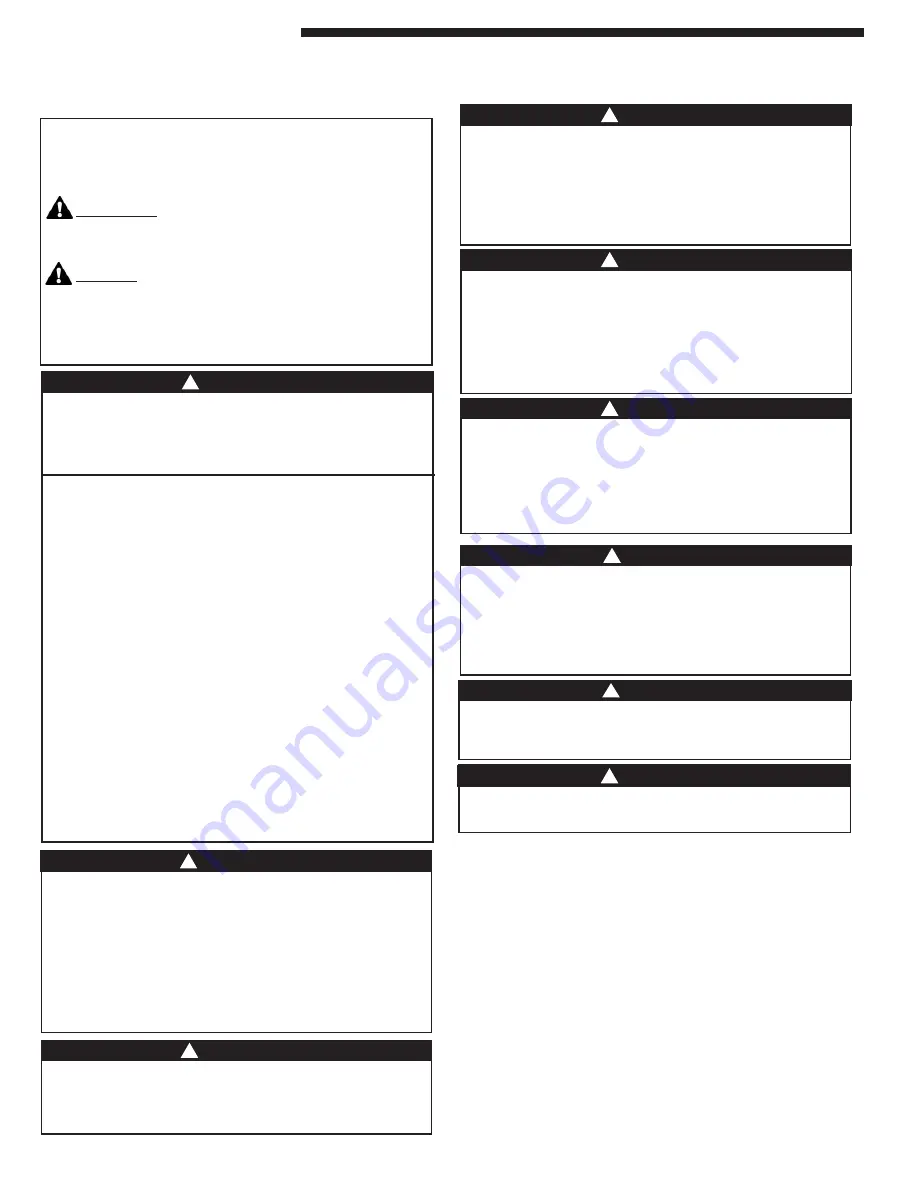
Page 2
Installer’s Guide
IMPORTANT: Read this entire manual before beginning installation procedures.
Safety Considerations
WARNING: INDICATES A POTENTIALLY HAZ-
ARDOUS SITUATION WHICH, IF NOT AVOIDED,
COULD RESULT IN DEATH OR SERIOUS INJURY.
CAUTION: Indicates a potentially hazardous situation which, if not
avoided, may result in minor or moderate injury. It may also be used
to alert against unsafe practices and where property-damage-only
accidents could occur.
NOTICE
Warning and Cautions appear at appropriate locations
throughout this guide. Read these carefully.
EXPLOSION HAZARD!
