expired. The indoor blower motor will continue to
operate after the flames are extinguished and then is
switched to low heat speed for the FAN-OFF period.
CONTROL AND SAFETY SWITCH ADJUSTMENTS
LIMIT SWITCH CHECK OUT
The limit switch is a safety device designed to close the gas
valve should the furnace become overheated. Since proper
operation of this switch is important to the safety of the unit, it
must be checked out on initial start up by the installer.
To check for proper operation of the limit switches, set the
thermostat to a temperature higher than the indicated
temperature to bring on the gas valve. Restrict the airflow
by blocking the return air (disconnecting the indoor blower
may trip the inducer limit). When the furnace reaches the
maximum outlet temperature as shown on the rating plate,
the burners must shut off. If they do not shut off after a
reasonable time and overheating is evident, a faulty limit
switch is probable and the limit switch must be replaced.
After checking the operation of the limit control, be sure to
remove the paper or cardboard from the return air inlet. Refer
to Service Facts for additional instructions.
NOTE TO INSTALLER
Review the following warnings with the owner. Review con-
tents of USER’S INFORMATION MANUAL with the owner.
AIRFLOW ADJUSTMENT
Check inlet and outlet air temperatures to make sure they
are within the ranges specified on the furnace rating name-
plate. If the airflow needs to be increased or decreased, see
the wiring diagram for information on changing the speed of
the blower motor.
▲
WARNING
!
Disconnect power to the unit before removing the blower
door. Allow a minimum of 10 seconds for IFC power supply
to drain to 0 volts. Failure to follow this warning could
result in property damage, personal injury or death.
This unit is equipped with a blower door switch which cuts
power to the blower and gas valve causing shutdown when
the door is removed. Operation with the door removed or ajar
can permit the escape of dangerous fumes. All panels must be
securely closed at all times for safe operation of the furnace.
INDOOR BLOWER TIMING
Heating:
The integrated furnace control module controls the
indoor blower. The blower start is fixed at 45 seconds after
ignition. The FAN-OFF period is field selectable by dip
switches SW-2, #1 and #2 at 60, 100, 140, or 180 seconds.
The factory setting is 100 seconds.
W1-W2 stage delay (jumpered together) is field selectable by
dip switch SW-1, #1 and #2 at .5, 5, 10 or 15 minutes. The
factory setting is 10 minutes. (See wiring diagram).
Cooling:
The fan delay off period is factory set at 0 seconds.
The option for 80 second delay off is field selectable by dip
switch SW-2, #3 (See wiring diagram).
ROOM AIR THERMOSTAT
HEAT ANTICIPATOR ADJUSTMENT
Set the thermostat heat anticipator according to the current
flow measured, or the settings found in the notes on the
furnace wiring diagram (found in the SERVICE FACTS or
inside the furnace casing).
INSTRUCTIONS TO THE OWNERS
In the event that electrical, fuel, or mechanical failures
occur, the owner should immediately turn the gas
supply off at the manual gas valve, located in the
burner compartment. Also turn off electrical power to
the furnace and contact the service agency designated
by your dealer.
BURNER BOX TEMPERATURE LIMIT DEVICE
All models are equipped with a manual reset temperature
limit located on the burner box. In case of excessive tempera-
ture, the limit will open and cause the circuit to open which
shuts off all flow of gas.