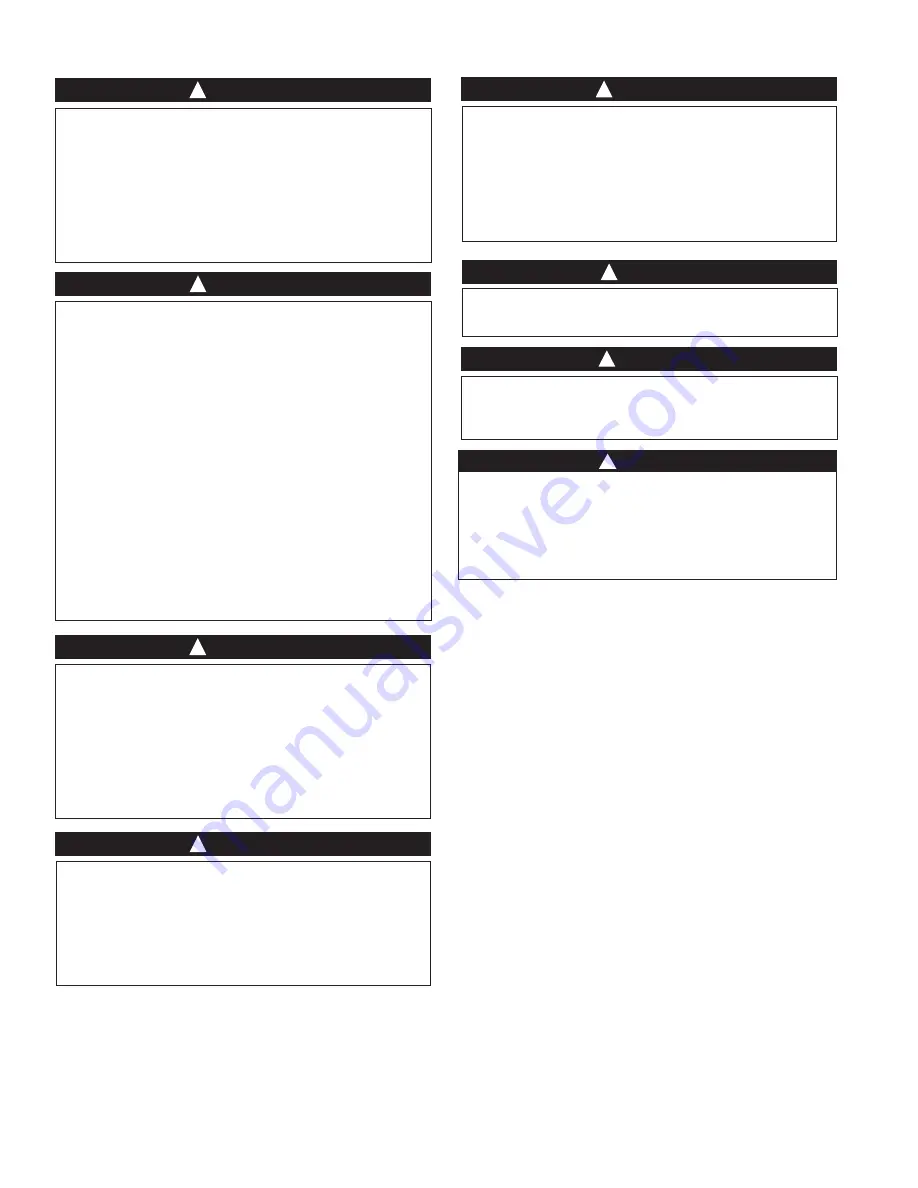
2
88-A4AC4001-1B-EN
Section 1. Safety
WARNING
!
This information is intended for use by individuals
possessing adequate backgrounds of electrical and
mechanical experience. Any attempt to repair a central
air conditioning product may result in personal injury
and/or property damage. The manufacture or seller
cannot be responsible for the interpretation of this
information, nor can it assume any liability in connec-
tion with its use.
These units use R-410A refrigerant which operates
at 50 to 70% higher pressures than R-22. Use only
R-410A approved service equipment. Refrigerant
cylinders are painted a “Rose” color to indicate the
type of refrigerant and may contain a “dip” tube to
allow for charging of liquid refrigerant into the sys-
tem. All R-410A systems use a POE oil that readily
absorbs moisture from the atmosphere. To limit this
“hygroscopic” action, the system should remain sealed
whenever possible. If a system has been open to the
atmosphere for more than 4 hours, the compressor oil
must be replaced. Never break a vacuum with air and
always change the driers when opening the system
for component replacement. For specific handling
concerns with R-410A and POE oil reference Retrofit
Bulletins SS-APG006-EN and APP-APG011-EN or
APP-APG012-EN.
Extreme caution should be exercised when opening
the Liquid Line Service Valve. Turn counterclockwise
until the valve stem just touches the rolled edge. No
torque is required. Failure to follow this warning will
result in abrupt release of system charge and may
result in personal injury and /or property damage.
UNIT CONTAINS R-410A REFRIGERANT!
R-410A operating pressures exceed the limit of R-22.
Proper service equipment is required. Failure to use
proper service tools may result in equipment damage
or personal injury.
SERVICE
USE ONLY R-410A REFRIGERANT AND AP-
PROVED POE COMPRESSOR OIL.
WARNING
!
WARNING
!
LIVE ELECTRICAL COMPONENTS!
During installation, testing, servicing, and trouble-
shooting of this product, it may be necessary to work
with live electrical components. Failure to follow all
electrical safety precautions when exposed to live
electrical components could result in death or serious
injury.
WARNING
!
If using existing refrigerant lines make certain that all
joints are brazed, not soldered.
CAUTION
!
Scroll compressor dome temperatures may be hot. Do
not touch the top of compressor; it may cause minor to
severe burning.
CAUTION
!
WARNING
!
WARNING!
This product can expose you to chemicals including lead,
which are known to the State of California to cause cancer
and birth defects or other reproductive harm. For more
information go to www.P65Warnings.ca.gov
WARNING
!