Propane gas is heavier than air and may collect in any low areas or con-
fined spaces. In addition, odorant fade may make the gas undetectable
except with a warning device. If the gas furnace is installed in a basement,
an excavated areas or a confined space, it is strongly recommended to
contact a gas supplier to install a gas detecting warning device in case
of leak. The manufacturer of your furnace does not test any detectors
and makes no representations regarding any brand or type of detector.
WARNING
!
CAUTION
!
CONTAINS REFRIGERANT!
SYSTEM CONTAINS OIL AND REFRIGERANT UNDER HIGH
PRESSURE. RECOVER REFRIGERANT TO RELIEVE PRESSURE
BEFORE OPENING SYSTEM. Failure to follow proper procedures
can result in personal illness or injury or severe equipment damage.
RECONNECT ALL GROUNDING DEVICES.
All parts of this product that are capable of conducting electrical cur-
rent are grounded. If grounding wires, screws, straps, clips, nuts, or
washers used to complete a path to ground are removed for service,
they must be returned to their original position and properly fastened.
CAUTION
!
Hot Surface!
Do Not touch top of compressor. May cause minor to severe burning.
Unit contains R-410A Refrigerant!
R-410A operating pressure exceeds the limit of R-22. Proper service
equipment is required. Failure to use proper service tools may result
in equipment damage or personal injury.
SERVICE
Use only R-410A Refrigerant and approved POE compressor oil.
PRECAUTIONARY MEASURES
•
Avoid breathing fiberglass dust
•
Use a NIOSH approved dust/mist respirator
•
Avoid contact with the skin or eyes. Wear long-sleeved, loose fitting
clothing, gloves, and eye protection.
•
Wash clothes separately from other clothing, rinse washer thor-
oughly.
•
Operations, such as sawing, blowing, tear-out, and spraying may
generate fiber concentrations requiring additional respiratory pro-
tection. Use the appropriate NIOSH approved respirator in these
situations.
FIRST AID MEASURES
Eye Contact:
Flush eyes with water to remove
dust. If symptoms persist, seek medical
attention.
Skin Contact:
Wash affected area gently with soap and
warm water after handling.
This product contains fiberglass wool insulation! Fiberglass dust and
ceramic fibers are believed by the state of California to cause cancer
through inhalation. Glasswool fibers may also cause respiratory, skin, or
eye irritation.
CAUTION
!
Never use combustible cleaning fluids on any part of the furnace.
EXPLOSION HAZARD!
To prevent an explosion or possible injury, death, and equipment dam-
age, do not store combustible materials, gasoline, or other flammable
vapors or liquids near the unit.
WARNING
!
WARNING
!
WARNING
!
WARNING
!
IMPORTANT:
This product has been designed and manufactured to meet
ENERGY STAR criteria for energy efficiency. However, proper refrigerant
charge and proper air flow are critical to achieve rated capacity and efficiency.
Installation of this product should follow the manufacturer’s refrigerant charging
and air flow instructions.
Failure to confirm proper charge and airflow may reduce
energy efficiency and shorten equipment life.
IMPORTANT:
Do not connect gas piping to the unit until a line pressure test
has been completed. This unit should never be exposed to gas line pressure in
excess of 14 inches water column (1/2 PSIG). The furnace and its equipment
shutoff valve must be disconnected from the gas supply piping system during
any pressure testing of that system at test pressures in excess of 1/2 psi.
IMPORTANT:
Reconnect all grounding devices. All parts of this product capable
of conducting electrical current are grounded. If grounding wires, screws, straps,
clips, nuts, or washers used to complete a path to ground are removed for service,
they must be returned to their original position and properly fastened.
IMPORTANT:
Wear appropriate gloves, arm sleeve protectors, and eye
protection when servicing or maintaining this equipment.
Improper Unit Lift!
Test lift unit approximately 24 inches to verify proper center of gravity
lift point. To avoid dropping of unit, reposition lifting point if unit is
not level. Failure to properly lift unit could result in death or serious
injury or possible equipment or property-only damage.
WARNING
!
IMPORTANT:
Air filters and media wheels or plates shall meet the test require-
ments in UL 900.
RELEASED 10/Aug/2020 16:34:00 GMT